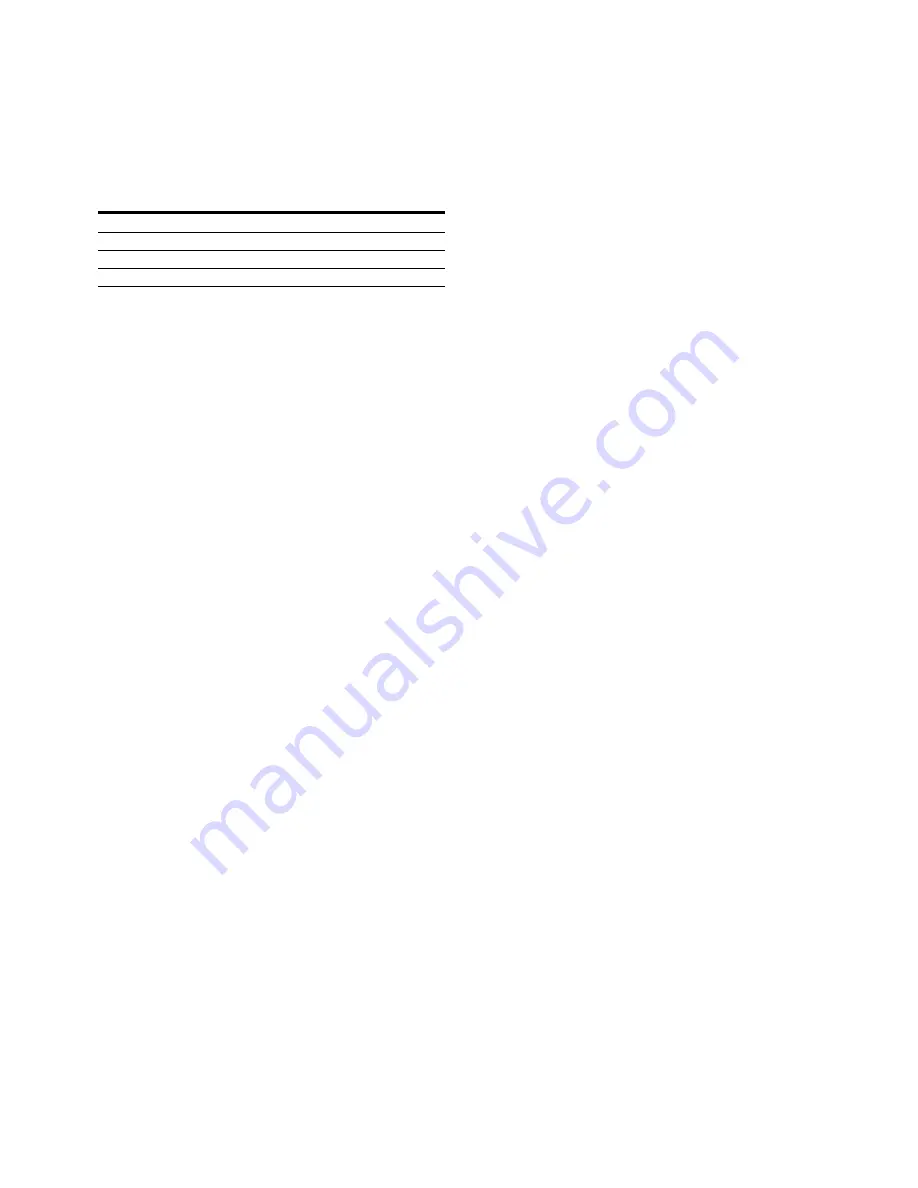
15
EATON Vane Motors M-2740-S June 2011
4.
Vanes and Rotor.
Position the ring on a flat surface and
insert the rotor and vane assembly 1/4 way into the ring.
Use a suitable size hard wood plug as a driver for
positioning the rotor and vane assembly (see Table 5).
Release the compressor carefully so the vanes do not
snap out against the ring surface. With the hard wood
plug, press the vanes and rotor flush with the ring.
NOTE:
Vanes may become cocked if not pushed down
uniformly.
5.
Cartridge Pins.
Install the cartridge pins on the body end
pressure plate (plate without bushing). Place the rotor,
ring and vane assembly over the pins on the plate.
6.
Cover End Pressure Plate.
Install the cover end pressure
plate against the rotor and ring. The porting in this plate
will be 90 degrees from the other plate. Carefully install
the two cap screws in the cartridge. Tighten the screws
to values shown in Figure 9 being certain the peripheral
edges of the ring and plates are flush. Tap with a plastic
hammer if necessary to effect alignment.
7.
O-Rings and Back-Up Rings.
Install backup rings first
and then o-rings on the pressure plate hubs. Grease with
petroleum jelly. Inspect this assembly to insure that the
o-ring is positioned in the concave side of the back-up
ring.
8.
Cartridge Installation.
Clamp the body in a vise with
protective jaws. Assemble the hub adapter on the
cartridge pressure plate (body end). Install back-up
ring and then the o-ring on the hub adapter. Grease with
petroleum. Install the cartridge on the shaft, with the
hub adapter toward the body. Tap the cartridge into
position. Install the retaining ring in the body.
9.
Cover Assembly.
Install the o-ring in the cover, greasing
liberally. Carefully install the cover, being sure the locating
pin engages the pin hole in the cover. To check
engagement, turn the cover 30 degrees in both directions
and be certain the cartridge moves with it. Install four
cover bolts and tighten requirement shown in Figure 9.
Testing
If test equipment is available, the motor should be tested
at the recommended speeds and pressures shown on the
installation drawings (Table 1).
Motor Size
Diameter
Approx. Length
25M-20 2.80 1.50
35M-20 3.36 2.00
45M-20 3.95 2.50
50M-20 4.50 2.75
Table 5. Rotor Driver Dimensions