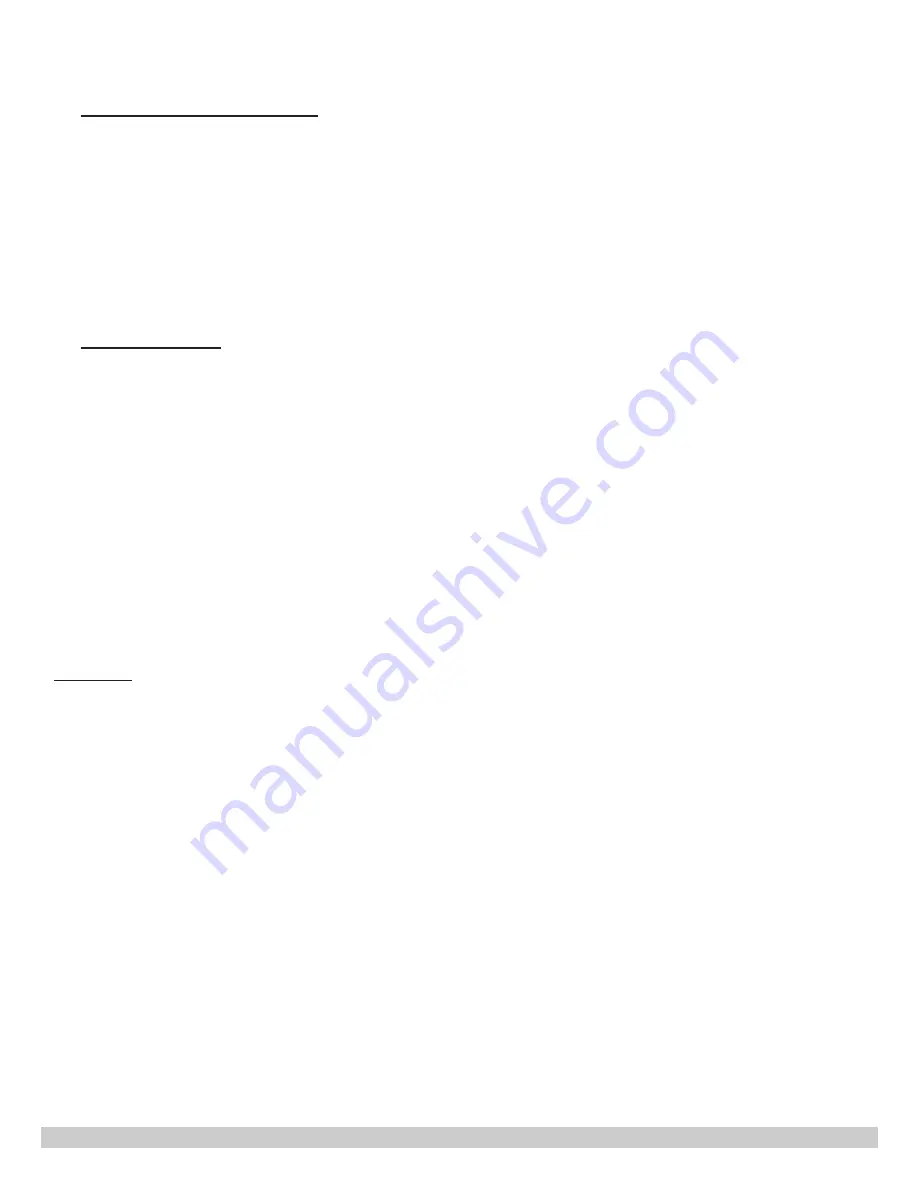
22
PN 240013666 REV. A [06/30/2022]
2.
Energy Management System
- The control can accept an external DC signal from an Energy
Management System (EMS) in place of the outdoor sensor� The control converts the DC signal into the
appropriate boiler target temperature between 50°F (10°C) and 210°F (99°C) based on the EMS Input
Signal and Offset settings. To use the external input signal, the EMS / Demands DIP switch must be set
to EMS� Also, the supply temperature on the boiler controls must be set above 210°F (99°C)�
A� Input signal: The control can accept either a 0 - 10 V (dc) signal or a 2 - 10 V (dc) signal� The
External Input Signal setting must be set to the proper setting based on the signal that is being sent
to the control�
B� DHW/Setpoint operation with external signal: Whenever an external signal is used, the control can
still provide all DHW OR Setpoint functions�
3.
Pump Operation
– The control includes two primary pump outputs with capability for sequencing�
Primary pump sequencing is activated through a DIP switch� Only primary pump 1 is operated when
pump sequencing is turned off, while primary pumps 1 and 2 are operated in stand-by mode when
pump sequencing is turned on�
The running times of the primary pumps are logged in the view menu� To reset these values back to
zero, press and hold the up and down button while viewing this item�
Note: once primary pump sequencing is selected, DHW operation is not available� Setpoint operation,
however, is available if primary pump sequencing is selected�
The primary pumps will operate when the control receives an appropriate demand:
External Boiler Demand
DHW Demand and the control is set to DHW Mode 3, 4, or 6�
Setpoint Demand and the control is set to Setpoint Mode 3 or 4�
The primary pumps also operate when the control is completing a DHW Purge�
Flow Proof
- The control includes a flow proof demand in order to prove flow once a primary pump has
turned on. In order for boiler operation to commence, the proof demand must be present. A flow proof
signal is required at all times during pump operation. A flow proof is generated by applying a voltage
between 20 and 260 V (ac) across the Flow Proof terminals (30 and 31)� Once voltage is applied, the Proof
Demand indicator is turned on in the LCD�
Once a pump contact is turned on, a flow proof signal must be present before the flow proof delay has
expired�
The flow proof demand is selected by setting the Proof Demand item in the Adjust menu to F P (flow proof).
A flow proof demand can come from a flow switch, pressure differential switch, current sensing or power
sensing device�
The control only operates one primary pump at a time. A flow proof device can be used to detect when
stand-by pump operation is required�
Argo AMB Controls