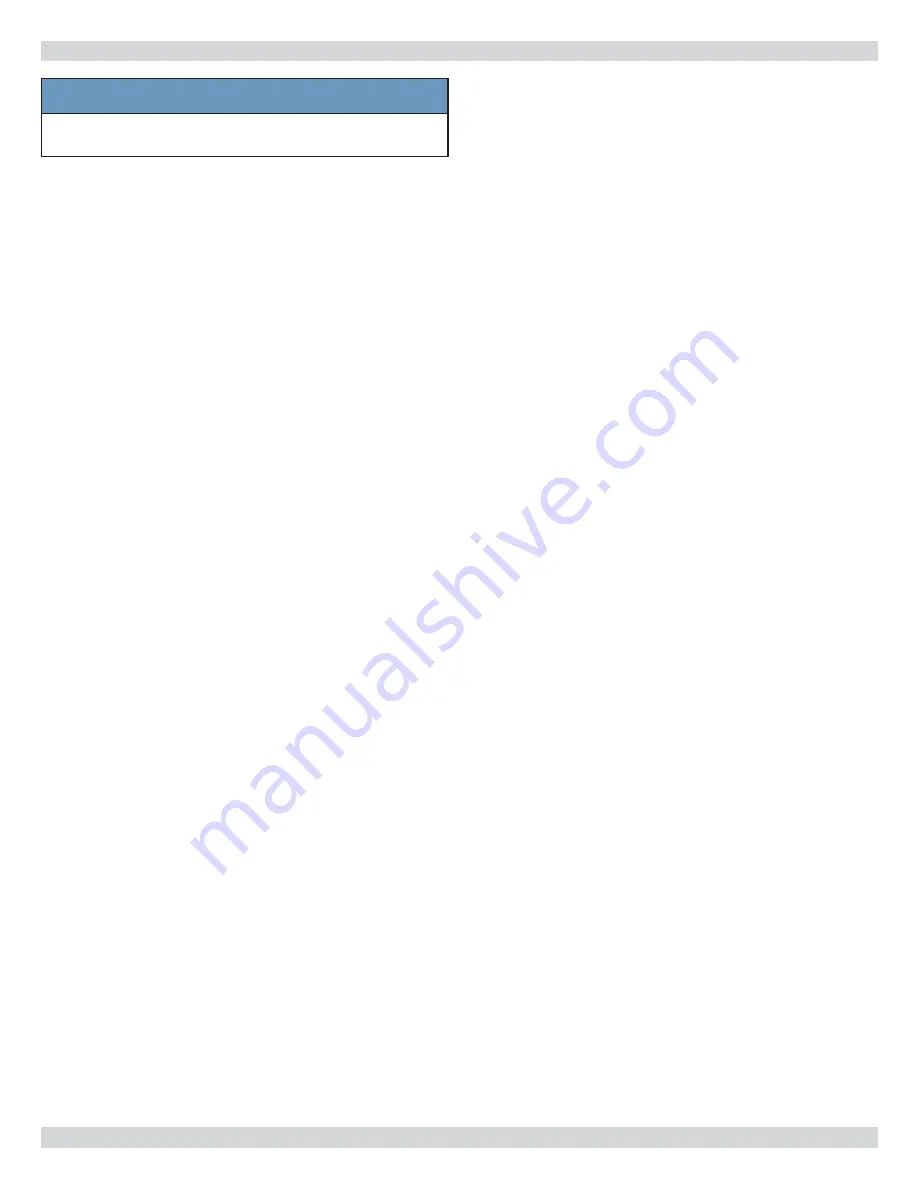
14
Installation
Recommend all pipes be cut, prepared, and pre-
1.
assembled before permanently cementing any joint.
Rigid supports cause excess noise in vent piping.
2.
Attach combustio
3.
n air intake piping to supplied 2”
coupling on CVI gas valve. Attach vent piping to
furnished 2” CPVC vent tee on draft inducer outlet.
All pipe joints are to be water tight.
4.
Working from boiler to outside, cut pipe to required
5.
length(s).
Deburr inside and outside of pipe. Remove all chips and
6.
shavings.
Chamfer outside edge of pipe for better distribution of
7.
primer and cement.
Clean and dry all surfaces to be joined.
8.
Check dry fi t of pipe and mark insertion depth on pipe.
9.
After pipes have been cut and pre-assembled, apply
10.
cement primer to pipe fi tting socket and end of pipe to
insertion mark. Quickly apply approved cement to end
of pipe and fi tting socket (over primer). Apply cement
in light, uniform coat on inside of socket to prevent
buildup of excess cement. Apply second coat.
While cement is still wet, insert pipe into socket with
11.
¼ turn twist. Be sure pipe is fully inserted into fi tting
socket.
Wipe excess cement from joint. Continuous bead of
12.
cement will be visible around perimeter of properly
made joint.
Handle pipe joint carefully until cement sets.
13.
Support combustion air and vent piping minimum of
14.
every 5 feet using pre-formed metal hanging straps. Do
not rigidly support pipes. Allow for movement due to
expansion and contraction.
Slope combustion air and vent pipes toward boiler
15.
minimum of ¼” per linear foot with no sags between
hangers.
Use appropriate methods to seal openings where vent
16.
and combustion air pipes pass through roof or side
wall.
6 - COMBUSTION AIR AND VENT PIPE
NOTICE
Exhaust transition from 2” pipe to 3” pipe must be made
in vertical run. (Transition pieces not included.)
Consider following when determining appropriate
5.
location for termination of combustion air and vent
piping:
Position termination where vent vapors will not
A.
damage plants/shrubs, air conditioning equipment,
or siding on the house.
Position termination so it will not be effected by
B.
wind eddy, air born leaves, snow, or recirculated
fl ue gases.
Position termination where it will not be subjected
C.
to potential damage by foreign objects, such as
stones, balls, etc.
Position termination where vent vapors are not
D.
objectionable.
Put vent on wall away from prevailing winter wind.
E.
Locate or guard vent to prevent accidental contact
with people or pets.
Terminate vent above normal snow-line. Avoid
F.
locations where snow may drift and block vent.
Ice or snow may cause boiler to shut down if vent
becomes obstructed.
Under certain conditions, fl ue gas will condense,
G.
forming moisture, and may be corrosive. In such
cases, take steps to prevent building materials at
vent from being damaged by exhaust of fl ue gas.
Terminate venting system at least 3 feet (0.3m)
о
above any forced air inlet (except boiler’s
combustion air inlet) within 10 feet (3m).
Terminate venting system at least 12 inches
о
(300mm) from any air opening into any building.
Locate bottom of vent at least 12 inches
о
(300mm) above grade.
Terminate vent not less than 7 feet (2.1m) above
о
adjacent public walkway.
Vent terminal shall not be installed closer than
о
3 feet (0.9m) from inside corner of L shaped
structure.
Termination of vent should be kept at least 3 feet
о
(0.9m) away from vegetation.
If multiple terminations are used, minimum of
о
12 inches (300 mm) between exhaust of one
termination and air intake of next termination.
See Figure 8, 9, and 10.
All fi eld installed vent pipe must be 3”.
о
Terminate vent system at least 4 feet (1.22 m) horizontally
from, and in no case above or below, unless a 4 feet (1.22
m) horizontal distance is maintained, from electric meters,
gas meters, regulators and relief equipment.