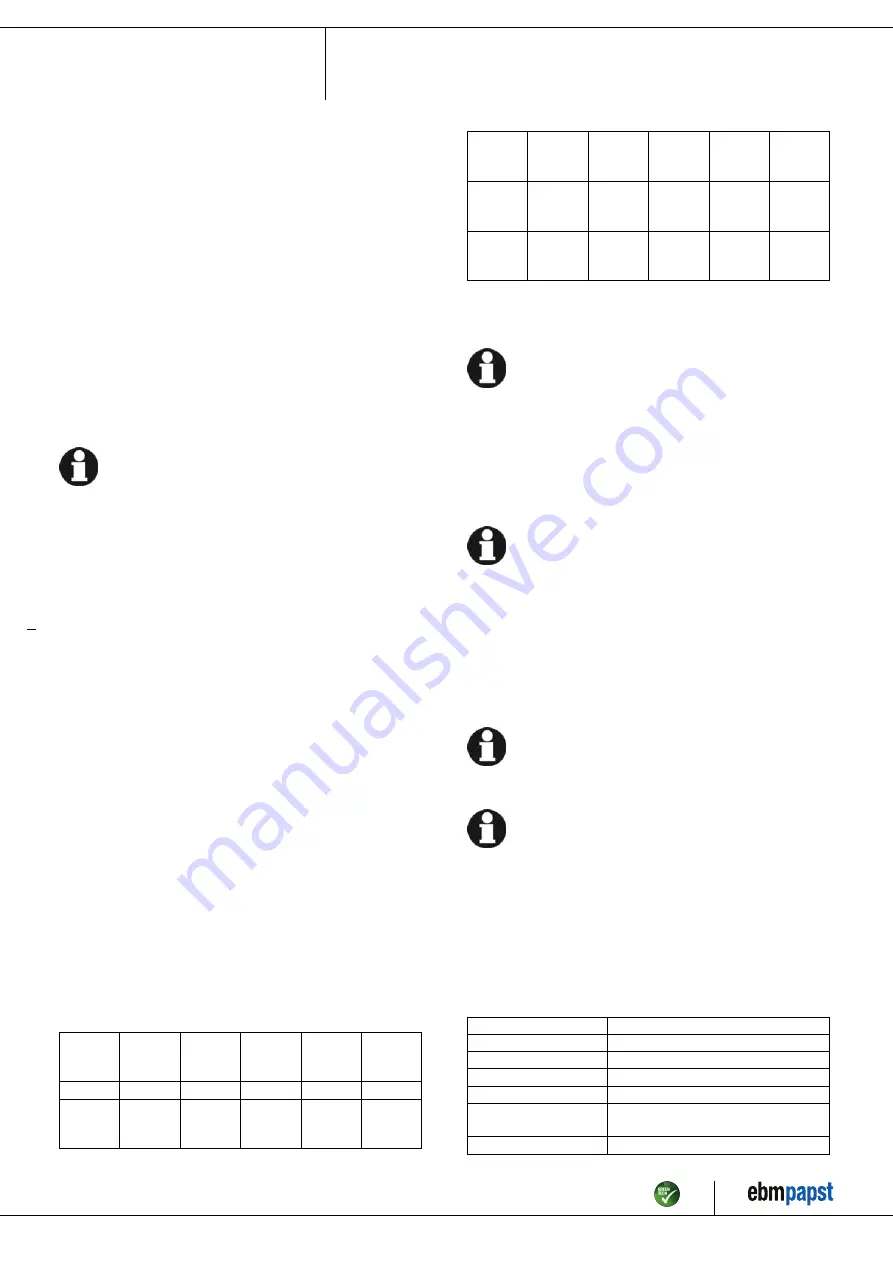
Operating instructions
K3G280-PS10-J2
Translation of the original operating instructions
→ Only connect the fan to circuits that can be switched off with
an all-pole disconnection switch.
→ When working on the fan, secure the system/machine in
which the fan is installed so as to prevent it from being
switched back on.
NOTE
Device malfunctions possible
Route the device's control lines separately from the supply line.
→ Maintain the greatest possible clearance.
Recommendation: clearance > 10 cm (separate cable
routing)
NOTE
Water ingress into wires or cables
Water ingress at the customer end of the cable can damage the
device.
→ Make sure the end of the cable is connected in a dry
environment.
Only connect the device to circuits that can be switched off with
an all-pole disconnection switch.
4.2.1 Requirements
;
Check whether the data on the nameplate match the connection data.
;
Before connecting the device, make sure the power supply matches
the device voltage.
;
Only use cables designed for the current level indicated on the
nameplate.
For determining the cross-section, note the sizing criteria according
to EN 61800-5-1. The protective earth must have a cross-section
equal to or greater than that of the phase conductor.
We recommend the use of 105 °C cables. Ensure that the minimum
cable cross-section is at least
AWG 26 / 0.13 mm².
;
Note the following when routing the cables:
For permanently installed lines, the bending radius must be at least
four times the outside diameter of the cable.
For movable lines, the bending radius must be at least 15 times the
outside diameter of the cable.
Ground conductor contact resistance according to EN 61800-5-1
Compliance with the impedance specifications according to EN 61800-5-
1 for the protective earth connection circuit must be verified in the end
application.
Depending on the circumstances of installation, it may be necessary to
connect an additional protective earth conductor to the extra protective
earth terminal on the device.
The protective earth terminal is on the housing and has a ground
conductor symbol and a bore hole.
4.2.2 Supply connection and fuses
Assignment of supply cable cross-sections and their required fuses (line
protection only, no equipment protection).
Nominal
voltage
Fuse
Automatic
circuit
breaker
Cable
cross-
section
Cable
cross-
section
VDE
UL
VDE
mm²
*AWG
3/PE AC
380-480
VAC
16 A
15 A
C16A
1.5
16
3/PE AC
380-480
VAC
20 A
20 A
C20A
2.5
14
3/PE AC
380-480
VAC
25 A
25 A
C25A
4.0
12
3/PE AC
380-480
VAC
32 A
30 A
C32A
6.0
10
* AWG = American Wire Gauge
4.2.3 Reactive currents
Because of the EMC filter integrated for compliance with EMC
limits (interference emission and immunity to interference),
reactive currents can be measured in the supply line even
when the motor is at a standstill and the line voltage is switched
on.
●
The values are typically less than 250 mA.
●
At the same time, the effective power in this operating state
(operational readiness) is typically < 5 W.
4.2.4 Residual current circuit breaker (RCCB)
Only universal residual current devices (type B or B+) are
allowed. As with variable frequency drives, residual current
devices cannot provide personal safety while operating the
device.
When the device's power supply is switched on, pulsed
charging currents from the capacitors in the integrated EMC
filter can lead to the residual current devices tripping without
delay. We recommend the use of residual current circuit
breakers with a trip threshold of 300 mA and delayed tripping
(super-resistant, characteristic K).
4.2.5 Leakage current
For asymmetrical power systems or if a phase fails, the
leakage current can increase to a multiple of the nominal value.
4.2.6 Locked-rotor protection
Due to the locked-rotor protection, the starting current (LRA) is
equal to or less than the nominal current (FLA).
4.3 Connecting the cables
The device has external leads.
;
First connect the "PE" (protective earth).
●
Connect the cables according to your application. When doing so,
observe Chapter 4.5 Connection diagram.
4.4 Factory settings
Factory settings made for the device by ebm-papst.
Mode parameter set 1
PWM control
Mode parameter set 2
PWM control
Fan/device address
01
Max. PWM / %
100
Min. PWM / %
5
Save set value to
EEPROM
Yes
Set value requirement
Analog (linear)
Item no. 54427-5-9970 · ENU · Change 90170 · Approved 2016-07-14 · Page 7 / 12
ebm-papst Mulfingen GmbH & Co. KG · Bachmühle 2 · D-74673 Mulfingen · Phone +49 (0) 7938 81-0 · Fax +49 (0) 7938 81-110 · [email protected] · www.ebmpapst.com