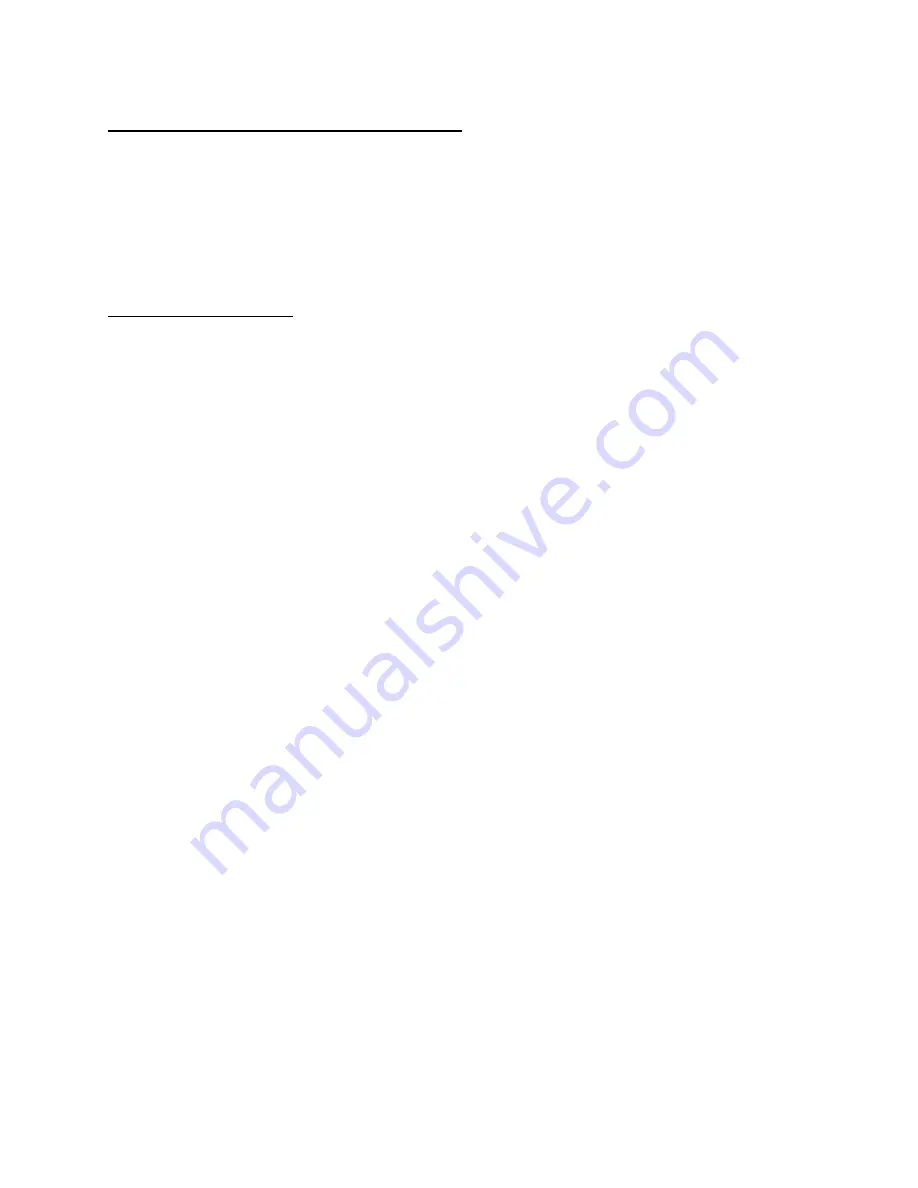
8
3.0 Connecting the NOxCAN module
Power and CAN connections to the module are made using the Eurofast 12mm connector on the
module. The power input requirement is 12 to 30VDC at 1.5A (steady-state). At start-up, there
can be a peak current of up to 5A. Multiple modules can share the CAN bus. All modules are
configured to broadcast CAN messages at the CAN baud rate of 500K. The maximum distance
between any two nodes on the CAN bus at this baud rate is 100m. Each end of the CAN bus
must have a terminating resistor of 121 Ohms.
3.1 Application
Notes
1.
Configuration software (ECM Configuration Tool) for the module is located on the CD. This
software allows the setup, configuration, monitoring, and recording of data using supported
CAN adapters.
2.
The NOxCAN is calibrated for lean (i.e. O
2
> 0%) exhaust conditions. However, it will
output NOx and O
2
values under rich conditions. Under rich conditions, the NOxCAN will
output negative O
2
values which in magnitude are proportional (but not scaled) to the CO and
H2 in the exhaust. It is the responsibility of the user to verify the accuracy of the NOx values
under rich and near zero O
2
(i.e. O
2
< 0.5%) exhaust conditions.
3.
The NOxCAN is calibrated for NOx between 0 and 3000 ppm and O
2
between 0 and 25%.
The user can zero and span the NOx and O
2
measurements. The user zeros and spans can
also be cancelled, returning to the factory calibration. The factory calibration and the user
zeros and spans are stored in a memory chip located in the connector of the NOx sensor. No
matter what the NOx sensor is plugged into, it will read the same NOx and O
2
values since
the factory calibration, user zeros, and user spans travel with the sensor.
4.
The main disturbance affecting the accuracy of the NOx and O
2
measurements is the
temperature of the NOx sensor body. Thus the sensor should be zero’d and span’d under
thermal conditions (i.e. exhaust pipe temperatures) close to what it will experience in service.
During start-up, it is the achieving of constant sensor body temperatures that determines
when the NOx and O
2
values output by the module can be used. Typically, this takes 5
minutes when the sensor is in the exhaust of a running engine. Do not exceed 850°C exhaust
gas temperature.
5.
It is best to zero and span the NOx sensor in the exhaust of an engine and in
comparison to a chemiluminescence NOx analyzer. If you zero and span the NOx
measurement in a vessel fed by gases from tanks, you will need to heat the vessel walls
to the temperature of the exhaust pipe the sensor will be used in, and will need to
include H
2
O in the gases in the concentration(s) the sensor will see in the exhaust of the
engine.
6.
Do not extend the wires between the NOx sensor and the control module. You can lengthen
the power wires on the DC Power Cable (P/N: 11-01 or 11-02) but use large gauge wire and
make sure that the voltage at the power terminals of the supplied harness is at least 14 V
when the sensor is being heated. You can lengthen the CAN communication wires using
Eurofast 12mm cable. Eurofast 12mm cable was designed specifically for CAN
communication and along with additional “Tees”, allows you to easily build long and reliable
CAN networks.