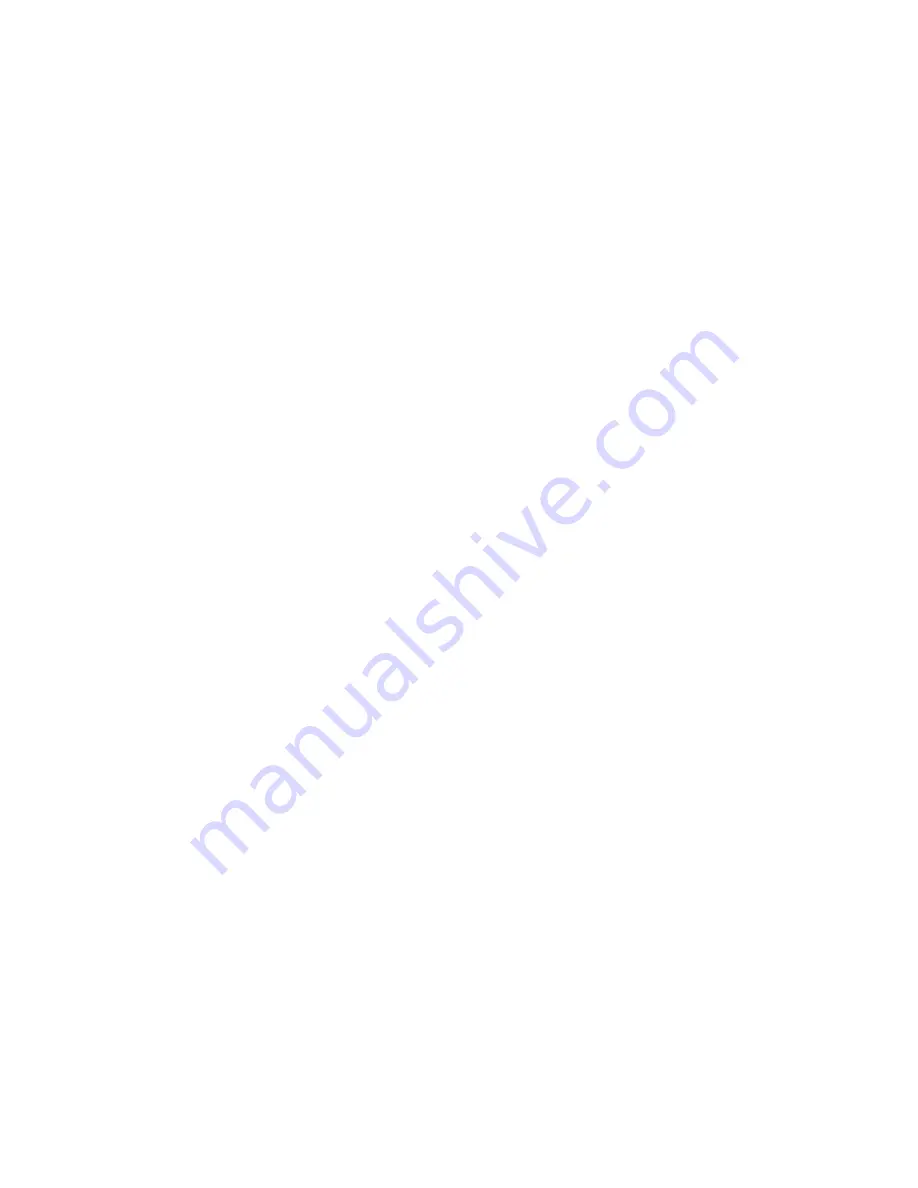
PUMP MOTOR
230V AC/ 0.7Amps/ 80watts (SELNI)
Thermal cut-out fitted
Flow Rate
24ltrs /min / 6.3 gal/min
Pump motor resistance
33 ohms @ 20
0
C / 68
°
F
WATER VALVES
24 Volts DC
Digital Valve
Resistance
64 ohms @ 20
°
C / 68
°
F
Flow Rate
10 ltrs/min - 2.6 gal/min
Proportional Valve
Resistance
64 ohms @ 20
°
C / 68
°
F
Flow Rate
16ltrs/ min - 4.2 gal/min
Operating pressure
Max 1034 kpa (150PSI)
Min
20 kpa (3 PSI)
THERMISTOR
NTC-type temperature sensor
Resistance 10,000 ohms @ 25
°
C / 77
°
F
RECIRCULATING VALVE
Resistance
1.5 Kohms
@ 20
°
C/68
°
F
INNER BOWL SPEED
Other Cycles
Regular Cycle
Fast Spin
1,000 RPM
1,000 RPM
Medium Spin
700 RPM
800 RPM
Slow
300 RPM
700 RPM
Stir Speed
25 RPM
25 RPM
FABRIC SOFTENER DISPENSER
Dosage
75cc
ELECTRIC SUPPLY
120Volts / 60Hz
MAX CURRENT
2.8 amps