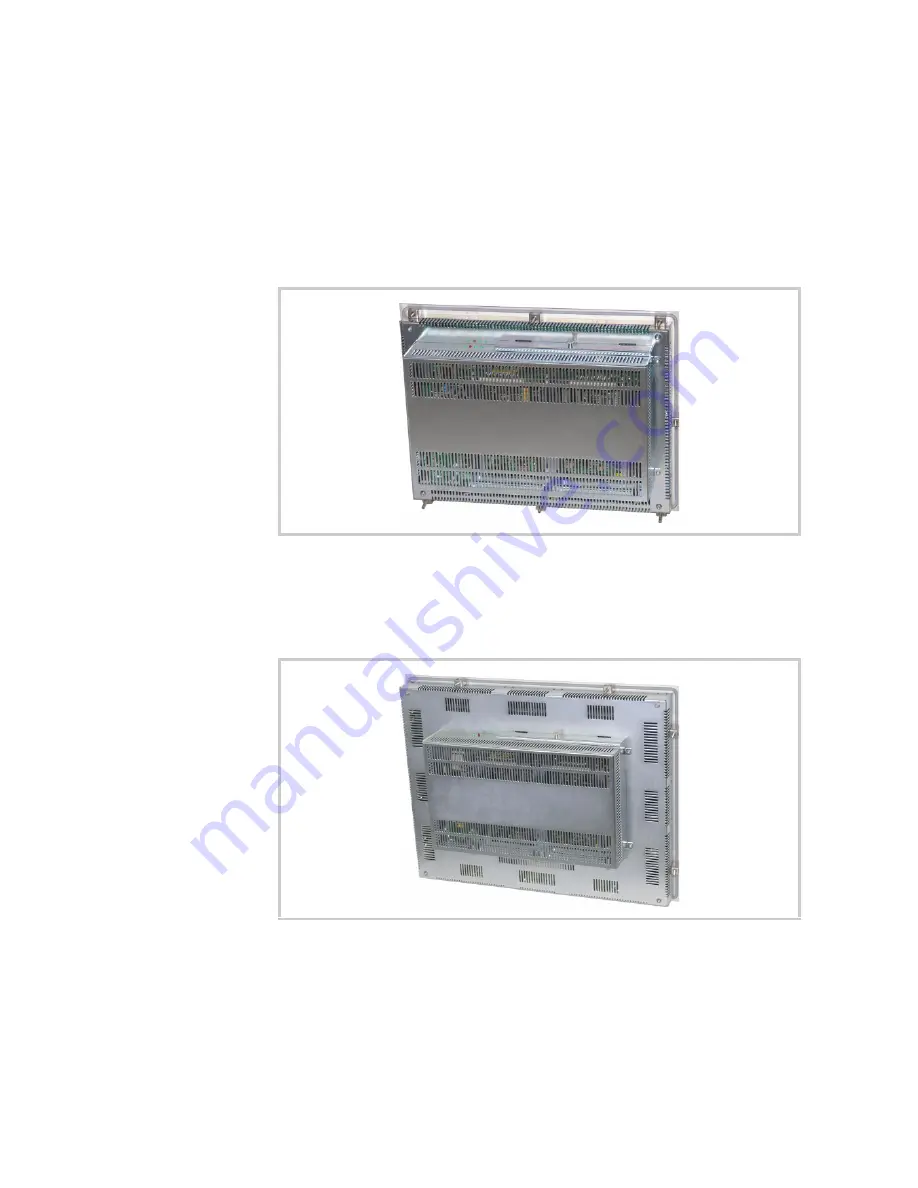
5 Installation
5.4 Mounting
52
MICRO PANEL XV400 10.4"/12.1"/15"
12/2010 MN04802010Z-EN
www.eaton.com
10.4" and 12.1" devices which must be mounted in accordance with IP65 or used in potentially
explosive atmospheres:
Top and bottom of the device:
One retaining bracket at each of the fixing positions (left, right and in the center)
Left and right on the device:
One retaining bracket each at the central fixing position
15" devices (standard mounting):
Top and bottom of the device:
One retaining bracket each at the second fixing position from the left and from the right
Left and right on the device:
One retaining bracket each at the top and bottom fixing position
Fig. 42 10.4" and 12.1" devices with eight retaining brackets (meet IP65 requirements)
Fig. 43 15" devices with eight retaining brackets (do not meet IP65 requirements)