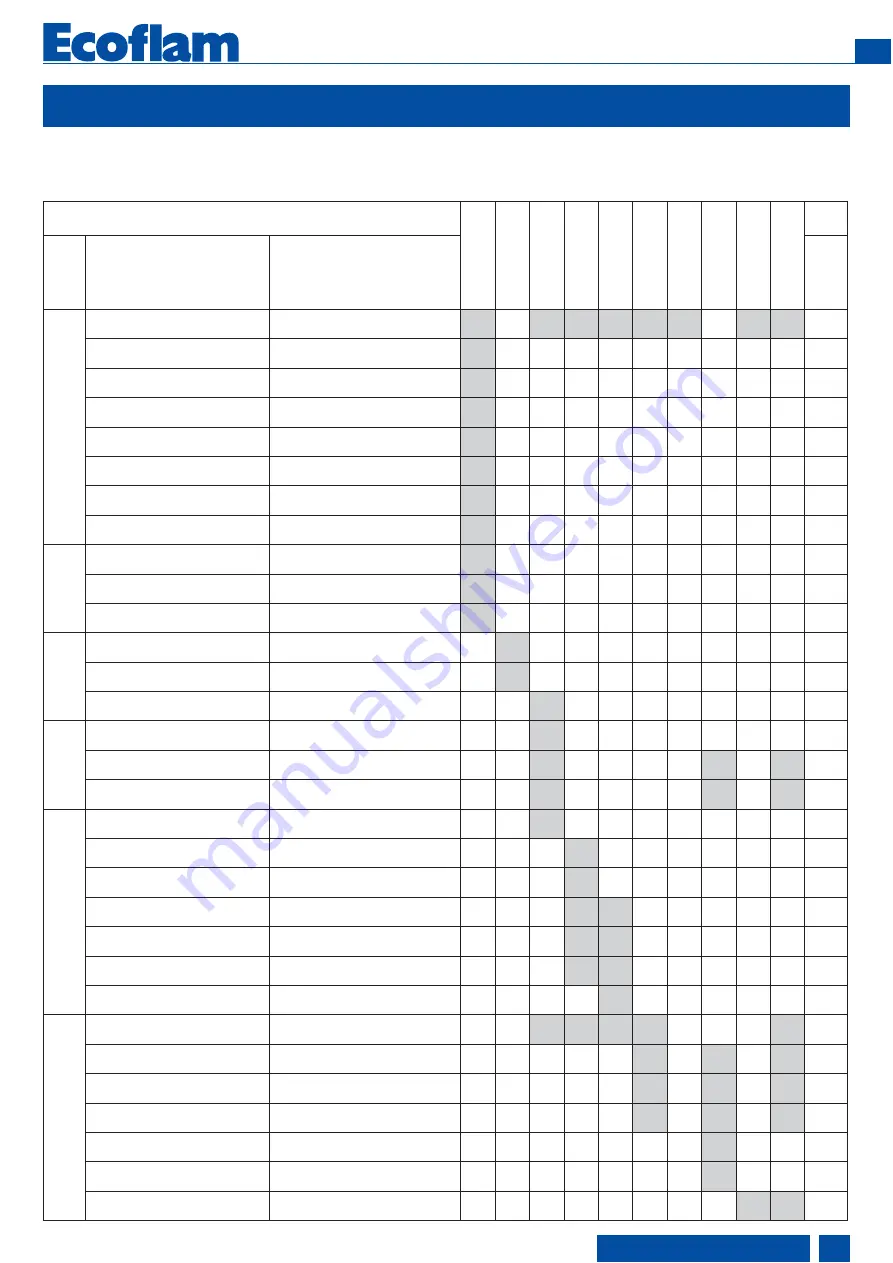
The list of faults/causes/possible solutions for a set of main failures is a guideline for professional personell authorised to carry out
service and maintenance.
Irregular burner operation or malfunction: check that every adjustment parameter is correctly set as per instruction on this manual.
TROUBLESHOOTING INSTRUCTIONS
TROUBLESHOOTING TABLE
GAS OPERATION
Burner doesn't start
Burner starts with continuous pre-purge
Burner starts and then goes into lock- out
Pilot Ignition failure (1st safety time)
Main Ignition failure (2nd safety time)
Burner lock-out after flame appereance / pulsation
Flame control repeats the cycle and does not give consent
Combustion emission not satisfactory
Burner doesn't switch into Hi flame
Burner lock-out during operation
LFL
ST
A
TUS
CAUSES
REMEDIES
MUL
TICALOR
MUL
TIFLAM
BLU
PRE-ST
AR
T
(MISSING SIGNALS)
Defective control box unit
Replace control box unit
X
X
X
X
X
X
X
X
YES
No electrical power supply
Wrong electrical connections
Check switches/contactors
Check connections
X
YES
Air pressure switch not "closed"
Check contacts
X
YES
Boiler thermostats open
Check contacts
X
YES
Fan motor overload intervention
Replace Fuse
X
YES
Auxiliaries fuses interrupted
Replace Fuse
X
YES
Servomotor [CLOSE] position
switch not reach
Check servomotor settings
X
YES
Minimum gas pressure swtich
not close
Open manual ball valve, check
pressure switch settings, contacts,
replace if necessary
X
YES
LEAKAGE
CHECK
Leakage test successful -
signals not arrive to control unit
Check contacts
X
YES
Leakage Test failure (VPS / VDK)
Clean valves or replace leakage
controller if necessary
X
YES
Leakage Test failure (LDU kit)
Check contacts, clean valves or
replace leakage controller if necessary
X
YES
SEQUENCE
ST
AR
T
Servomotor [OPEN] position
switch not reach
Check servomotor settings
X
YES
Servomotor [MIN] position
switch not reach
Check servomotor settings
X
YES
Extraneous light
Eliminate light source
X
YES
LACK
OF AIR
Air pressure switch fail to connect
to Terminal 14
Check contacts
X
YES
Fan contaminated / dirty
Clean fan
X
X
X
YES
Fan motor rotation direction
not correct
Check direction and contactor
X
X
X
YES
IGNITION & FLAME
ST
ABLISA
TION PERIOD
Flame supervision circuit internal
test failed
Replace control unit
X
YES
Pilot flame failure - Pilot gas valves
not open
Check valves contacts / replace if
necessary
X
YES
Pilot flame establish - weak flame
signal
Check Ionisation or flame sensor
Replace if necessary
X
YES
Ignition transformer faulty
Replace
X
X
YES
Ignition cable & electrodes defective
Replace
X
X
YES
Electrode bad position
Check setting / replace if necessary
X
X
YES
Main solenoid valve fails to open
Check contacts and clean valves
Replace valves if necessary
X
YES
COMBUSTION
Flame sensor signal failure
Clean, re-position or replace if
necessary
X
X
X
X
X
YES
Head adjustment not correct
Check settings
X
X
X
YES
Gas / Air mixture setting not correct
Check settings
X
X
X
YES
Oscillating gas pressure
Install damping throttle (AGA 25) -
order separately or reduce suppply
pressure
X
X
X
YES
Capacity reduction due to lower
gas supply pressure
Check gas pressure, clean filter,
replace cartridge if necessary
X
YES
Gas pressure regulator
not regulating
Replace regulating valve
X
YES
Load control device does not close
Check load control,
replace if necessary
X
X
YES
420010487501
EN
www.ecoflam-burners.com
23