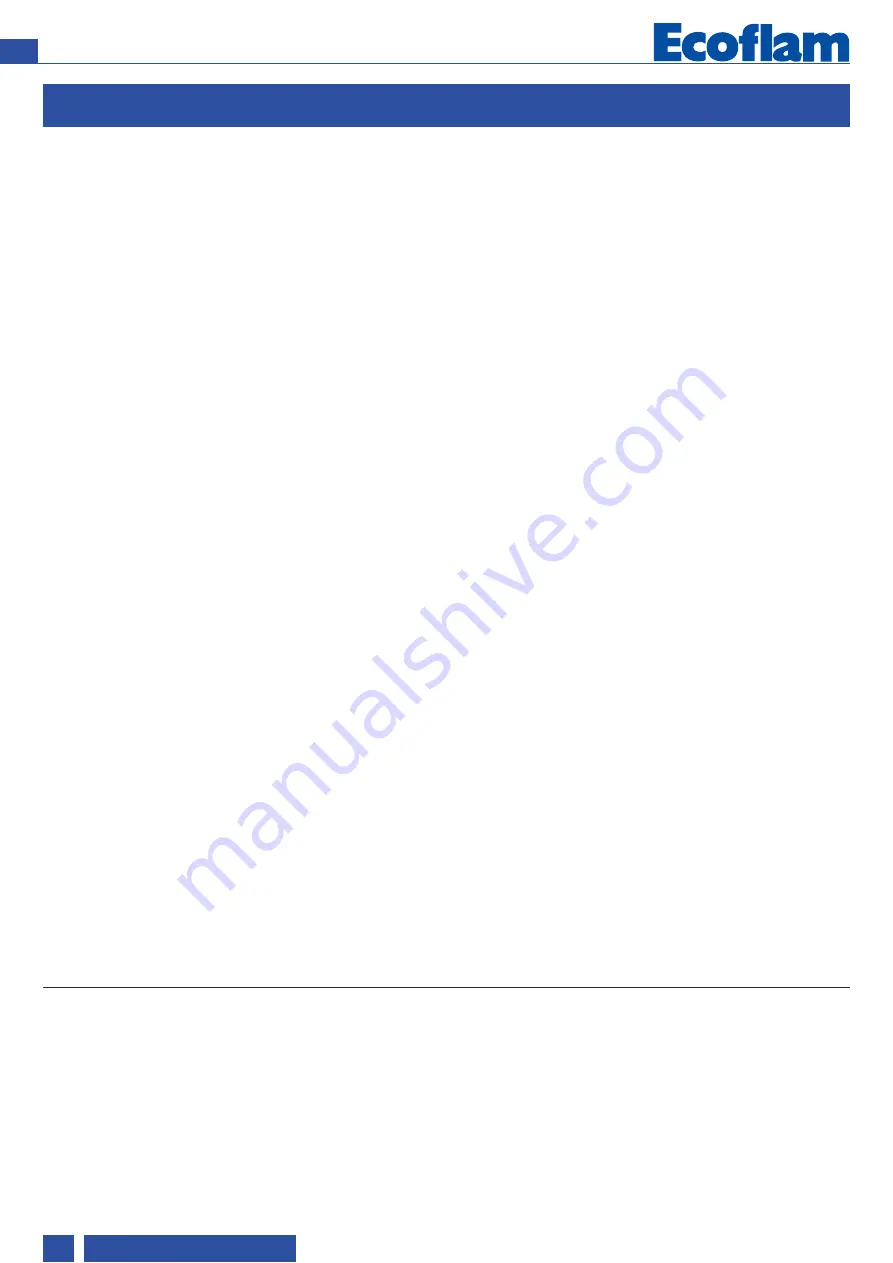
10
www.ecoflamburners.com
EN
420010930200
GAS OPERATING MODE GENERAL SAFETY FUNCTIONS
STARTUP MODE
As soon as the furnace system is required
to supply heat, the burner control circuit
will close and the program flow started.
When the program has come to its end,
the burner will be turned on.
An automatic test is made for the tightness
of the gas valves prior to each burner start.
The air damper is in its closed position
when the burner is out of operation.
The electric actuator will open the closed
air damper to its full-load position so that
the burner will ventilate the furnace and
the exhaust hoods with the specified air
rate.
Shortly after the preventilation process has
been started the lack-of-air cut-out must
change over to operating position within a
certain time, i.e. the minimum air pressure
setting must be reached and maintained
until the burner is turned off. At the end of
the specified pre-ventilation time the air
damper will be moved into its partial-load
position in a linked control concept with the
gas damper.
The ignition transformer will be started.
At the end of the pre-ignition time the gas
valves will be opened to allow gas to flow
into the burner.
The ignition electrodes incorporated in the
burner will ignite the ignition gas.
The UV cell gives flame signal to
control box so that the safety shut-off
valves will be opened.
The gas will be fed to the gas nozzles via
the gas damper while combustion air is
supplied by the fan.
Gas and air will be intensively mixed in the
mixing unit and ignited by the spark.
After the safety period has run down the
ignition spark will be turned off.
Attention:
If there are shut-off dampers in the flue
gas tract they must be completely open.
Otherwise there will be a high danger of
low-speed detonation or explosion!
GAS OPERATING MODE
After the flame has developed the load
regulator will be enabled which brings the
burner into its operating position.
The load regulator will now control the
burner automatically between its partial-
load and full-load stages. Depending on
the heat demand, the electric actuator of
the compound control system will be fed
with the OPEN or CLOSE command via
the regulator and thus increase or
decrease the gas and air flow rates.
This compound control system will vary
the positions of the gas control valve and
air damper and thus regulate the gas flow
rate in a linked concept with the air flow
rate. The burner can either be controlled
by a 2-stage sliding or, if a respective
controller is provided, a stepless control
concept.
The stepless control will allow the burner
to be operated at any desired stage
between its partial-load and full-load
positions.
The burner will always be turned off out of
its partial-load position.
The air damper will be closed when the
burner is out of operation and will thus
prevent cold air flowing through the burner
chamber, heat exchanger and chimney.
The interior cooling losses will thus be
greatly minimized.
GAS LEAKAGE CONTROL FOR
BURNERS IN PRE VERSION
The relevant function is ACTIVE as a
standard. Before commissioning the
burner, please check is this feature is
“ACTIVATED” (look inside menu on
section 5 “Operating Control and
Displays”page 64, fig.5-32”).
If it is “NOT ACTIVATED” and it is not
mandatory to fit the valve proving, a
suitable gas train must be fit. Such a gas
train must be equipped with a pressure
switch upstream of the first gas valve
(referring to the picture on page 12, the
313 min. gas pressure switch must be fit
after the device 144).
It works as follows:
The valve leakage test checks whether the
main gas valves are leak-tight. The supply
gas pressure is used for this purpose.
Since the valve leakage test line (space
between the two main valves) burns empty
in the event of a shut-off, this part is
normally without pressure when starting
(gas pressure > min. = 0). The FA1 checks
this. Main gas 1 is then opened shortly and
gas flows into the test line (gas pressure >
min. changes from 0 to 1). This pressure
must then subsist for 30 seconds. The
valve leakage test is then deemed to be
completed.If the valve leakage test line is
not empty at the start (e.g. as a result of a
previous fault shut-down), main gas valve
2 opens first. The valve leakage test line is
vented (into the combustion chamber or
over the roof, depending on the system;
for suggested circuit, see Appendix). It is
checked, whether the line remains
pressureless for 30 seconds. Otherwise
the procedure is, as described previously.
GENERAL SAFETY FUNCTIONS
In case a flame does not develop when
starting the burner (fuel release) the
burner will shut off at the end of the safety
period (shut-off on trouble).
A shut-off on trouble will also occur in the
case of flame failure during operation, air
flow failure during the pre-ventilation
phase and pressure failure during the
whole period of burner operation.
Any failure of the flame signal at the end of
the safety period and a flame signal during
the pre-ventilation phase (external light
control) will result in a shut-off on trouble
with the control box being locked.
The trouble is indicated by the trouble
signal lamp lighting up.
The control box can be unlocked
immediately after a shut-off on trouble by
pressing the unlocking key. The program
unit will return to its starting position and
proceed with the restart of the burner.
A voltage failure will result in a regular
shut-off of the burner. Upon voltage
recovery there may be an automatic
restart unless another interlock is
provided, e.g. by the safety system. In any
case of trouble the fuel oil supply will be
shut off right away. The program unit will
stop at the same time causing also the
trouble location indicator to stop.
The symbols will indicate the kind of
trouble.
Summary of Contents for 3145132
Page 26: ...26 www ecoflam burners com EN 420010930200 APPENDIX Electrical diagrams...
Page 27: ...27 www ecoflam burners com EN 420010930200 APPENDIX Electrical diagrams...
Page 28: ...28 www ecoflam burners com EN 420010930200 APPENDIX Electrical diagrams...
Page 29: ...29 www ecoflam burners com EN 420010930200 APPENDIX Electrical diagrams...