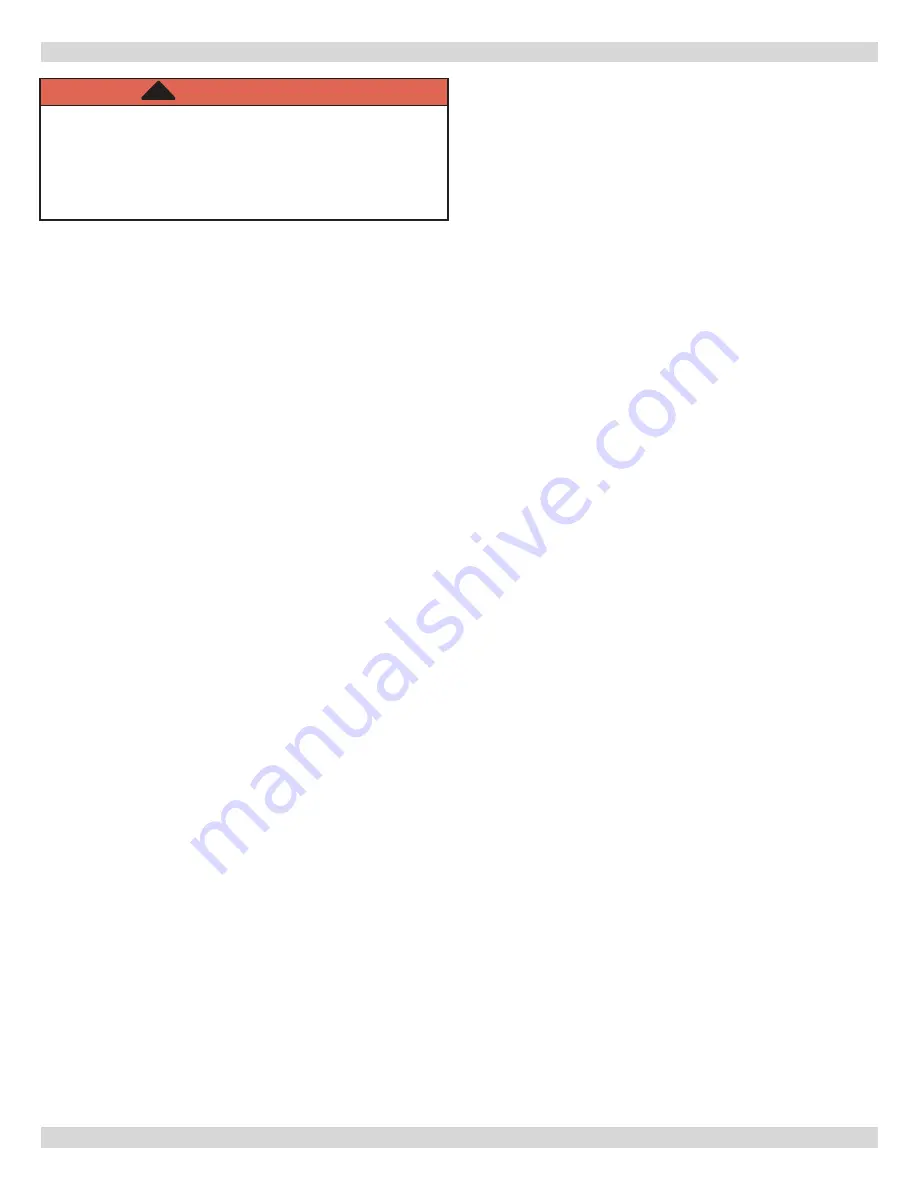
13
5 - WATER CHEMISTRY AND GENERAL ANTIFREEZE GUIDELINES
Boiler Water Quality and Antifreeze
Water treatment and antifreeze protection must be applied
to all aluminum series high efficiency gas-fired boilers
using antifreeze protection.
Clean System First
•
Before connecting boiler to heating system, clean
and flush system thoroughly. Verify system is free of
sediment, flux and residual boiler water additives.
•
Systems having antifreeze not recommended must be
completely flushed to ensure no old antifreeze remains.
In older systems obviously discolored, murky or dirty
water; or pH reading outside acceptable range (between
7.0 and 8.0) are indications system should be cleaned
or treated. Thoroughly flush system with clean water to
remove sediment or contaminants. Sludge and iron oxide
deposits can cause rapid breakdown of inhibitors.
•
Flush with clean water. If chemical cleaners are used,
use only those recommended for use with aluminum
boilers. Follow chemical cleaner manufacturer’s
instructions completely.
•
DO NOT mix different manufacturer’s products.
Fill Water and Chemistry
Verify water used to fill system meets these requirements:
• System fluid pH maintained between 7.0 and 8.0.
•
Maintain water hardness below 7 grains hardness.
•
Filling with chlorinated potable water is acceptable. DO
NOT
fill boiler with water containing chlorine in excess
of 100 ppm.
•
DO NOT use inhibitors or other additives that are not listed.
•
Consult local water treatment specialist for
recommendations if any of above requirements is
outside stated ranges.
Eliminate System Leaks
•
Continuous addition of make-up water will constantly
add oxygen to system. Eliminate all system leaks. All
system leaks must be repaired immediately.
•
Verify expansion tank is operational and properly sized.
Undersized expansion tanks cause relief valve weeping
and substantial make-up water addition.
•
Operation of this boiler in a system containing
significant amounts of dissolved oxygen can cause
severe heat exchanger corrosion damage.
•
This boiler is not designed for use in systems
containing regular additions of make-up water. Regular
additions of make-up water may cause severe heat
exchanger damage. System leaks may not always be
visible. Unseen system leak will become obvious if boiler
pressure decreases when make-up valve is closed.
•
This boiler is designed for closed loop hydronic heat
system only.
Boiler is not suitable for natural gravity
type installations, or any other open type system.
General Guidelines When Using Antifreeze
•
Use only antifreeze products recommended for use with
aluminum boilers. See Table 5 page 14.
•
Continuous addition of make-up water will dilute power
of antifreeze and change buffers ability to maintain pH.
•
Flush old antifreeze from system. Flush boiler and
system separately.
•
Do not use antifreeze unless required.
•
Antifreeze must be of type as listed in this manual due
to their operational characteristics of : type 356 T6
aluminum at operating temperatures between 20°F
(-6.7°C) and 250°F (121°C).
•
Always clean system prior to using antifreeze.
•
Follow antifreeze manufacturer’s instructions for
use, safe handling and storage. Refer to MSDS
(Material Safety Data Sheets) provided by antifreeze
manufacturer for potential hazards and first aid
procedures for exposure or ingestion.
•
Antifreeze will raise pH of hydronic solution in heating
system above recommended level due to corrosion
inhibitors. Solution must be treated to maintain
pH within recommended level. Follow antifreeze
manufacturer’s instructions to adjust pH.
•
If system leaked, adjust water and antifreeze
chemistry. To avoid damage to boiler, check pH
and chemistry of boiler solution. Consult antifreeze
manufacturer for recommendations.
•
Take pH reading annually, and adjust as necessary.
Follow antifreeze/inhibitor manufacturer’s instructions
for details on how to adjust pH.
•
Antifreeze solutions can break down over time.
Failure to check antifreeze chemistry on annual basis
may result in accelerated corrosion of boiler and
other system components. Consult with antifreeze
manufacturer for recommendations.
•
Use of antifreeze in any boiler will reduce heating
capacity as much as 10-20%. Take into consideration
when sizing heating system, pumps and expansion
tank. Consult antifreeze manufacturer’s literature for
specific information on reduced capacity.
•
Using antifreeze manufacturer’s instructions, determine
freezing temperature needed and use correct amount
of antifreeze. Never exceed 50% antifreeze by volume.
•
Boiler operating pressure must remain below 15 psi
for antifreeze solutions that specify maximum of
250°F (121°C). Otherwise, increase system operating/
tank pressure to 20 psig. Refer to expansion tank
manufacturer instructions for adjusting tank
pressure.
WARNING
Fire, explosion, asphyxiation hazard. Inadequate
dielectric isolation, incorrect water treatment or
antifreeze application may cause damage to boilers
heat exchanger. Improper installation could result
in death or serious injury. Follow these instructions
completely.
!
Summary of Contents for Dunkirk Q90-125
Page 41: ...41 Troubleshooting Chart 1 15 TROUBLESHOOTING ...
Page 42: ...42 Troubleshooting Chart 2 15 TROUBLESHOOTING ...
Page 45: ...45 Troubleshooting Chart 5 15 TROUBLESHOOTING ...
Page 50: ...50 NOTES ...
Page 51: ...51 Company Address Phone Company Name Tech Initials Service Performed Date SERVICE RECORD ...