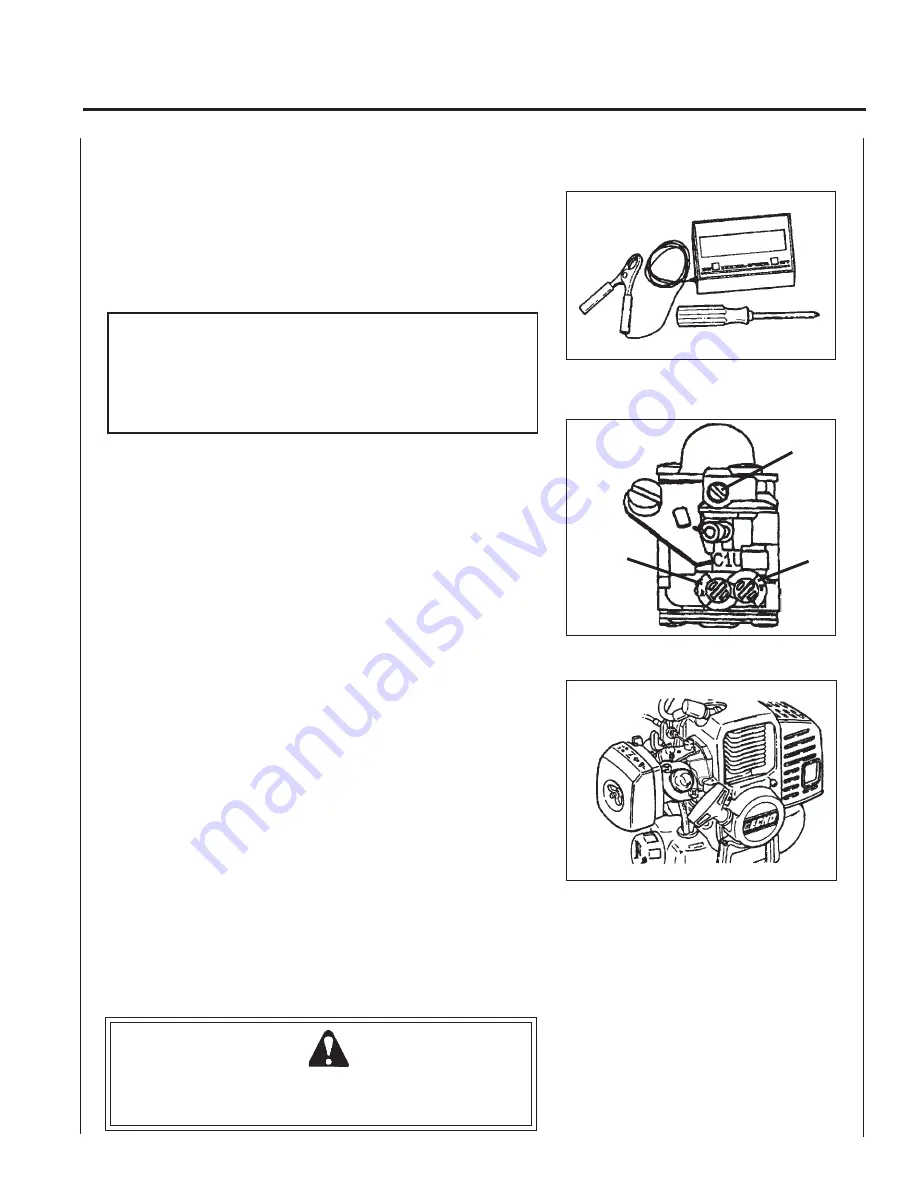
G
RASS
T
RIMMER
/B
RUSH
C
UTTER
O
PERATOR
'
S
M
ANUAL
27
CARBURETOR
ADJUSTMENT
Type 1E Emission Models
Level 2.
Tools required: Slotted Screwdriver w/2 mm blade width, Tachometer
(ECHO P/N 99051130017)
Parts required: None.
NOTE
Every unit is run at the factory and the carburetor is set in
compliance with EPA Phase 1 and California Emission Regula-
tions. In addition, the carburetor is equipped with HI and LO
needle adjustment limiters that prevent settings outside accept-
able limits.
1. Before adjusting the carburetor, clean or replace the air filter and
spark arrester screen.
2. Trimmer line must be extended to the cut-off knife.
3. Start engine and run for several minutes to reach operating
temperature.
4. Stop engine. Turn HI speed needle (A) CCW (counter clockwise)
to stop. Turn LO speed needle (B) midway between full CCW and
CW (clockwise) stops.
5. Idle Speed Adjustment.
Start engine and turn “idle” speed adjustment screw (C) CW until
the cutting attachment begins to turn, then turn the screw CCW
until cutting attachment stops turning. Turn screw CCW an
additional 1/4 turn.
5. Accelerate to full throttle for 2-3 seconds to clear excess fuel from
engine then return to idle. Accelerate to full throttle to check for
smooth transition from idle to full throttle. If engine hesitates, turn
LO needle (B) CCW an additional 1/8 turn and repeat acceleration.
Continue adjusting until smooth acceleration results.
6. Check HI speed RPM at W.O.T. (Wide Open Throttle). HI speed
RPM should be set to specifications found on page 11 "Specifica-
tions" of this manual.
7. Check idle speed and reset if necessary. If a tachometer is avail-
able, idle speed should be set to the specification found on page
11 "Specifications" of this manual.
WARNING
DANGER
When carburetor adjustment is completed, the cutting attachment
should not rotate at idle, otherwise serious personal injury may
result.
A
C
B
Summary of Contents for SMR-2110 - 01-99
Page 2: ......