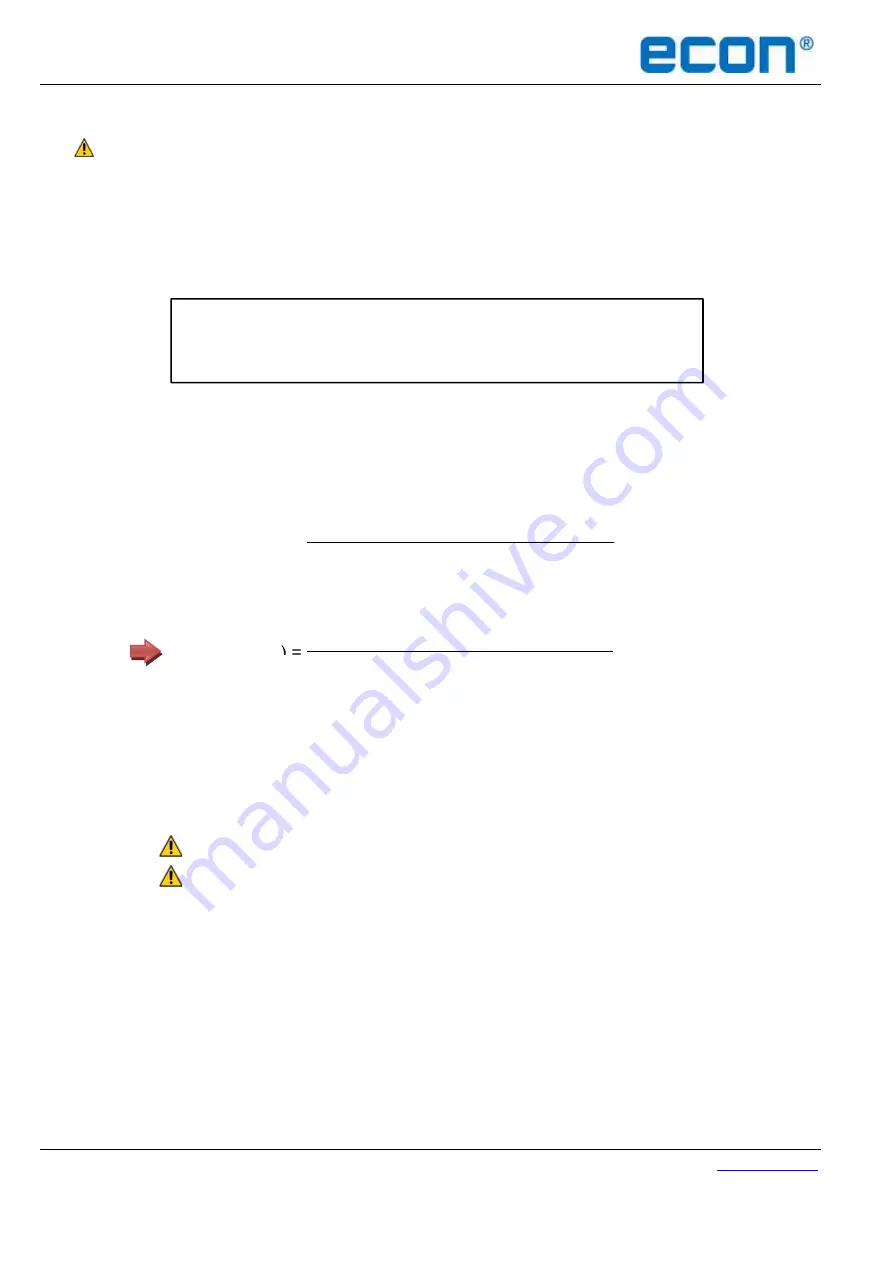
Installation & Operation Manual
ECON actuator Fig. 7917EX, type ELSA50 – 260
www.eriks.com
Rev. 0 – April 10
th
, 2019
9
3.5 Sizing
For safety reasons, do not remove or inspect the SPRING STRUCTURE. Proper
tools must be used or serious injury will occur
The actuator shall be sized to ensure that its torque output meets the operating torque of the
valve and its ability to overcome the required duty cycle of the application (A safety factor of
minimal 30% on top of the required valve torque is recommended).
If the maximum torque of a valve is 80 Nm
80 x 1.3 = 104 Nm
104 Nm < 130 Nm (ELSA130)
OK!
104 Nm > 50 Nm (ELSA50)
NOT OK!
3.6 Duty Cycle – IEC
The duty cycle is the relationship between the running time and resting time. It is
calculated as below:
Duty Cycle = x 100 %
Rest Time (s) =
If the motor running time is 10 s, the spring return time is 5 s and the duty
cycle is 50%, the rest (off) time shall be calculated as below:
Running time: [ 10 s × ( 1 - 50 % ) ] / 50 % = 10, rest time is 10 s
Reset time
:
[ 5 s. × ( 1 - 50 % ) ] / 50 % = 5, rest time is 5 s
One cycle is equal to: open-rest-close-rest
A rest time is required after spring return action because the gear train
and motor are driven during spring release.
3.7 Flame path Joint
The following conditions apply to both certificate numbers SIRA 19 ATEX 1176 X and
IECEx SIR 19.0043X: The flame paths in this equipment are different to the standard
dimensions given in EN/IEC 60079-1. If specific flame path dimensions are required
then the manufacturer (OEM) must be contacted.
Running Time (s) x ( 1 - Duty Cycle)
Duty Cycle
Running Time (s)
+
Rest Time (s)
Running Time (s)