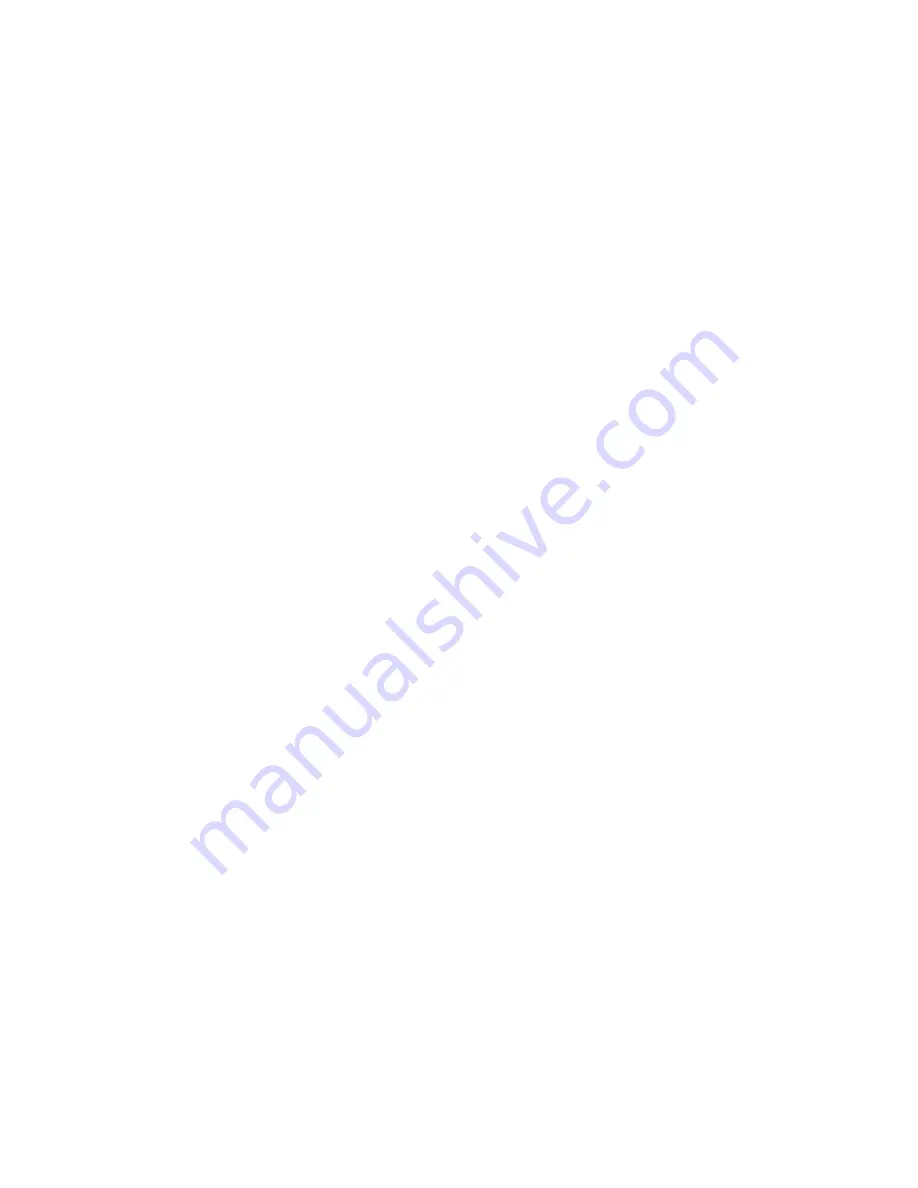
A.2 BURNER ELECTRODES
Adjustment of the electrode tips with respect to each
other, the nozzle, and to the rest of the burner is very
important to ensure smooth start-ups and to permit
efficient combustion.
Beckett AF Burner
Electrode gap: 5/32 inch.
Distance above horizontal centerline: 5/16 inch. Older
instruction sheets specify 7/16 inch. The current
specification is 5/16 inch.
Distance ahead of nozzle: 1/16 inch.
“Z” dimension, the distance from the front of the end
cone (head) to the face of the nozzle should be 1-1/8
inches. If a ceramic head is used, the distance from
the end cone to the nozzle face is increased to 1-3/8
inches.
Riello 40F, & BF Burners
Electrode gap: 5/32 inch.
Distance above horizontal centerline: 13/64 inch.
Distance ahead of nozzle: 5/64 to 7/64 inch.
A.3 START UP
The furnace should be operated for a minimum of 10
minutes to reach steady state conditions before fine
tuning combustion. The warm up time is ideal for
testing the oil pump pressure.
Drill a 1/4-inch test port in the venting between the
furnace flue outlet and draft regulator (barometric
damper). Insert a stack thermometer and note the flue
gas temperature. The flue gases should be within a
range of 350°F to 450°F. If the flue gases are below
the range, it may be necessary to slow down the
blower fan. If the flue gases are above the range, the
blower fan may require speeding up. Stack
temperature varies directly with the system
temperature rise. System temperature rise is the
difference between the furnace outlet temperature and
furnace inlet temperature as measured in the vicinity of
the connection between the plenum take-offs and the
trunk ducts. Temperature rise value is listed on the
system rating plate.
Perform a smoke spot test. The smoke spot should not
exceed No. 1 on the Bacharach Scale.
After the air adjustments have been completed, re-
check the draft pressure at the test port on the burner
mounting plate as shown in Figure 2. The draft should
be adjusted to -0.02 inches w.c.
In the United States, the Beckett AF Burner may be
equipped with Beckett's "
Inlet Air Shut-Off
" to increase
efficiency. (Beckett Part No. AF/A 5861).
NOTE: USE OF THE INLET AIR SHUT-OFF
COULD CAUSE POST COMBUSTION NOZZLE
DRIP.
A.4 SPECIAL INSTRUCTIONS FOR UNITS
EQUIPPED WITH RIELLO BURNERS
Riello burners are factory set with respect to nozzle
size, pump pressure, air gate and turbulator
adjustments for each model and firing rate; therefore,
do not use the above listed set up procedures.
Riello specifications are listed in Tables A-3 and A-4.
Consult the Riello Installation Instructions supplied with
the Burner for specific information concerning burner
adjustments, operation, and trouble-shooting.
30173 Rev B 4/29/2008
12
Summary of Contents for HML-C
Page 33: ...30173 Rev B 4 29 2008 33...
Page 34: ...30173 Rev B 4 29 2008 34...
Page 35: ...30173 Rev B 4 29 2008 35...