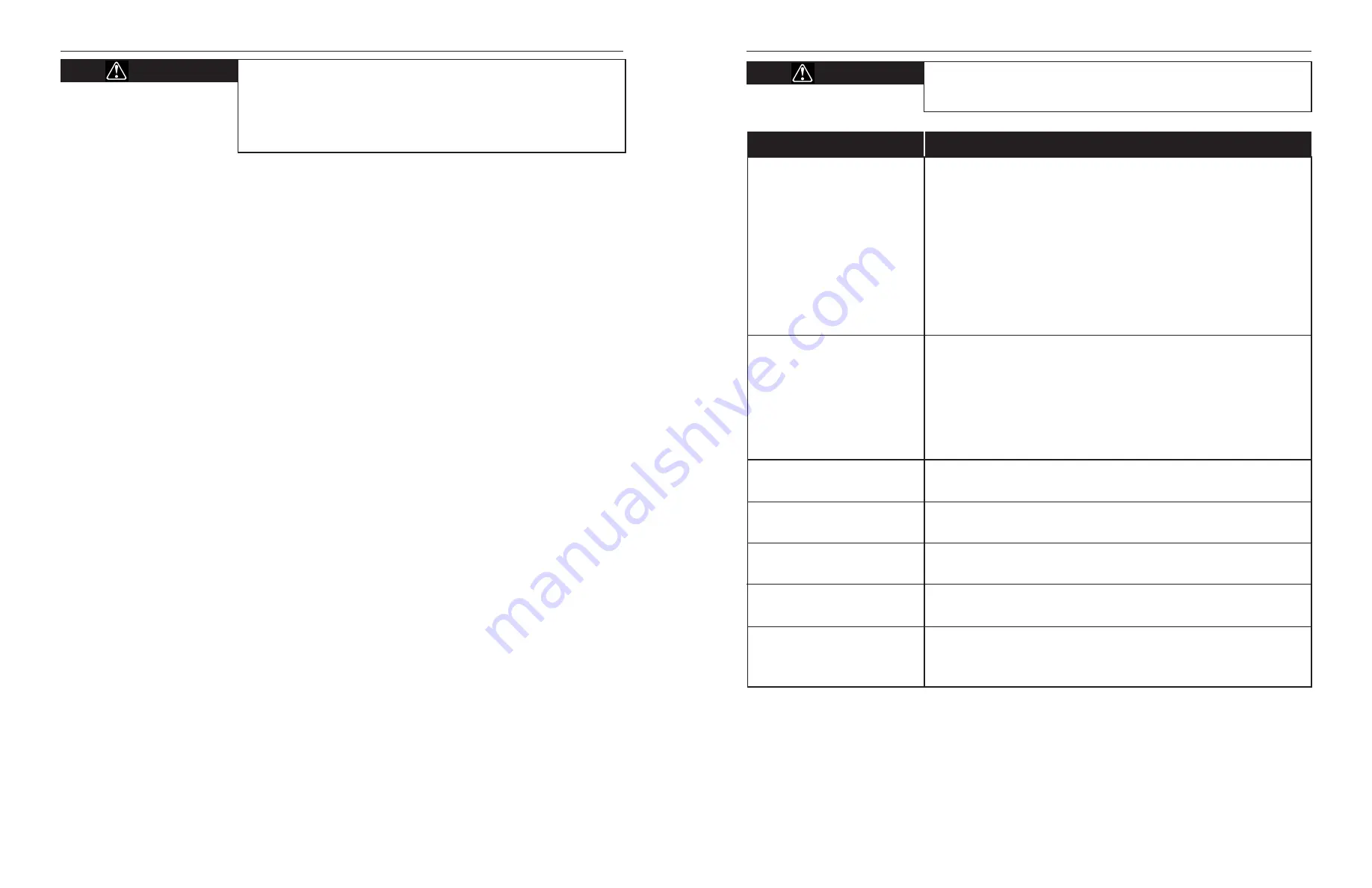
4
2.0 Burner Operation and Controls
Failure to use suitable flame sensing devices and automatic fuel shut-off
valves can cause explosions and fires. The owner/user and/or his insur-
ance underwriter is responsible for providing, using, and maintaining
suitable limit controls, flame supervision, and other safety devices for this
burner, and for properly interfacing all electrical equipment and sequenc-
ing burner operation.
Turndown Method
Ratiomatic burners are designed to operate with either two-position or modulating
temperature control systems. Gas-air ratio control is performed by a ratio regulator
as shown in Figure 2.
Control Motor Requirements
Stroke:
90
°
. For applications with unusually high backpressures or drafts, motor
travel may need to be restricted to less than 90
°
. Eclipse recommends adjustable
stroke motors or motors with travel-limiting auxiliary switches for these jobs.
Timing:
15 seconds minimum.
Mounting:
Can be mounted on either side of the burner. However, if an air inlet filter
is used, the control motor must be mounted on the side opposite the filter.
Piloting
A spark ignited pilot is an integral part of each burner. An adjustment cock is included
for pilot adjustment.
The customer must provide a pilot gas valve train that includes a pilot gas regulator
and a solenoid valve.
If combustion chamber pressure is likely to be more than
±
1"w.c. (2.5 mbars) or if
it is expected to fluctuate during operation, cross-connect the pilot regulator vent to
the chamber.
Flame Monitoring
50 thru 600 sizes:
A flame rod is included with the burner; UV scanners and mount-
ing kits are available as options.
750 thru 2500 sizes:
UV scanner only; must be ordered separately.
Main Gas Valve Train
Gas should be supplied to the burner inlet through a valve train which complies with
NFPA Standards and all applicable local codes.
When multiple burners are fed from the same valve train, a check valve must be in-
stalled in the gas line as close as possible to the proportionator inlet to prevent un-
even flows at low fire. Main regulator pressure may need to be increased to com-
pensate for the check valve pressure drop.
CAUTION: Customer supplied main gas regulators for inlet pressures greater
than 1 psig (70 mbars) for 50-200 Ratiomatics or 5 psig (350 mbars) for 300-
2500 Ratiomatics must be capable of tight shut-off to prevent leakage and sub-
sequent proportionator damage.
Limit Controls
Limit controls and safety equipment should comply with current NFPA Standard 86
and all applicable local codes and/or standards. NFPA Standards are available from:
National Fire Protection Association
Batterymarch Park
Quincy, Massachusetts 02269
Blower Shut-Off
During shutdown, the blower must not be turned off until the chamber temperature
has dropped below 250
°
F (121
°
C). This is to prevent hot gases from flowing back
through the burner and blower and damaging them.
WARNING
13
5.0 Trouble-shooting
Trouble-shooting of panels and electrical circuits should be done by quali-
fied plant electricians, technicians, or engineers experienced in all facets
of this type of combustion equipment.
CAUTION
CAUSE(S)
PROBLEM
Burner behaves erratically, does
not respond to adjustment.
Main flame too long & yellow at
high fire.
Main flame too short at high fire.
Low fire (pilot) flame is long,
soft or yellow.
Low fire flame is weak or
unstable.
Main flame fails to light or goes
out as burner cycles to high fire.
Pilot fails to light.
1. On initial start-up, gas line may be filled with air. Repeat ignition
trial several times to purge.
2. No power to ignition transformer or pilot solenoid.
3. Open circuit between ignition transformer and spark plug.
4. Spark plug needs cleaning.
5. Spark plug center electrode grounded against burner.
6. Spark plug improperly grounded. Do not use pipe dope on ignition plug
threads.
7. Pilot gas cock screw closed.
8. Insufficient gas pressure into or out of pilot regulator.
1. Pilot set too lean, becoming unstable as air increases.
2. Insufficient pressure into or out of main gas regulator.
3. Main gas adjusting valve not open enough.
4. Marginal air pressure switch setting.
5. Suction or backpressure in chamber fluctuates, upsetting pilot stability.
Cross-connect pilot regulator vent to the combustion chamber, but not via
the burner air pressure tap.
1. Gas flow is insufficient. Open pilot gas cock adjusting screw or increase
pressure out of pilot gas regulator.
1. Burner internals loose, dirty or burned out. If any of these problems exist, con-
tact your Eclipse representative or the Eclipse factory for service.
1. Gas flow is too high. Gas butterfly valve is open too far, or main gas regu-
lator spring is screwed in too far.
1. Gas flow is too low. Gas butterfly valve is closed too far, or main gas regu-
lator spring is screwed out too far.
1. Too much gas flow. Main gas proportionator spring is set for too much
flow, or pilot gas cock adjustment is open too far.
2. Insufficient air flow due to dirty blower filter or impeller.