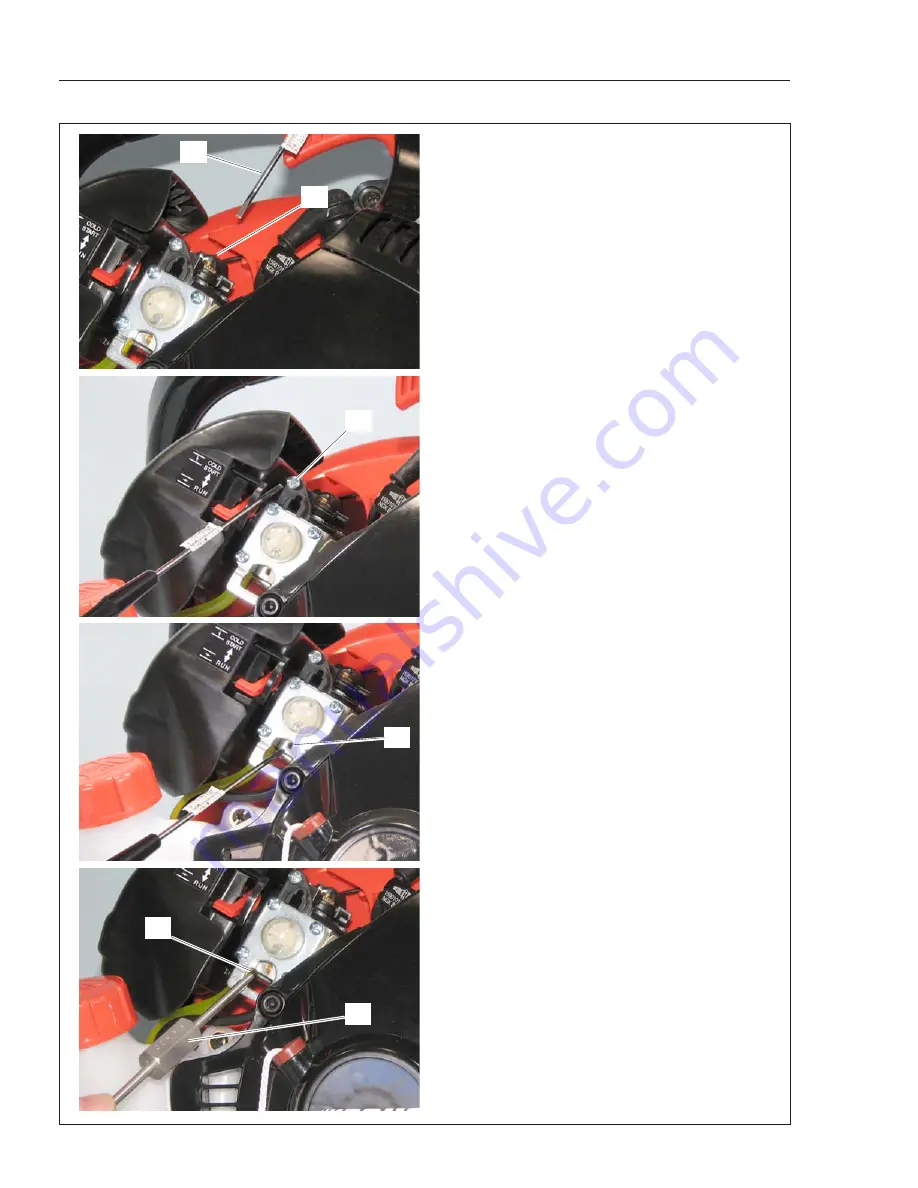
PB-251
FUEL SYSTEM
30
5-5 Adjusting carburetor (Continued)
NOTE :
The initial carburetor settings for idle adjust
screw, idle and H mixture needles are intended to
start and run the engine before final carburetor ad-
justments are made to conform the unit to meet
Emission Regulations. Actual turns required for en-
gine operation may vary.
4. Start engine and warm it up alternating rpm be-
tween WOT and idle every 10 seconds for 1 minute.
5. Adjust idle mixture needle (A) with 2.5 mm blade
screwdriver (E) to reach maximum engine speed
just before drop off.
6. Set idle speed to 3,500 rpm by turning idle adjust
screw (D). Engine rpm should be stable at 3,500
+/- 10 rpm after idle adjust screw adjustment.
7. Turn idle mixture needle (A) counterclockwise to
reduce idle speed 500 to 600 rpm in the range of
2,900 to 3,000 rpm.
NOTE:
Engine speed must be allowed to stabilize a
minimum of 20 seconds after each adjustment of
idle mixture needle to assure accurate tachometer
readings.
8. Adjust H mixture needle (B) and obtain maximum
WOT engine speed just before lean drop off using
2.5mm blade screwdriver.
9. Turn H mixture needle (B) counterclockwise to
reduce WOT engine speed 10-20 rpm. Minimum
WOT engine speed after adjusting should be over
6,700 rpm.
10. Start engine, and verify engine idle speed ranges
from 2,800 to 3,200 rpm, and WOT engine speed
ranges from 6,700 to 7,200 rpm. When final adjust-
ment is completed, the engine should idle,
accelerate smoothly, and attain WOT per above
specification.
11. After adjusting carburetor, insert and secure new
plug(s) (F) P005-001270 deep in the needle holes
per the Emission regulation using limiter plug tool
(C).
(E)
(A)
(D)
(B)
(F)
(C)
Summary of Contents for PB-251
Page 1: ...Ord No 403 16...