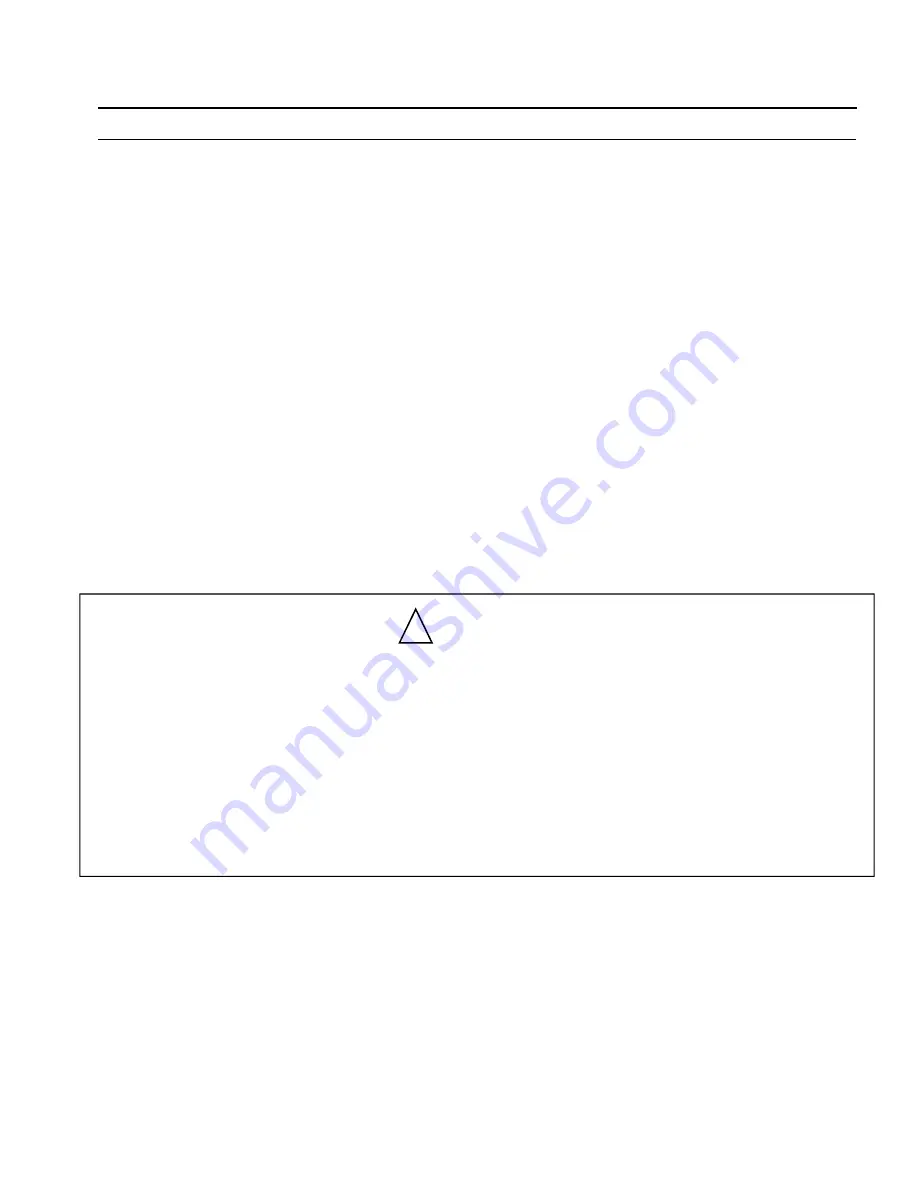
11
Rev
10/2018
Operating, Installation, and Maintenance
Rules for Safe Installation (Continued)
PIPING -
Pipes must line up and not be forced into position. Piping should be independently supported
near the pump so that no strain will be placed on the pump casing. Where any noise is objectionable,
pump should be insulated from the piping with vibration isolation devices. Always keep pipe size as large
as possible and use a minimum of fittings to reduce friction losses.
SUCTION PIPING –
Suction pipe should be direct and as short as possible. It should be at least one size
larger than suction flange size and should have a minimum of elbows and fittings (5 to 6 pipe diameters
of straight pipe before inlet is recommended). The piping should be laid out so that it slopes upward to
pump without dips or high points so that air pockets are eliminated. The highest point in the suction
piping should be the pump inlet except where liquid flows to the pump inlet under pressure. The suction
pipe must be tight and free of air leaks or pump will not operate properly. To avoid vortex, make sure the
end of the suction pipe is submerged twice as much as the size of the pipe diameter.
DISCHARGE PIPING –
Discharge piping should never be smaller than pump flange size and should
preferably be one size larger. A gate valve should always be installed in discharge line for throttling if
capacity is incorrect. To protect the pump from water hammer and to prevent backflow, a check valve
should be installed in the discharge line between the pump and gate valve. On points where it is
necessary to bleed air, vent valves should be installed.
ELECTRICAL CONNECTIONS –
Be sure motor wiring is connected for voltage being used. Follow the
correct wiring procedure on the motor for the voltage you are using. Unit should be connected to a
separate circuit. A fused disconnect switch or circuit breaker must be used in this circuit. Wire of
sufficient size should be used to keep voltage drop to a maximum of 5%. Single phase motors have built-
in overload protection. Three phase motors require a control box. Install overload protection to help
prevent motor damage. Flexible metallic conduit should be used to protect the motor leads. Disconnect
the coupling sleeves and momentarily turn on the motor to check if the rotation direction is the same as
indicated at the pump. If the rotation is incorrect, change two power leads
.
WARNING
Pre-operation Cautions
Make certain the motor is not connected to a power source until the motor is properly assembled
and mounted. Serious personal injury or damage to the motor/pump assembly could occur if the
motor is activated improperly.
Only certified electricians should make electrical connections
.
1.
Prime the pump by adding fluid to the volute case through the top plug. To properly prime
the pump, venting may be required.
2.
Check the nameplate on the motor to determine the correct wiring procedure for your
intended power source and if the motor is single or three phase. Connect the motor to a
power source by following the wiring procedure on the motor's nameplate.
!