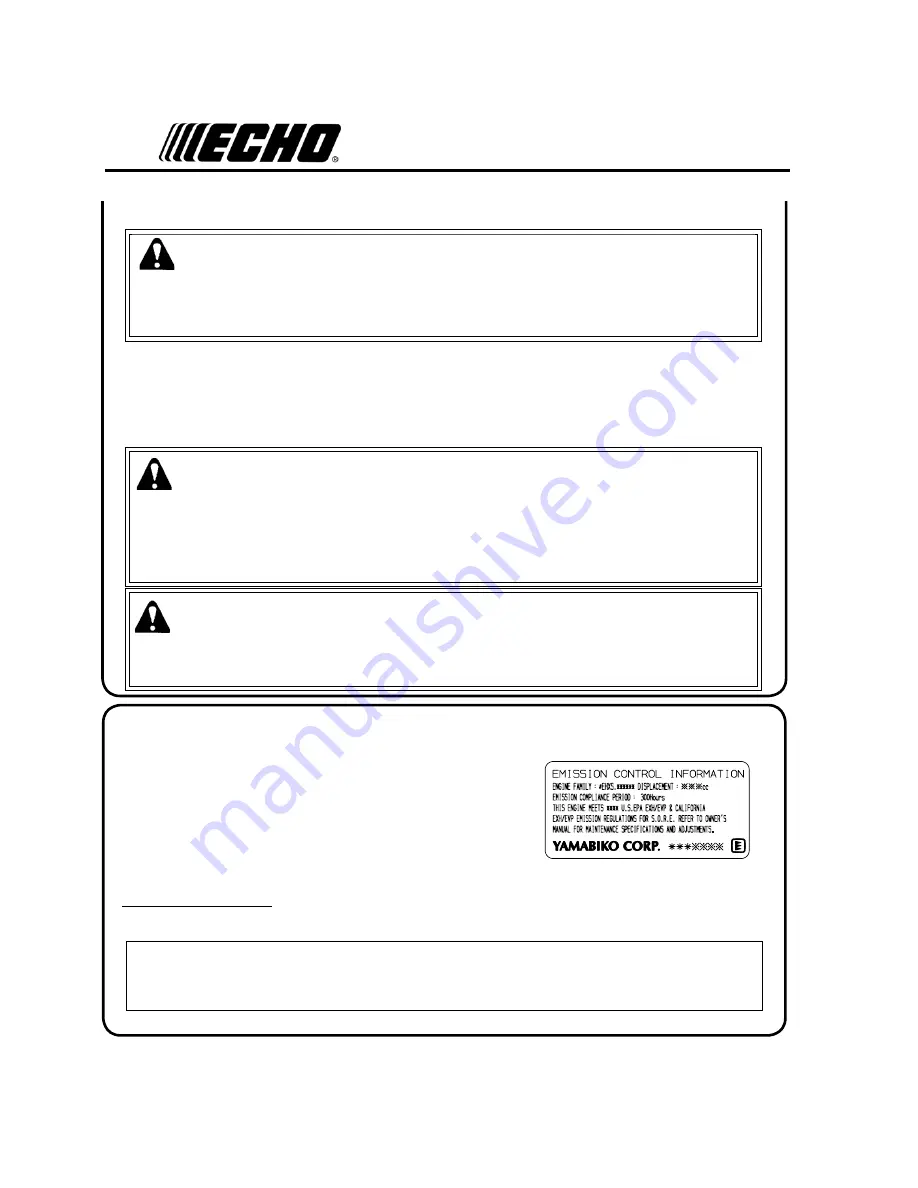
6
EQUIPMENT
WARNING
Use only ECHO approved attachments. Serious injury may result from the use of a non-approved attachment com-
bination. ECHO, INC. will not be responsible for the failure of cutting devices, attachments or accessories which
have not been tested and approved by ECHO. Read and comply with all safety instructions listed in this manual and
safety manual.
• Check unit for loose/missing nuts, bolts, and screws. Tighten and/or replace as needed.
• Inspect shield for damage and ensure that the cut-off knife is securely in place. Replace if either is damaged or miss-
ing.
• Check that the cutting attachment is
fi
rmly attached and in safe operating condition.
• Check that front loop handle and shoulder strap/ or shoulder/waist harness are adjusted for safe, comfortable opera-
tion. See Assembly Section for proper adjustment.
WARNING
Moving parts can amputate
fi
ngers or cause severe injuries. Keep hands, clothing and loose objects away from all
openings.
•
ALWAYS
stop engine, disconnect spark plug, and make sure all moving parts have come to a complete stop
before removing obstructions, clearing debris, or servicing unit.
•
DO NOT
start or operate unit unless all guards and protective covers are properly assembled to unit.
•
NEVER
reach into any opening while the engine is running. Moving parts may not be visible through openings.
WARNING
Check fuel system for leaks due to fuel tank damage, especially if the unit is dropped. If damage or leaks are found,
do not use unit, otherwise serious personal injury or property damage may occur. Have unit repaired by an authorized
servicing dealer before using.
An Emission Control Label
is located on the engine. (Th
is
is an EXAMPLE ONLY, information on label varies by
engine FAMILY).
E
MISSION
C
ONTROL
(
EXHAUST
&
EVAPORATIVE
)
EPA 2010 and Later and/or C.A.R.B. TIER III
PRODUCT EMISSION DURABILITY (EMISSION COMPLIANCE PERIOD)
Th
e 300 hour emission compliance period is the time span selected by the manufacturer certifying the engine emis-
sions output meets applicable emissions regulations, provided that approved maintenance procedures are followed as
listed in the Maintenance Section of this manual.
Th
e emission control system for the engine is EM (engine
modifi cation) and, if the second to last character of the Engine
Family on the Emission Control Information label (sample
below) is “C”, “K”, or “T”, the emission control system is EM
and TWC (3-way catalyst). Th
e fuel tank/fuel line emission
control system is EVAP (evaporative emissions). Evaporative
emissions for California models may only be applicable to fuel
tanks.