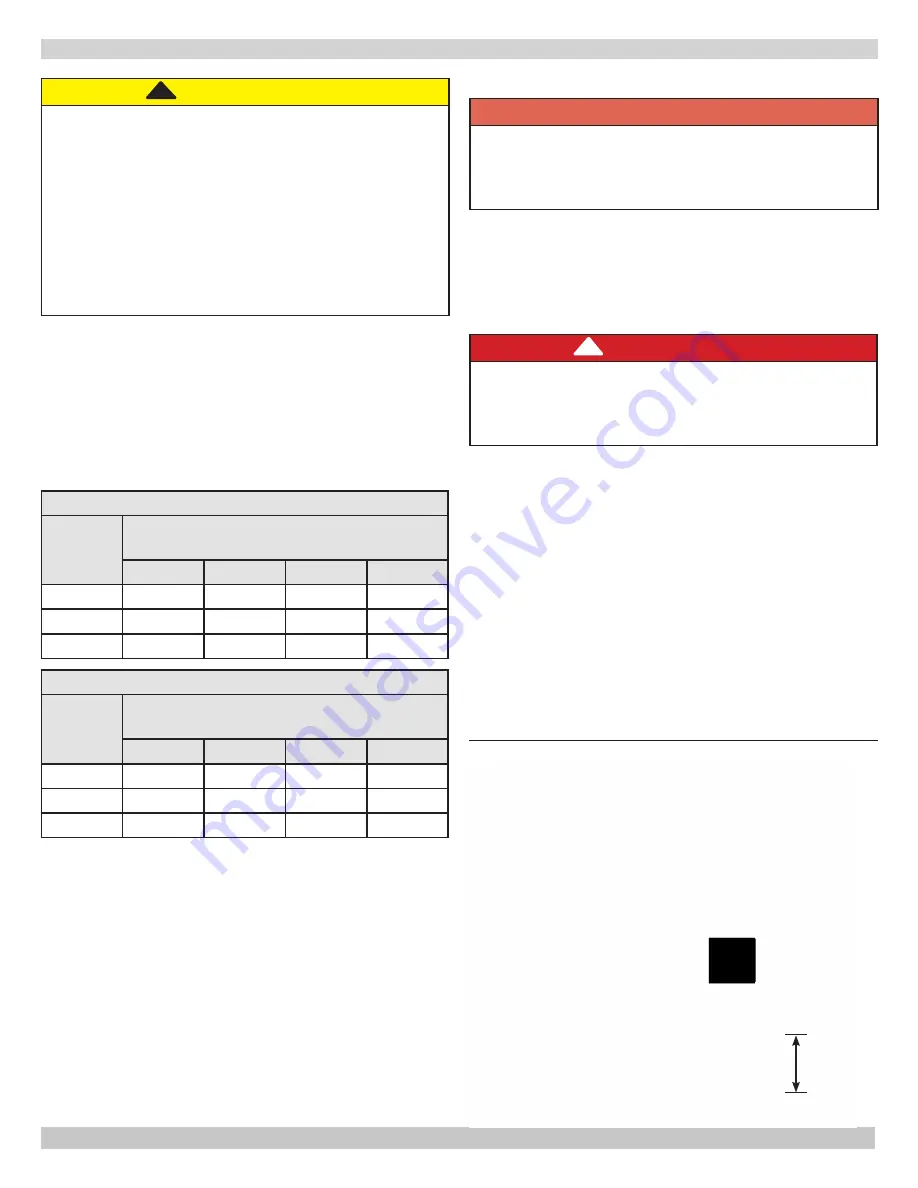
15
GAS SUPPLY PIPING
CAUTION
WHAT TO DO IF YOU SMELL GAS
• Do not try to light any appliance.
• Do not touch any electrical switch; do not use
any phone in your building.
• Immediately call your gas supplier from a
neighbor’s phone. Follow gas supplier’s
instructions.
• If you cannot reach your gas supplier, call the fire
department.
!
General
• Use piping materials and joining methods acceptable
to authority having jurisdiction. In absence of such
requirements National Fuel gas Code, ANSI Z223.1/
NFPA 54.
• Size and install gas piping system to provide sufficient
gas supply to meet maximum input at not less than
minimum supply pressure. See Tables 4a and 4b.
Table - 4a Gas Pipe Sizes - Natural Gas
Length
of Pipe
- Ft.
Pipe Capacity - BTU Per Hour Input
Includes Fittings
1/2"
3/4"
1"
1 -1/4"
20
92,000
190,000 350,000 625,000
40
63,000
130,000 245,000 445,000
60
50,000
105,000 195,000 365,000
Table - 4b Gas Pipe Sizes - Propane Gas
Length
of Pipe
- Ft.
Pipe Capacity - BTU Per Hour Input
Includes Fittings
5/8"
3/4"
1/2"
3/4"
20
131,000 216,000 189,000 393,000
40
90,000
145,000 129,000 267,000
60
72,000
121,000 103,000 217,000
* Outside diameter
Length of pipe or tubing should be measured from the gas meter
or propane second stage regulator.
• Support piping with hooks straps, bands, brackets,
hangers, or building structure components to prevent or
dampen excessive vibrations and prevent strain on gas
connection. Gas valve will not support piping weight.
• Use thread (joint) compound (pipe dope) suitable for
natural and liquefied petroleum gas.
• Install field sourced manual main shutoff valve, ground
joint union, and sediment trap upstream of gas valve.
See Figure 11.
DANGER
Fire Hazard. Do not use matches, candles, open
flames, or other methods providing ignition source.
Failure to comply will result in death or serious
injury.
!
Leak Check Gas Piping
Pressure test boiler and gas connection before placing
boiler in operation. Avoid excessive pressure that could
damage pressure regulators, valves, or meters.
• Pressure test at 1/2 psig (3.5 kPa) or less. Isolate
boiler from gas supply system by closing manual gas
shutoff valve.
• Locate leakage using gas detector, noncorrosive
detection fluid, or other leak detection method
acceptable to authority having jurisdiction. Do not
use matches, candles, open flames, or other methods
providing ignition source.
• Correct leaks immediately and retest.
Figure 11 - Gas Piping At Boiler
Propane Installation
WARNING
Fire, explosion, asphyxiation hazard. Verify boiler
is equipped with propane gas orifices and gas valve
is configured for propane. Failure to follow these
instructions may result in serious injury or death.
• Connections by licensed propane dealer only.
• Use two stage regulator provided by propane
supplier.
• Have propane supplier check piping.
Summary of Contents for GreenMountain GMGS075E
Page 9: ...9 Figure 4 Recommended Near Boiler Piping Using One Supply Tapping SYSTEM PIPING...
Page 27: ...27 REPAIR PARTS...
Page 28: ...28 REPAIR PARTS...
Page 29: ...29 REPAIR PARTS...
Page 30: ...30 REPAIR PARTS Safety Relief Valve 14 11 NPT X 4 Nipple PF 033 02...
Page 31: ...31 Date Service Performed Company Name Tech Initials Company Address Phone...