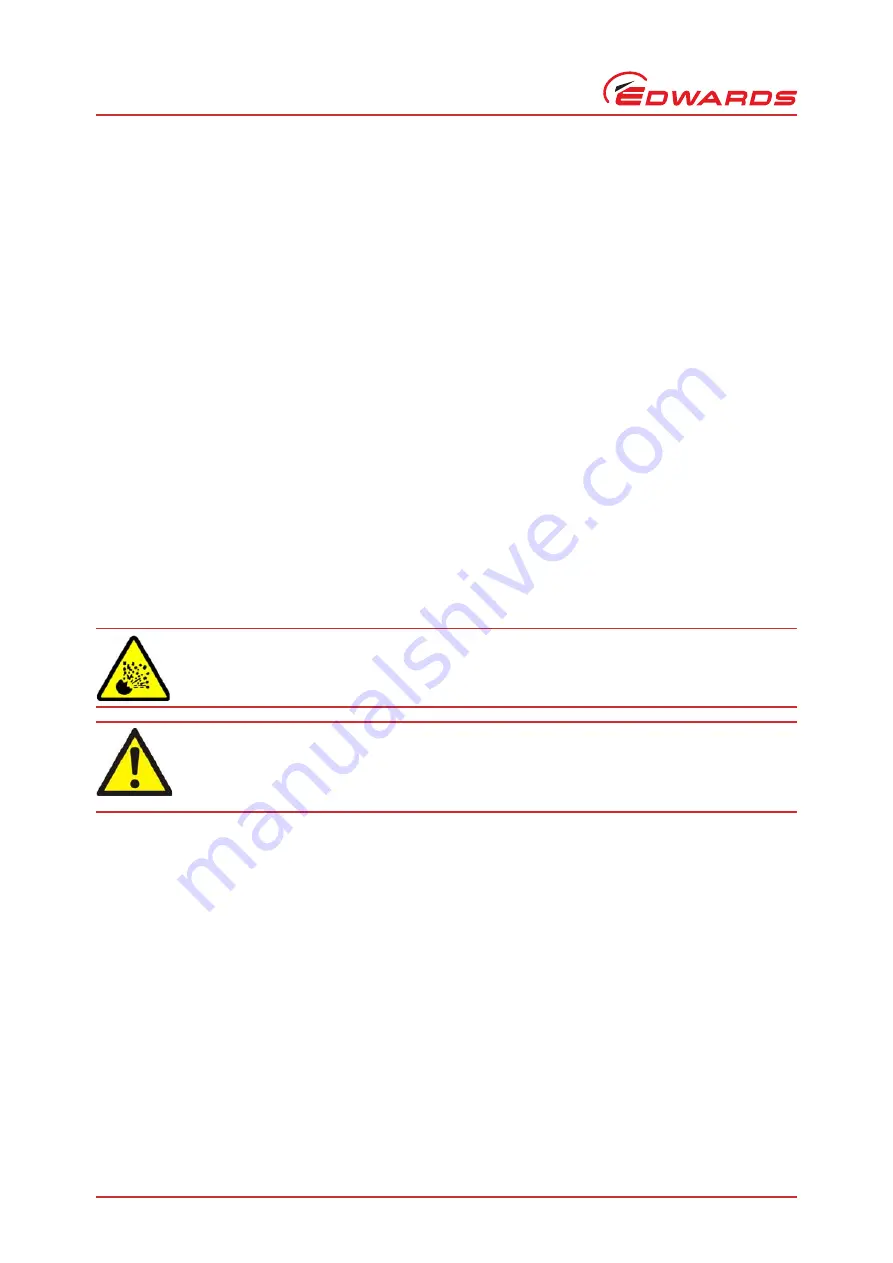
A705-40-880 Issue B
Page 46
© Edwards Limited 2011. All rights reserved.
Edwards and the Edwards logo are trademarks of Edwards Limited.
Maintenance
5.10.3
Check for coolant leaks
Check the pump for obvious signs of a coolant leak (for example, a small stream of coolant at one of the joints on
the pump-body).
If there are signs of a coolant leak, contact your supplier or Edwards for advice.
5.11
Flush the pump with cleaning solution
5.11.1
Introduction
You must use a cleaning solution suitable for the process substances pumped (refer to the warnings at the start of
and
). Note that to completely flood all the unblocked cavities in the pump, you will require
the quantities of cleaning solution shown in
1. Switch on the shaft-seals purge nitrogen supply. If you do not, you will contaminate the lip seals in the pump
when you flush it with cleaning solution.
2. Flush the pump:
Use the procedure in
if you want to remove deposits from a pump which has been operating
correctly.
Use the procedure in
if the pump has seized.
5.11.2
Flush a pump which has been operating
Note:
If the pump has a torque limiter and it has tripped and decoupled the pump-motor from the pump, do not
reset the torque limiter (to recouple the pump-motor to the pump) until you have finished this procedure.
If you leave the pump-motor decoupled from the pump, it will be easier to turn the pump by hand.
1. Refer to
. Remove the four bolts which secure one of the coupling cover guards (14) and remove the
guard.
2. Disconnect the exhaust pipeline from the pump-outlet (25) and place a suitable container under the pump-
outlet.
3. If you have a pump-inlet isolation-valve in your system, close the valve. If you do not have a pump-inlet
isolation-valve, disconnect the pump-inlet (3) from your process system and fit a blanking-flange over the pump-
inlet.
4. Refer to
. Unscrew and remove the blanking plug from the gas ballast purge port (4). Use a suitable tool
to inject the cleaning solution into the port until the cleaning solution comes out of the port, then refit the plug
to the port.
5. Undo and remove the blanking plug from the middle stage purge port (5). Use a suitable tool to inject the
cleaning solution into the port until the cleaning solution comes out of the port, then refit the plug to the port.
WARNING
Use a cleaning solution which is suitable for the process materials pumped. If you do not, there
may be a risk of explosion or pump damage.
WARNING
Ensure that you correctly refit the blanking plugs to the purge ports on the pump. Ensure that the
threads in the purge ports are clean and free from damage, and that the plug is undamaged.
Replace damaged plugs.