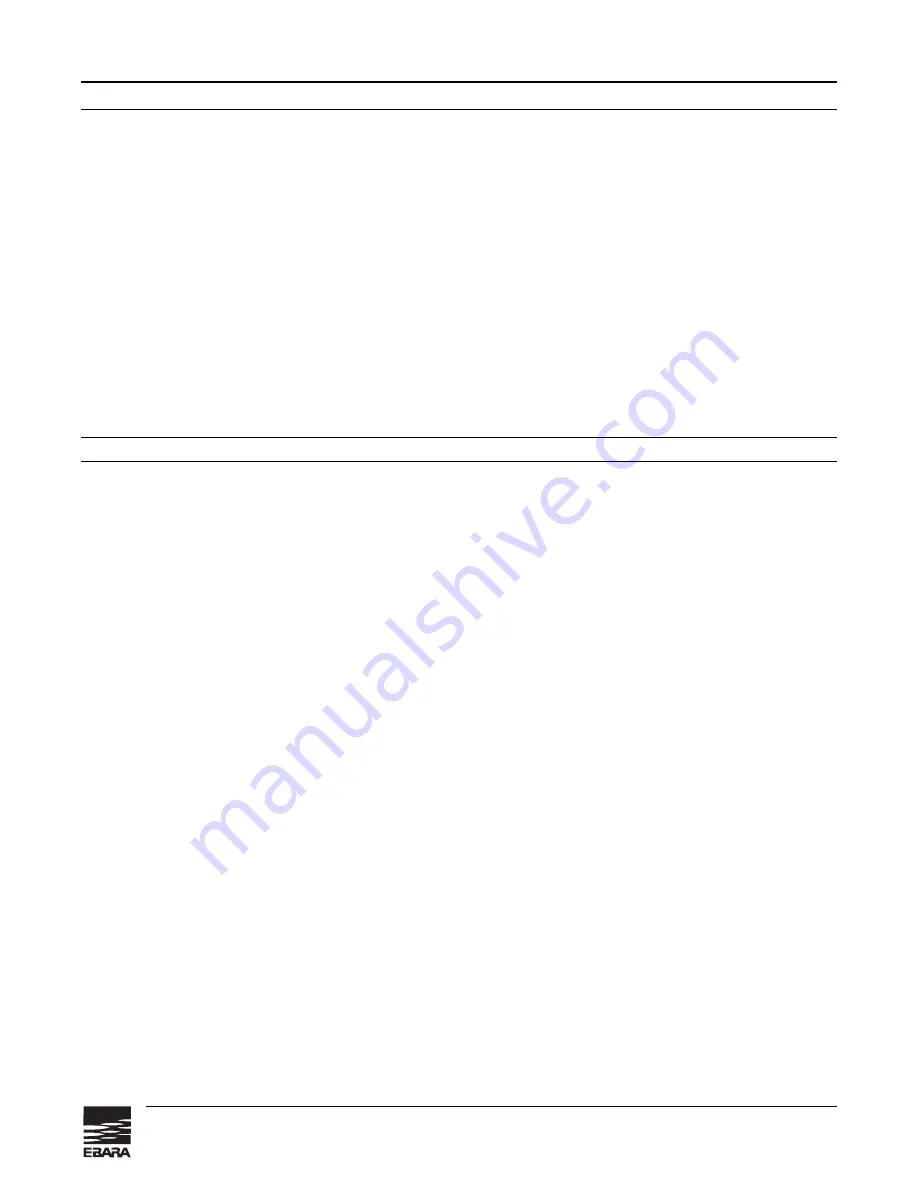
Safety Information and Introduction
DMLU
Instruction, Operation, and Maintenance
Project:
Model:
Chk’d:
Date:
Contents
Section
Page
Safety Information . . . . . . . . . . . . . . . . . . . . . . . . . . . . . . . . . . . . . . . . . . . . . . . . . 2
Delivery Checks . . . . . . . . . . . . . . . . . . . . . . . . . . . . . . . . . . . . . . . . . . . . . . . . . . 3
Specifications . . . . . . . . . . . . . . . . . . . . . . . . . . . . . . . . . . . . . . . . . . . . . . . . . . . . 3
Installation . . . . . . . . . . . . . . . . . . . . . . . . . . . . . . . . . . . . . . . . . . . . . . . . . . . . . . . 4
Operation . . . . . . . . . . . . . . . . . . . . . . . . . . . . . . . . . . . . . . . . . . . . . . . . . . . . . . . 5
Maintenance . . . . . . . . . . . . . . . . . . . . . . . . . . . . . . . . . . . . . . . . . . . . . . . . . . . . . 6
Troubleshooting . . . . . . . . . . . . . . . . . . . . . . . . . . . . . . . . . . . . . . . . . . . . . . . . . . . 7
Disassembly and Reassembly. . . . . . . . . . . . . . . . . . . . . . . . . . . . . . . . . . . . . . . . . 8
Parts . . . . . . . . . . . . . . . . . . . . . . . . . . . . . . . . . . . . . . . . . . . . . . . . . . . . . . . . . . . 9
Warranty . . . . . . . . . . . . . . . . . . . . . . . . . . . . . . . . . . . . . . . . . . . . . . . . . . . . . . . 12
Warnings in this manual provide information for safe use of your EBARA pump, and instructions for preventing injury to those
operating it. Please pay close attention to the instructions listed below. If there are any questions regarding these instructions,
please direct them to EBARA INTERNATIONAL CORPORATION.
1.
Before lifting the pump, confirm the total weight of the unit listed in the catalog or outline drawing. Use the appropriate
hoist or crane assembly, and make sure that the load is balanced to prevent shifting during loading and off-loading.
2.
Be sure to keep the pump from lying on the power and control cables, and do not use the power and control cables
to lift the pump. This can result in damage to the cables and can cause electrical shorts that can possibly lead to
fires.
3.
A qualified electrician should perform all wiring and all national and local electrical codes must be observed.
4.
Make sure that all equipment is properly grounded. Failure to do so can result in electric shock.
5.
Disassembly and repair of the pump should only be performed by factory trained service centers. Errors made by
unqualified personnel can result in improper assembly and operation, therefore resulting in possible injury.
6.
Always make sure that power switch is in OFF position and that power cable is disconnected before inspecting or
repairing the pump.
7.
If pump is to be out of service for a long period of time, turn power off. If power is left on without operating pump it
can cause insulation breakdown, resulting in a possible motor short or electric shock.
8.
Do not insert hands into the pump during operation.
9.
Do not operate the pump unsubmerged, as overheating can occur, causing insulation breakdown and possible
electric shock.
10. If the insulation resistance is below 1M
Ω
, turn power off to unit as soon as possible, as electric shock can occur.
CALL 1-800-577-8111 FOR SALES AND SUPPORT
CALL 1-800-577-8111 FOR SALES AND SUPPORT