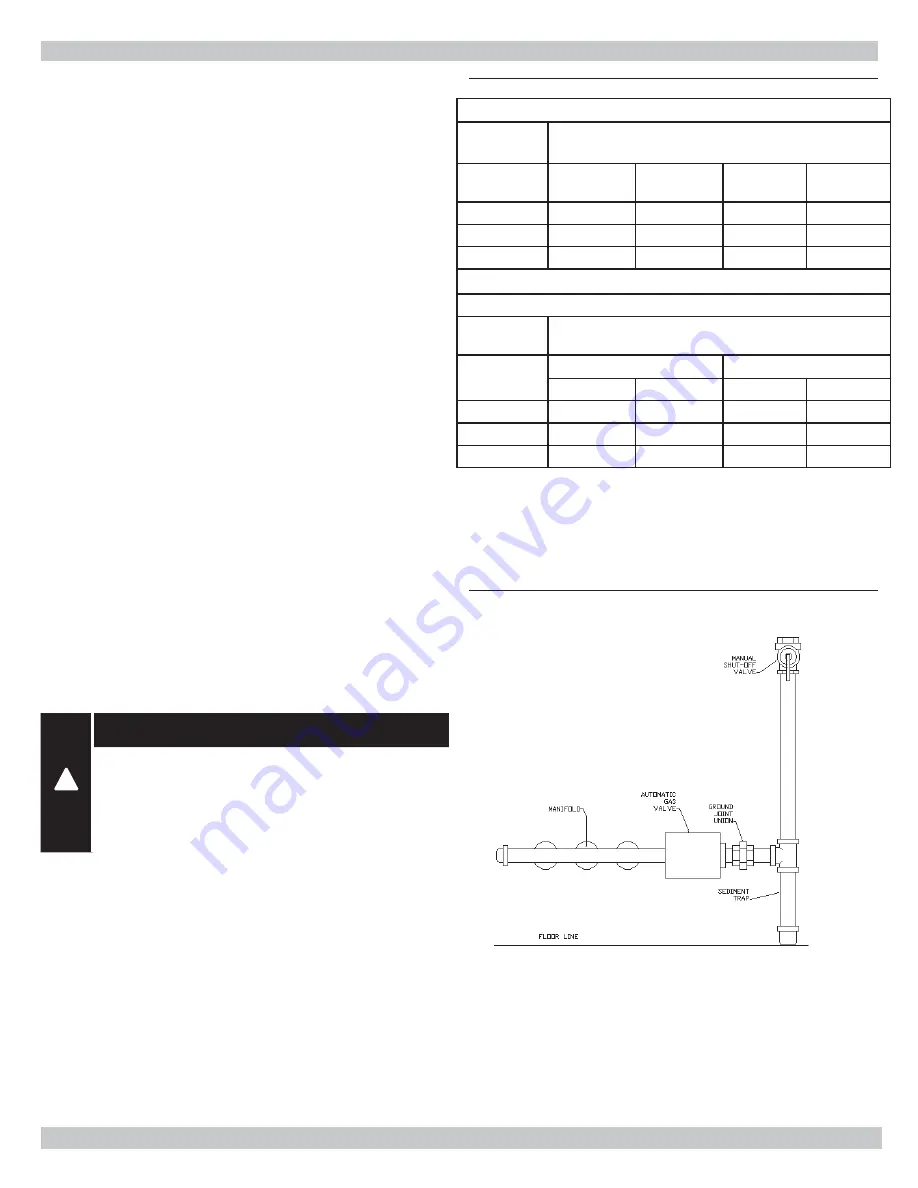
11
GAS SUPPLY PIPING
CHECK GAS SUPPLY
The gas pipe to your boiler must be correct size for
length of run and for total BTU per hour input of all gas
utilization equipment connected to it. See Fig. 12 for
proper size. Be sure your gas line complies with local
codes and gas company requirements.
CONNECTING THE GAS PIPING
Refer to Fig. 13 for the general layout at the boiler.
It shows the basic fi ttings you will need. The gas line
enters the boiler from the right side.
The following rules apply:
1. Use only those piping materials and joining methods
listed as acceptable by the authority having
jurisdiction, or in the absence of such requirements,
by the National Fuel Gas Code, ANSI Z223.1/NFPA
54.
2. Use pipe joint compound suitable for LP gas on
male threads only.
3. Use ground joint unions.
4. Install a sediment trap upstream of gas controls.
5. Use two pipe wrenches when making the connec-
tion to the gas valve to keep it from turning.
6. Install a manual shut-off valve in vertical pipe
about 5 feet above fl oor.
7. Tighten all joints securely.
8. Propane gas connections should only be made by
a licensed propane installer.
9. Two-stage regulation should be used by the pro-
pane installer.
10. Propane gas piping should be checked out by
the propane installer.
CHECKING THE GAS PIPING
!
DANGER
Fire Hazard. Do not use matches,
candles, open fl ames, or other methods
providing ignition source. Failure to
comply will result in death or serious
injury.
Pressure test boiler and gas connection before placing
boiler in operation.
Pressure test over 1/2 psig (3.5 kPa). Disconnect
•
boiler and its individual gas shutoff valve from gas
supply system.
Pressure test at 1/2 psig (3.5 kPa) or less. Isolate
•
boiler from gas supply system by closing manual gas
shutoff valve.
Locate leakage using gas detector, noncorrosive
•
detection fl uid, or other leak detection method
acceptable to authority having jurisdiction. Do
not use matches, candles, open fl ames, or other
methods providing ignition source.
Correct leaks immediately and retest.
•
NATURAL GAS
Pipe Capacity - BTU Per Hour Input
Includes Fittings
Length of
Pipe - FT
½”
¾”
1”
1¼”
20
92,000
190,000
350,000
625,000
40
63,000
130,000
245,000
445,000
60
50,000
105,000
195,000
365,000
PROPANE GAS
Pipe Capacity - BTU Per Hour Input
Includes Fittings
Length of
Pipe - FT
Copper Tubing *
Iron Pipe
⅝
”
¾”
½”
¾”
20
131,000
216,000
189,000
393,000
40
90,000
145,000
129,000
267,000
60
72,000
121,000
103,000
217,000
* Outside diameter
The length of pipe or tubing should be measured from the gas
meter or propane second stage regulator.
FIG. 12 GAS PIPE SIZES
FIG. 13 - GAS PIPING
Summary of Contents for Dunkirk PVWB Series
Page 7: ...7 FIG 6 CHILLED WATER PIPING FIG 5 TYPICAL HOT WATER PIPING INSTALLATION SYSTEM PIPING ...
Page 25: ...25 NOTES ...
Page 26: ...26 NOTES ...
Page 27: ...27 Date Service Performed Company Name Tech Initials Company Address Phone ...
Page 28: ...ECR International Inc 2201 Dwyer Avenue Utica NY 13501 www ecrinternational com ...