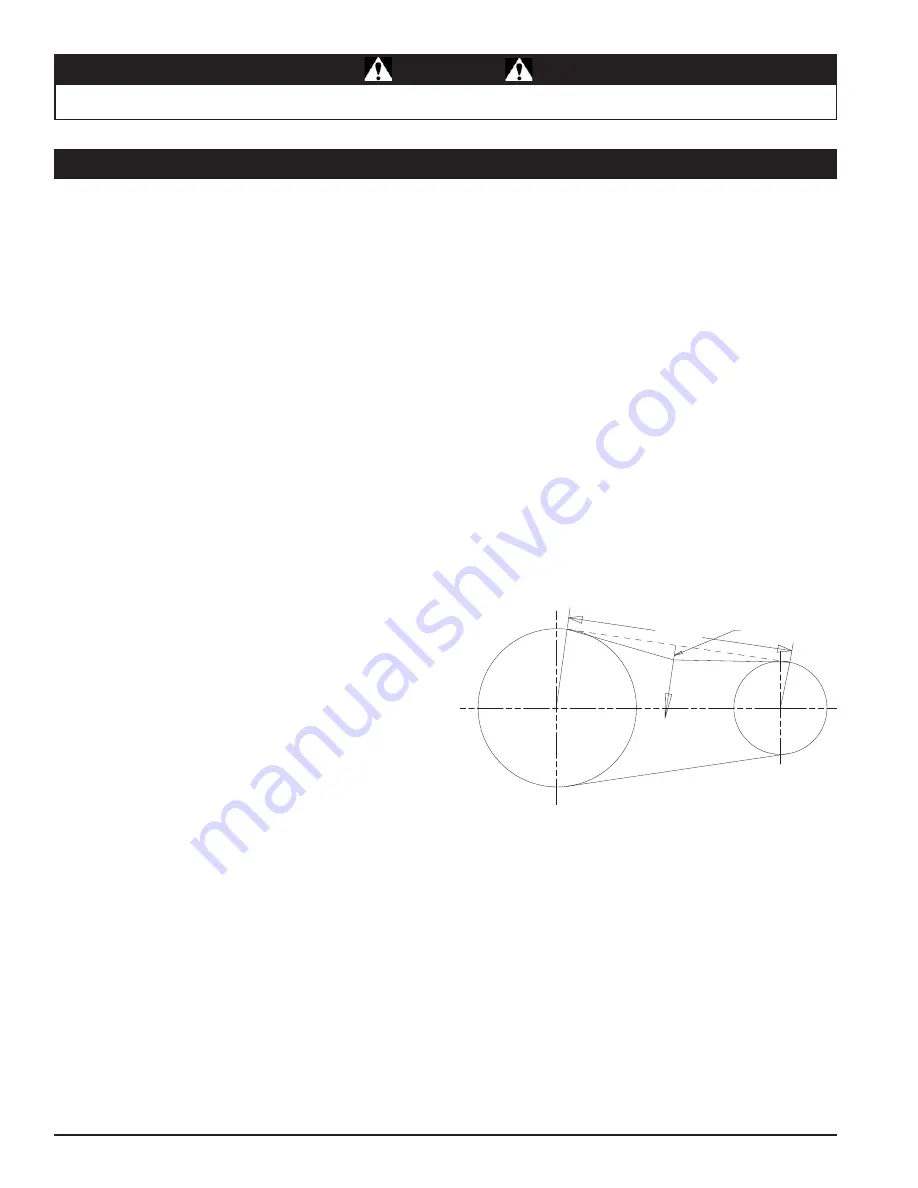
PN 18280-00 R041306
26
SERVICE & MAINTENANCE
BEFORE INSPECTING OR SERvICING ANY PART OF ThIS MAChINE, ShuT OFF POWER SOuRCE,
DISENGAGE ThE hYDRAuLICS, OPEN ShIELD AND MAkE SuRE ALL MOvING PARTS hAvE COME TO A COMPLETE STOP.
WARNINg
5.7.2 REpLAcINg hYDRAuLIc DRIvE bELT
Check the condition of the drive belt annually or after every
25 hours of operation, whichever comes first. If the belt is
cracked, frayed, worn or stretched, replace it. Follow proce-
dure below to replace the drive belt.
using a wrench, pull the small idler pulley away from the
hydraulic belt to release the tension
Remove the hydraulic drive belt from the drive pulley on the
engine and the hydraulic pump
using a wrench, pull the small idler pulley towards the center
of the chipper
Install the hydraulic drive belt on the hydraulic pump, on out-
side of idler pulley and on engine drive pulley.(figure 5.6)
Release idler to apply tension on hydraulic pump drive
belt.
1.
2.
3.
4.
5.
6.
5.7.2 ADjusTINg DRIvE bELTs
Lower the engagement handle
Loosen bolt on engine tie. DO NOT REMOvE.
verify the belt tensioning bolts on the engine mount plate are
tight against the engine mount.
Loosen the four engine mount bolts.
Alternately turn each of the belt tension bolts clockwise an
equal number of turns until the belt deflection at the center
of the belt is 7/16” when a 20 lb load is placed against the
belt (figure 5.5)
Check pulley alignment using a straight edge and adjust the
appropriate belt tension bolt if required.
Tighten the four engine mount bolts to the appropriate
torque
Tighten the engine tie bolt
Lift the engagement handle, start engine and lower engage-
ment handle to test units. Adjust pulleys and belt tension as
needed.
1.
2.
3.
4.
5.
6.
7.
8.
9.
Figure 5.5 - Drive Belt Tension
Span Length
Force
20 lbs
7/16" Deflection
5.7 DRIvE bELTs (coN'T)