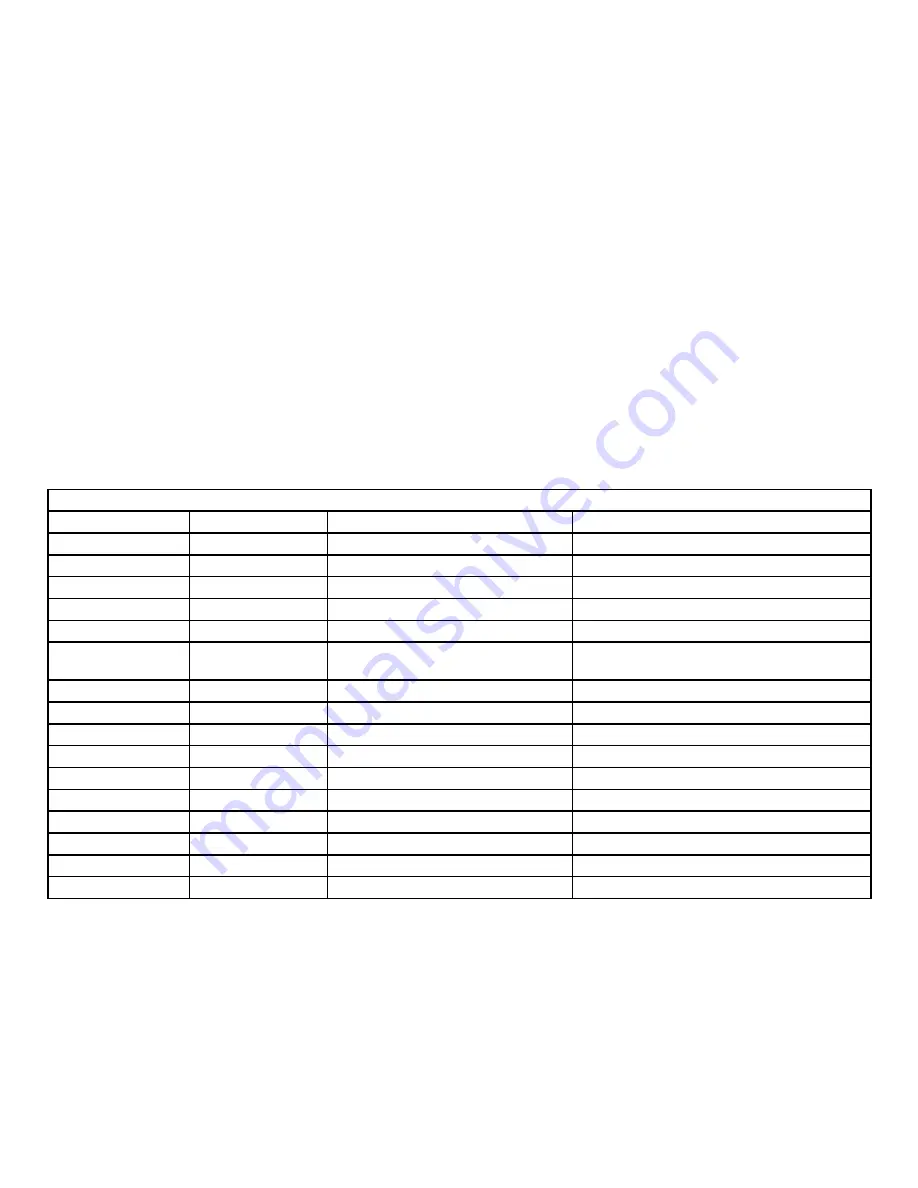
Page 8 of 18
Master/Slave Corner Module Operation
The 360 degree corner modules consist of “master” and “slave” LED light engines and a single integrated heatsink bracket. The “master”
circuit board, in the rear position, must be powered for the “slave”, in the front position, to flash. Corner module pairs are connected by a
sync wire. The flash pattern is set and determined by the master LED module in a module pair.
Dimming Operation
27 Series LED modules may be equipped with a low power “Dimming” mode. When DIM is engaged the LED’s will operate in a reduced
power mode which reduces the light output. Use caution when using the DIM setting to ensure that motorists can clearly see the emergency
vehicle. Failure to use adequate lighting for the circumstances can cause motorists to fail to see the emergency vehicle and lead to serious
personal injury or death. Use of the DIM setting may cause emergency lights to not comply with applicable emergency warning light stan-
dards. Please contact ECCO directly for further information.
CC Series Wiring
A CC series lightbar has a 2-wire power cable and a 16-wire control cable. The entire power load of the bar goes through the power cable.
The black ground wire should be connected directly to the battery. The 10 AWG red power wire requires a constant 10 to 16V power source
with a customer supplied in line fuse. To select an appropriately rated ATO (regular) or Maxi Fuse, add the amp ratings, found in the speci-
fications section, of the modules in your configuration specific lightbar and based on that sum, insert a fuse of the next larger size (to be no
larger than a 30 A fuse). The 16 control cable wires carry only low power (30 mA average) input signals to control the light bar functions and
must be routed to the output of a control switch (or directly to multiple switches).
Before attempting to connect the lightbar wiring harness, refer to the configuration specific wiring key included with the lightbar for the con-
figuration specific functions of each wire. Use appropriate high-temperature wiring if it passes through the engine compartment. Use cable
ties and grommets to secure and protect all cables and wires.
TABLE 2
Standard CC Function Wire Definitions
Function Wire Color
Function
Description
Notes
GRN/BLK
L1
Level 1 Emergency Mode
WHT/BLK
L2
Level 2 Emergency Mode
RED/BLK
L3
Level 3 Emergency Mode
RED
Arrowstik Left
Left Arrowstick
Overrides L1, L2, & L3 for rear of lightbar
ORG
Arrowstick Right
Right Arrowstick
Overrides L1, L2, & L3 for rear of lightbar
WHT
Drivers Side Cut
Cut Driver Side Directional and Alley
Lights
Designed to interface with the driver’s door
switch
BLK/RED
Pattern Select
Pattern Select
BLK
Take Down Flash
Take Down/Work Light Wig/Wag Flash
ORG/BLK
Take Down Lights
Take Down/Work Light Steady Burn
Overrides Take Down Flash
BLU/WHT
Alley Light Flash
Enables Alley Light Wig/Wag Flash
BLK/WHT
Left Alley Light
Left Alley Steady Burn
Overrides Alley Light Flash
RED/WHT
Right Alley Light
Right Alley Steady Burn
Overrides Alley Light Flash
GRN/WHT
Front Cut-Off
Blacks-Out Front Facing LEDs
BLU/BLK
Rear Cut-Off
Blacks-Out Rear Facing LEDs
GRN
Cruise Lights
End LEDs only
Overridden by all other functions except for Dim
BLU
Lightbar DIM
Sets LEDs to DIM mode
Note:
-When the Arrowstik Left and Arrowstik Right wires are both connected to +power, the Center-Out Arrowstik function is activated.
-The Front Cut and Rear Cut functions must be used with the greatest care to ensure that the use of these functions do not diminish
the effectiveness of the Emergency Warning signal.
-When the Pattern Select wire is connected to +power alone, test mode is enabled to exercise all outputs in sequence.
-The Dim Function lowers the brightness of the LEDs in both the ArrowStik mode and Emergency Warning Flash modes.
-The WHT Drivers Side Cut wire may be changed to Arrowstik Flash. Please see the Arrowstik flash pattern selection section below
for details.
-Lightbars equipped with a DOT strip assembly are wired in conjunction with the STT tail light function. All STT functions are
powered independent of the central driver PCA.