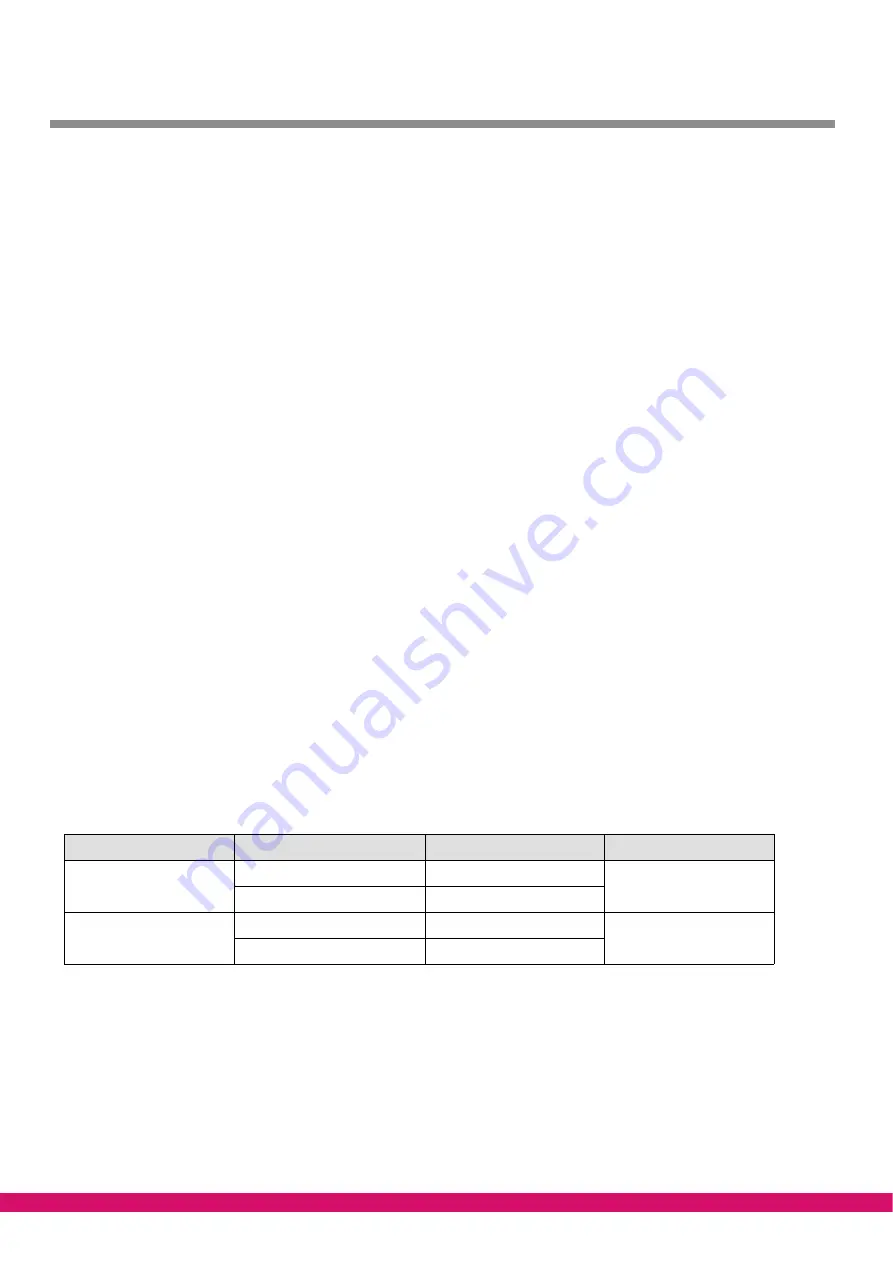
Version 2.02 15.05.2007
Function of VS 3000
22
3.22 Monitoring cylinder head temperature
Compressor cylinder head temperature is monitored to keep it from exceeding a defined maximum so as to pre-
vent damage to the compressor. The maximum cylinder head temperature at which a compressor is disabled
and also the compressor enabling temperature are definable by the parameters
Comp. OFF temp
and
Comp.
ON temp
(Menu 3-4). The respective compressor is stopped after a definable time delay elapses (Menu 3-4
Comp. temp del.
) and disabled for all further control actions when temperature exceeds the set maximum.
The compressor remains disabled until temperature drops below the enabling level. If this action is repeated
several times in a single day (five actuations) and if more than one compressor is still available in the pack, the
compressor will be disabled permanently and must then be re-enabled manually (Menu 3-1-c
Enable
comp.stages
). This causes fault report
Auto disable Cx
to be generated.
Compressor fault with combined control
Compressor fault occurs in the following conditions:
- Actuation of motor overload cutout
- Actuation of low oil pressure cutout
- Cylinder head temperature rise above maximum allowable level
In occurrence of fault conditions on one of the compressors that can be allocated to the frequency changer
(Compressor 1 and 2), the compressor is stopped and fault report is generated as a function of the base load
rotation output state (Digital Output 10 of VS 3000).
Compressor fault with single-stage compressors
With variable-speed compressors the frequency changer is always enabled together with the first compressor
capacity stage. Either Compressor 1 or Compressor 2 can be allocated to the frequency changer by base load
rotation. If base load rotation has not taken place (base load rotation output OFF), a fault on Compressor 1
causes Capacity Stage 1 to be shut down and a corresponding fault report to be generated for Compressor 1.
A fault on Compressor 2 causes Capacity Stage 2 to be shut down and a corresponding fault report to be gener-
ated for Compressor 2.
Following base load rotation (base load rotation output ON)), a fault on Compressor 1 causes Capacity Stage 2
to be shut down and a corresponding fault report to be generated for Compressor 1.
A fault on Compressor 2 causes Capacity Stage 1 to be shut down and a corresponding fault report to be gener-
ated for Compressor 2.
Fault
Base load rotation output
Capacity stage output OFF
Fault report
Compressor 1
ON
Stage 2
Compressor C1
OFF
Stage 1
Compressor 2
ON
Stage 1
Compressor C2
OFF
Stage 2
Compressor fault with capacity-controlled compressors
With multi-stage compressors operated in combined control, the frequency changer is always enabled together
with the first compressor relay stage and the motor of the first compressor is actuated. The following relay
stages are used to actuate the bypass valves of the first compressor.
With combined control the frequency changer can be assigned to either Compressor 1 or Compressor 2 by base
load rotation. This however requires the associate compressor capacity stages to also be rotated as well as the
compressor base load stage when base load rotation takes place.
If the base load is not changed (Base Load Rotation Output OFF), a fault on Compressor 1 will cause shutdown
of Capacity Stage 1 (frequency changer enable and Compressor C1 motor actuation) as well as Capacity Stage