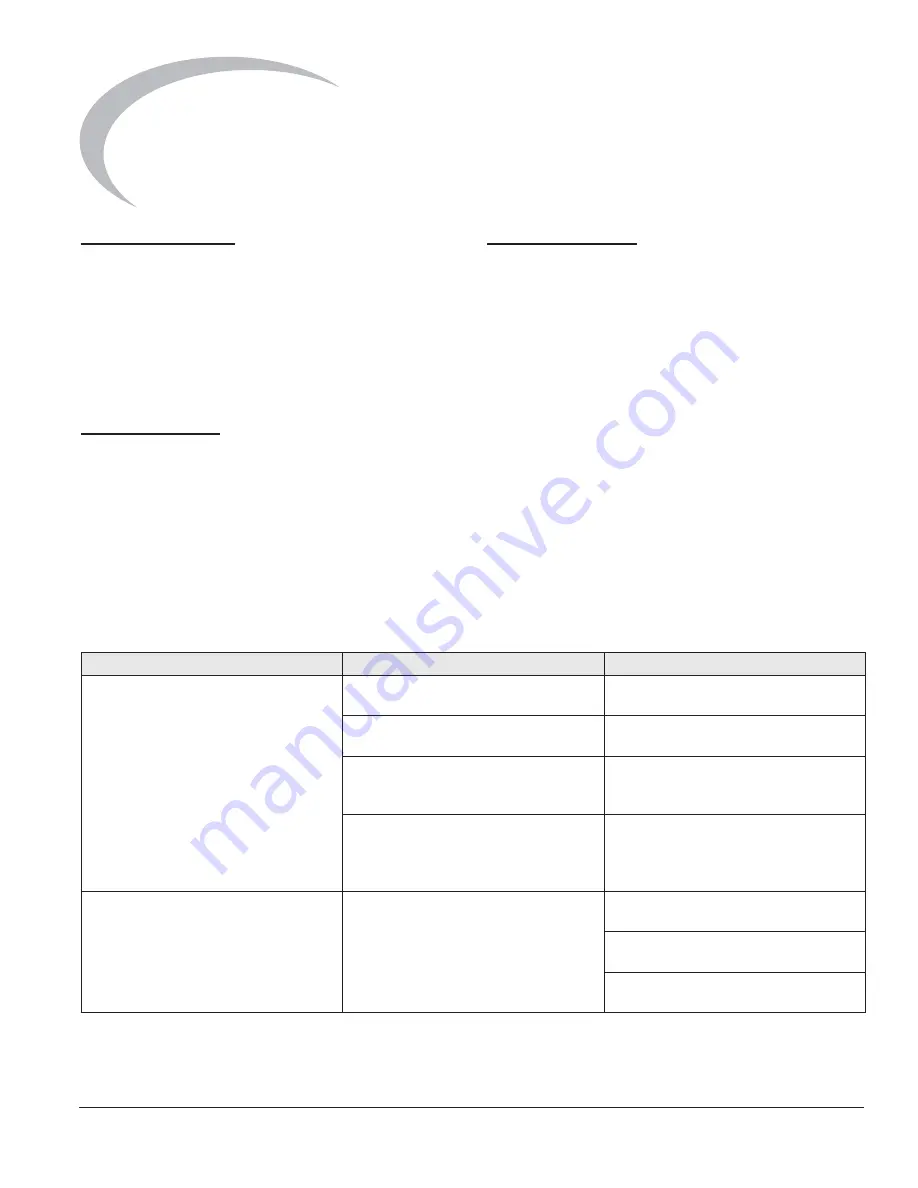
13
Eclipse Packaged Gas BoostPak, V2, Installation Guide 630-2, 6/22/2010
Maintenance &
Troubleshooting
Monthly Checklist
• Inspect and tighten loose mechanical components
• Look for signs of damage and repair
• Test operation if the unit has not run and check for
excessive vibration
• Clean the booster motor housing
• Clean the heat exchanger, its motor, and cooling fan
(MH only)
• Wipe clean the control panel surfaces
Yearly Checklist
• Check inlet and outlet pressure switch settings
• Check and compare inlet and outlet pressures to the
initial commissioning record sheet
• Measure and compare the power supply and motor
current to the record sheet
• Perform operational test in the commissioning
section of this guide
Alarm Conditions
Certain conditions will cause the ALARM to come on. To
silence the alarm, press the ALARM SILENCE push
button.
• INLET LOW GAS MANUAL RESET PRESSURE
SWITCH opens due to low utility line pressure. The
LOW GAS light comes on and the booster motor will
stop running. When the pressure is restored, this
switch must be manually pushed to reset its contact.
• DISCHARGE GAS PRESSURE SWITCH fails to
make contact within 15 seconds. The LOW GAS
light comes on; the booster will not shut down.
• If the motor wiring or internal temperature switch
opens, then the motor will stop causing the
discharge gas pressure switch to open. Then the
ALARM and LOW GAS light come on.
• A booster motor overload condition will shut down
the booster and the MOTOR FAULT light and
ALARM will come on.
• A heat exchanger motor overload condition will shut
down the heat exchanger fan and the MOTOR
FAULT light and ALARM will come on (MH only).
Problem
Possible Cause
Solution
No POWER ON light
Main supply power is off
Be sure main power to the system is
switched “on”.
Main disconnect switch is off
Turn the control panel main disconnect
switch on.
Loose connection
Check for voltage on panel terminals,
turn off main power and inspect,
tighten wire connection.
Blown fuse
Verify that all fuses are good and
properly installed. If blown, have a
qualified electrician determine the
cause and fix before replacing fuse.
Cannot initiate start sequence
Inlet low gas manual reset pressure
switch has activated
Check incoming gas pressure: adjust if
necessary.
Check pressure switch setting and
operation.
If used, check that the pressure switch
isolating valve is not closed.
6