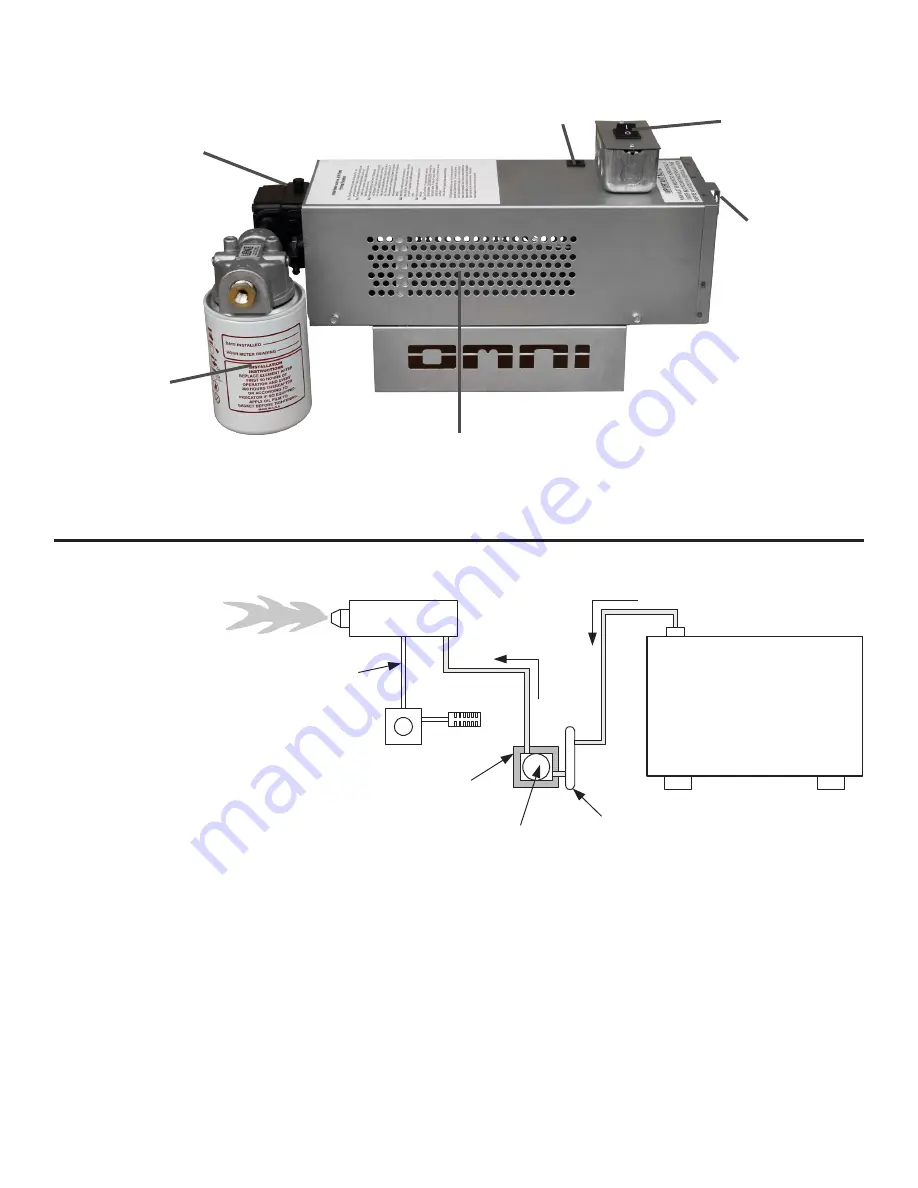
Page 11
OMNI by EconoHeat
Oil Flow Control Supply Pump has the ability to control lame even when various viscosities are
used- furnace or stove oil to 90 weight straight- lame remains stable
Figure 7 –
Oil Pump Assembly
Oil Shut-off Valve
(Eliminates start delays due
to possible drain back)
Spin-On Filter
Oil Primer Switch
(Solenoid valve, on/off)
Adjustable
Motor Speed
(Initial set up only; Once
set, no adjustment
needed thereafter)
Inline Breaker
Oil Burner Technology
OMNI’s patented burner technology improves the eficiency of the oil burn process by
continuous stabilization of the oil viscosity. Optimum atomization (spray) is accomplished
by precisely pre-heating the oil and air prior to introduction to the combustion chamber.
The waste oil enters into the Oil Pre-Heater Block (igure 4) and is pre-heated to operating
thermo setpoint, then compressed air from the air compressor (igure 3) is mixed with the oil
prior to spraying out the nozzle similar to fuel injection, by breaking up the oil droplets into a
iner mist or spray (atomization). Electrodes mounted just above the nozzle (igure 5) provides
continuous electrical arc across electrode to electrode igniting the ine oil mist as it sprays out
of the nozzle. Once ignited the lame is forced into a swirl caused by the burners blower and
specially designed lame cone (igure 5) providing a very eficient and thorough burn of the
waste oil.
DC Motor
Oil Tank
Filter
Flow Control
Oil Pump
Internal Pump Filter
Air Compressor
On Burner
Oil Preheater
Inside Burner
Air Line to Preheater
Mixes with Oil at Nozzle
Suction Line
Pressure Line
Atomization Through Low Pressure
Preheat & Air Induction At Nozzle
Air Filter