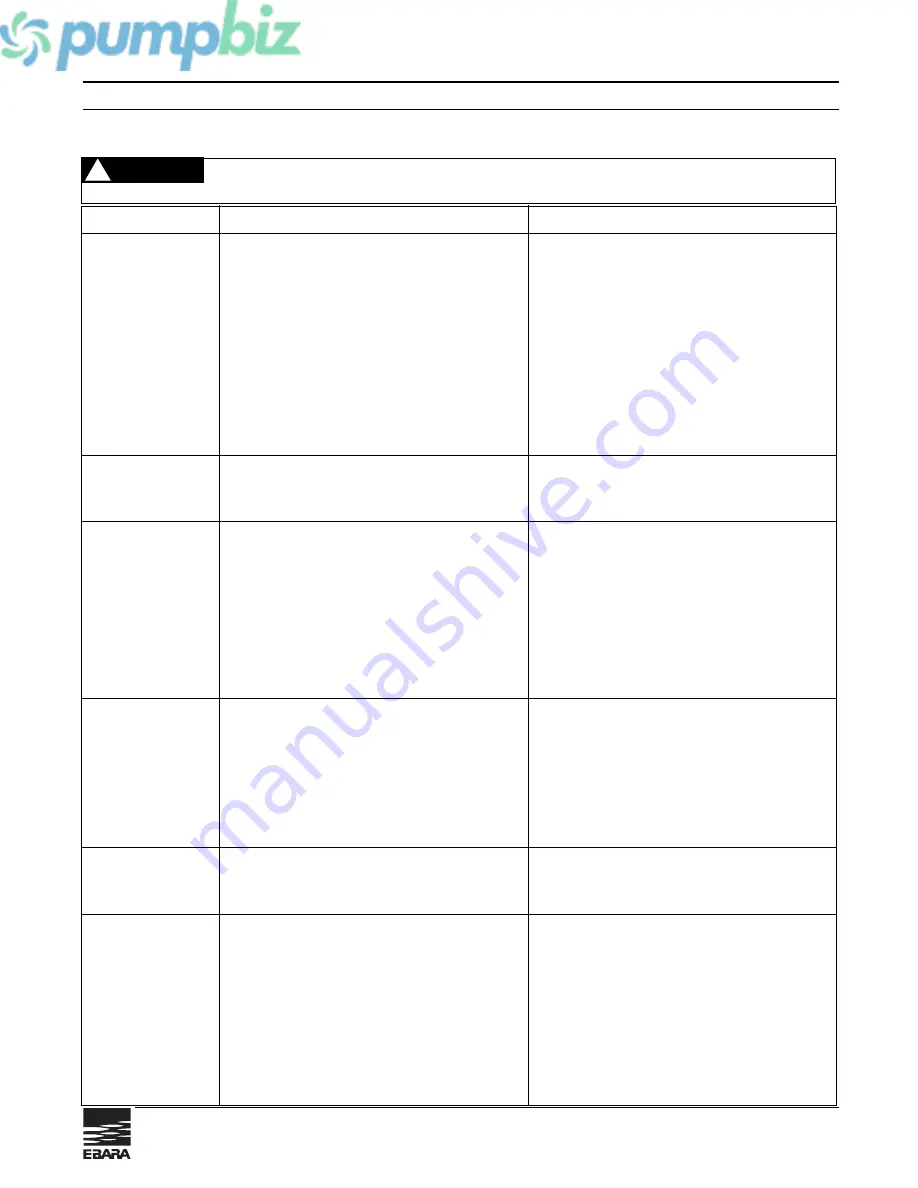
EBARA Submersible Grinder Pumps
DGUII/DGFU
Operating, Installation, and Maintenance
EBARA
Fluid Handling
www.pumpsebara.com
10
(t) 803 327-5005 • (f) 803 327-5097
rev. 11/05
Maintenance and Service
4. Troubleshooting:
All service should be done by factory trained or qualified personnel only.
Trouble
Does not start.
Starts, but immediately
stops.
Operates, but stops after
a while.
Does not pump.
Inadequate volume.
Over current
Pump vibrates;
excessive operating
noise.
Single phase motor:
Motor hums, but will not
run, over load trips.
In approximately 15-20
seconds. After an off
time of 30-60 seconds,
overload protector will
reclose. If motor again
hums and overload trips,
the fault is probably due
to either a defective start
capacitor or relay, or
perhaps the motor itself.
Cause
(1) Power Failure
(2) Large discrepancy between power source and voltage
(3) Significant drop in voltage
(4) Motor phase malfunction
(5) Electric circuit connection faulty
(6) Faulty connection of control circuit
(7) Blown fuse
(8) Faulty magnetic switch
(9) Water is not at level indicated by float
(10) Float is not at appropriate level
(11) Float defective
(12) Short circuit breaker is functioning
(13) Foreign matter clogging pump
(14) Motor burned out
(15) Motor bearing broken
(1) Prolonged dry operation has activated motor protector
and caused pump to stop
(2) High liquid temperature has activated motor protector
and caused pump to stop
(1) Reverse rotation
(2) Significant drop in voltage
(3) Operating a 60Hz pump on 50Hz
(4) Discharge head is high
(5) Large piping loss
(6) Low operating water level causes air suction
(7) Leaking from discharge piping
(8) Clogging of discharge piping
(9) Foreign Matter in suction inlet
(10) Foreign matter clogging pump
(11) Worn impeller
(1) Unbalanced current and voltage
(2) Significant voltage drop
(3) Motor phase malfunction
(4) Operating 50Hz pump on 60Hz
(5) Reverse rotation
(6) Low head; excessive volume of water
(7) Foreign matter clogging pump
(8) Motor bearing is worn or damaged
(1) Reverse rotation
(2) Pump clogged with foreign matter
(3) Piping resonates
(4) Gate valve is closed too far
(1) Defective start capacitor
(2) Defective relay:
a) Check relay coil with continuity meter
b) Check for loose or broken connection in relay and
start capacitor circuit
(2)
c) If after step (2b) motor fails to start, check with
continuity indicator across terminal
(3) Defective motor; if motor fails to start after replacing
relay (start or run capacitor if used), motor may be
defective
Remedy
(1) - (3) Contact electric power company and devise count-
er-measures
(4) Inspect connections and magnetic switch
(5) Inspect electric circuit
(6) Correct wiring
(7) Replace with correct type of fuse
(8) Replace with correct type of magnetic switch
(9) Raise water level
(10) Move float to an appropriate starting level
(11) Repair or replace
(12) Repair location of short circuit
(13) Remove foreign matter
(14) Repair or replace
(15) Repair or replace
(1) Raise stop water level
(2) Lower liquid temperature
(1) Correct rotation (see Operation 2, (3))
(2) Contact electric power company and devise
counter-measures
(3) Check nameplate
(4) Recalculate and adjust
(5) Recalculate and adjust
(6) Raise water level or lower pump
(7) Inspect, repair
(8) Remove foreign matter
(9) Remove foreign matter
(10) Disassemble and remove foreign matter
(11) Replace impeller
(1) Contact electric power company and devise counter-
measure
(2) Contact electric power company and devise counter-
measure
(3) Inspect connections and magnetic switch
(4) Check nameplate
(5) Correct rotation (see Operation 2.)
(6) Replace pump with low head pump
(7) Disassemble and remove foreign matter
(8) Replace bearing
(1) Correct rotation
(2) Disassemble and remove foreign matter
(3) Improve piping
(4) Open gate valve
(1) Replace start capacitor
(2a) Replace relay if open coil is found
(2b) If circuit is intact, replace start capacitor and restart
motor
(2c) If no continuity is indicated, replace relay
(3) Check motor for electrical and mechanical defects
CAUTION
!