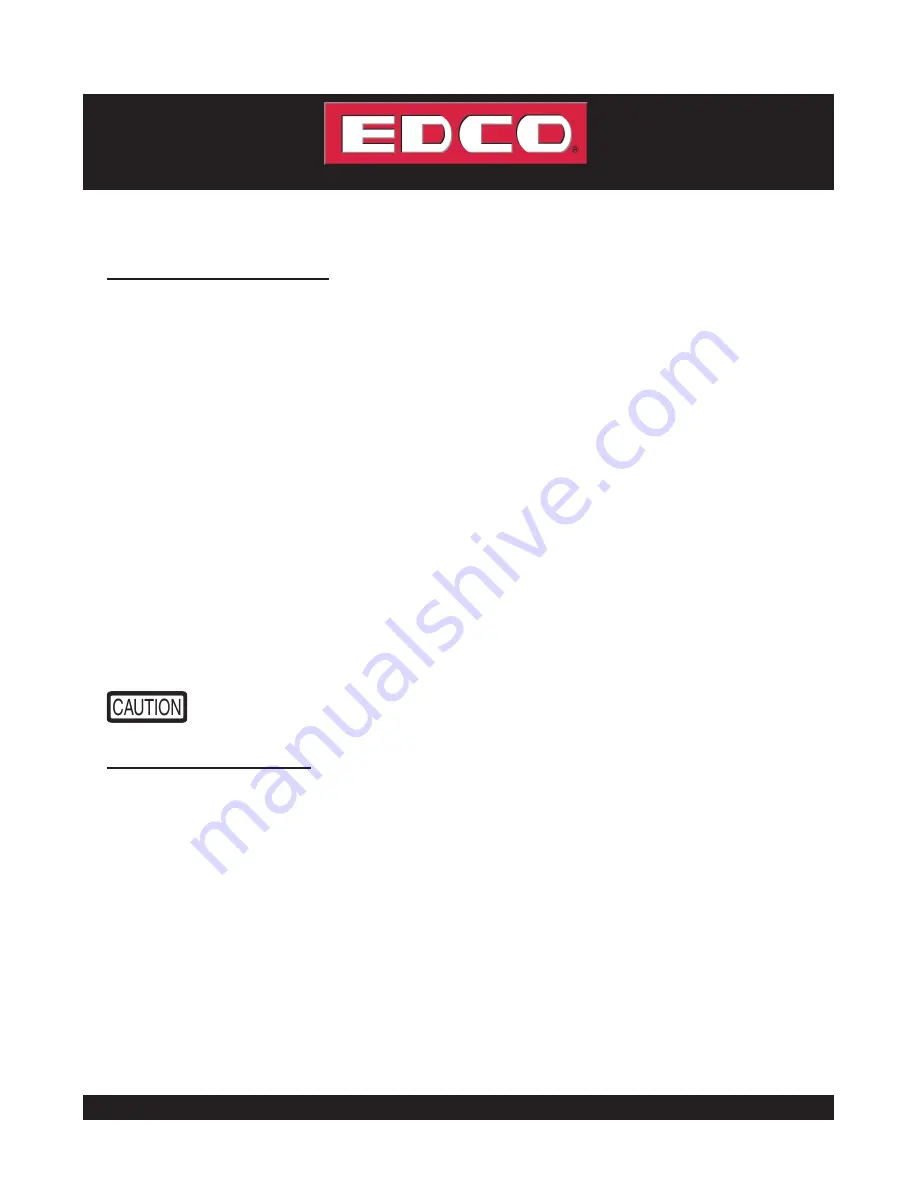
Page 7
E-CPU10FC-I-1117
E-SPTS-I-0809
800-638-3326 • edcoinc.com • [email protected]
EQUIPMENT DEVELOPMENT CO., INC.
Operating Instructions
Before Starting the Machine:
• Perform a visual inspection of the entire machine and all daily maintenance according to the
Maintenance
Schedule
on page 15.
• Locate and be familiar with all engine/motor and operating controls (
Figures 2
).
• For Gasoline models, obtain the
Engine Manufacturer’s Owner’s Manual
. Read it and understand it before con-
tinuing. Follow the engine manual for break-in instructions.
• Use the correct cutters for the job. Be sure cutter drum is balanced, the number, size and type of cutter wheels
are correct and the cutter drum shaft is locked and secured.
• Be sure all fasteners are tight and secure, check for signs of metal cracking or fatigue, inspect for damage to
electrical wiring, damage to fuel lines, check bearings, etc.
• Be sure all guards are in place. Do not operate unless cutter drum guard is in place and secure.
• Inspect work area to determine the presence and location of deck inserts, pipes, columns and objects protrud-
ing from the slab surface so that they may be avoided during operation.
• Adjust the handles for operator comfort and safe operation. Be sure to retighten knobs. (Figure 2, Item 9)
• Raise the cutter head to the full “up” position using the cutter head lever on the console. (Figure 2, item 1)
• Move the machine into operating position by disengaging the clutch (Figure 2, item 2). Lower clutch lever when
unit is in position.
DO NOT disengage clutch when engine is running and cutter drum is in contact with slab surfaces.
Failure to comply could result in serious bodily injury and/or damage to the equipment.
Starting the Engine/Motor:
For Electric Models:
•
Be sure the “OFF” button is depressed on the motor starter box.
•
Hook up the correct voltage/phase electrical power source by plugging into the connector provided. If the cord
does not mate with the connector, consult a qualified licensed electrician before continuing.
•
Verify that the electrical current being supplied is the proper voltage and phase required to run the equipment
• Check motor rotation. Cutter drum rotation on the model CPU-10FC is “upcut.” DO NOT use if drum rotation is
incorrect - have a qualified electrician make the necessary change in the main control panel or motor connection box.
For Gasoline Models:
•
Consult the
Engine Manufacturer’s Owner’s Manual
and follow the directions for starting the engine and allow the
engine to warm up.