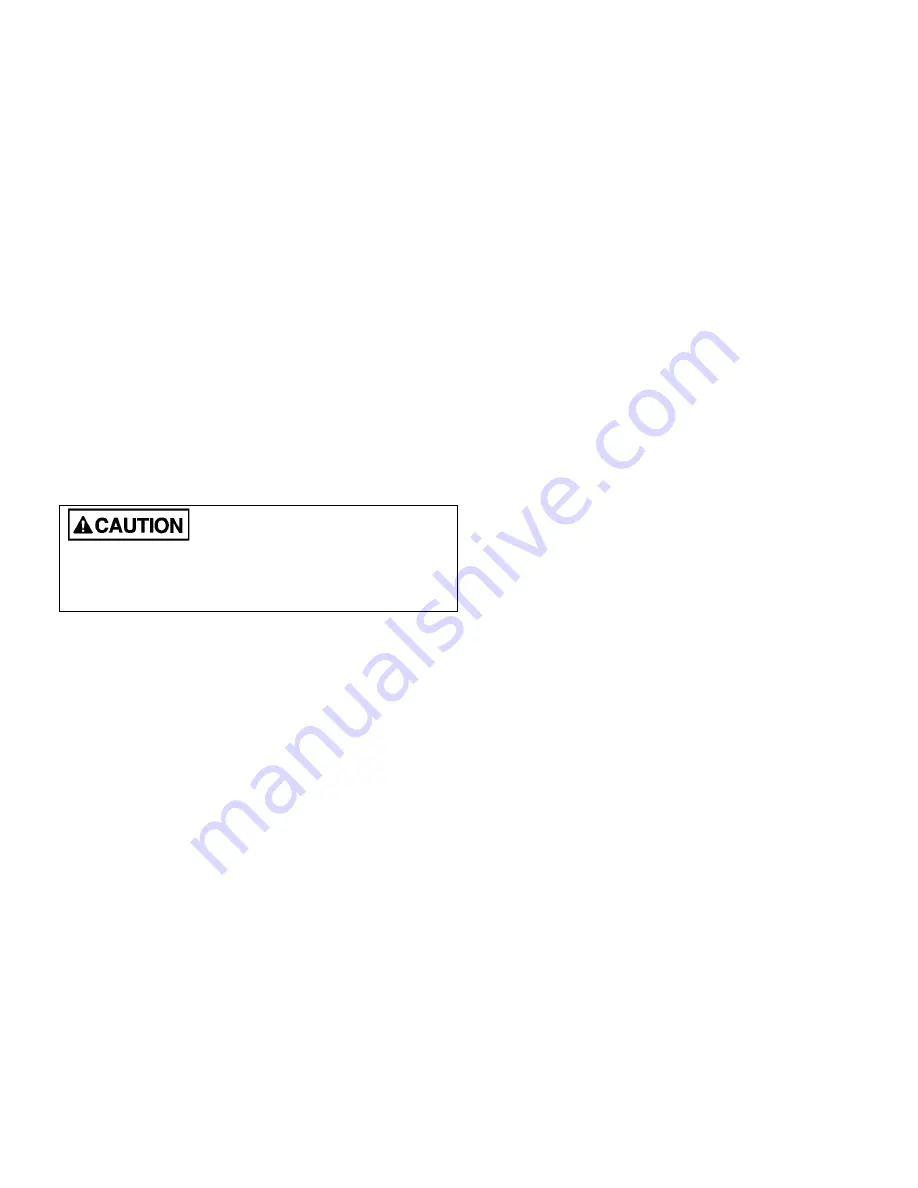
20. MAINTENANCE AND SERVICE
Routine Maintenance By Home Owner
Other than remembering to arrange for the annual
professional servicing of the furnace by the service or
installation contractor, the most important routine service
performed by the homeowner is to maintain the air filter
or filters. A dirty filter can cause the furnace to over-heat,
fail to maintain indoor temperature during cold weather,
increase fuel consumption and cause component failure.
The furnace filter(s) should be inspected, cleaned or
replaced monthly. The furnace is factory equipped with a
semi-permanent type filter. If the filter is damaged,
replace with filters of the same size and type. (See
Appendix A, Table A-8).
During the routine service, inspect the general condition
of the furnace watching for signs of oil leaks in the vicinity
of the oil burner, soot forming on any external part of the
furnace, soot forming around the joints in the vent pipe,
etc. If any of these conditions are present, please advise
your service or installation contractor.
Annual Service By Contractor
THE COMBUSTION CHAMBER (FIREPOT) IS
FRAGILE. USE CARE WHEN INSPECTING AND
CLEANING THIS AREA.
The heat exchanger should be inspected periodically and
cleaned if necessary. If cleaning is necessary,
SHUT
OFF POWER TO THE FURNACE
and remove the
burner. Using a stiff brush with a wire handle, brush off
scale and soot from inside the drum and flue pipe. To
clean the radiator, remove the clean-out caps screws,
and remove the caps carefully to avoid tearing the
gaskets. A wire brush can be used to loosen dirt and
debris on the inside surfaces of the radiator. Clean out all
accumulated dirt, soot and debris with a wire handled
brush and an industrial vacuum cleaner. Before replacing
the clean-out caps, inspect the gaskets. If the gaskets
are broken, remove the remnants and replace with new
gaskets.
The blower motor is factory oiled and permanently
sealed.
DO NOT LUBRICATE
. Excess oil causes
premature electric motor failure.
Inspect the blower fan. Clean if necessary.
Oil Burner Maintenance: Follow the instructions of the oil
burner manufacturer. (See oil burner manufacturer's
instructions supplied with furnace or burner). It is
advisable to change the oil burner nozzle and oil filter on
an annual basis.
The venting system should be cleaned and inspected for
signs of deterioration. Replace pitted or perforated vent
pipe and fittings. The barometric damper should
open and close freely.
All electrical connections should be checked to
ensure tight connections. Safety controls such as
the high limit controls should be tested for
functionality. The fan control should be checked to
ensure that the fan on and off delay function
continues to start and stop the blower fan at the
optimal settings.
21. OPERATING INSTRUCTIONS (HML-C)
Before Lighting
Open all supply and return air registers and grilles.
Open all valves in oil pipes.
Turn on electric power supply
To Light Unit
Set the thermostat above room temperature to call
for heat. The burner should start. NOTE: It may be
necessary to press the RESET button on the
primary combustion control relay.
There will be a fan on time delay before the
circulating fan is energized. The
United
Technologies 1158-120
has an adjustable fan on
time that is set by selecting the dipswitch
combination displayed in Chart 1. This fan on delay
can be set at 1, 2, 4 or 6 minutes.
Set the thermostat below room temperature. The oil
burner should stop.
The air circulation blower will continue to run until
the time off setting selected on the electronic fan
timer control times out. The
United Technologies
1158-120
has an adjustable fan off time of 30, 60,
90 or 120 seconds. The fan timer control
adjustments may be altered if the air at the room
registers is uncomfortably high upon blower start up
or shutdown.
The necessary adjustments to the fan control
settings should be determined by measuring the
temperature of the air in the supply air take-off, or
within the first few inches of the supply air trunk. The
side mid point of the transition is usually ideal,
providing that the thermometer probe is beyond the
"line of sight" wherein false readings from radiant
heat could be observed. System temperature rise is
the difference in temperature between the supply air
and return air
.
To check the operation of the limit switch, shut off
power to the furnace. Temporarily remove the
neutral wire from the direct drive blower motor.
Restore the electrical power to the furnace and set
the thermostat above room temperature.
30173 Rev B 4/29/2008
8
Summary of Contents for HML-C
Page 33: ...30173 Rev B 4 29 2008 33...
Page 34: ...30173 Rev B 4 29 2008 34...
Page 35: ...30173 Rev B 4 29 2008 35...