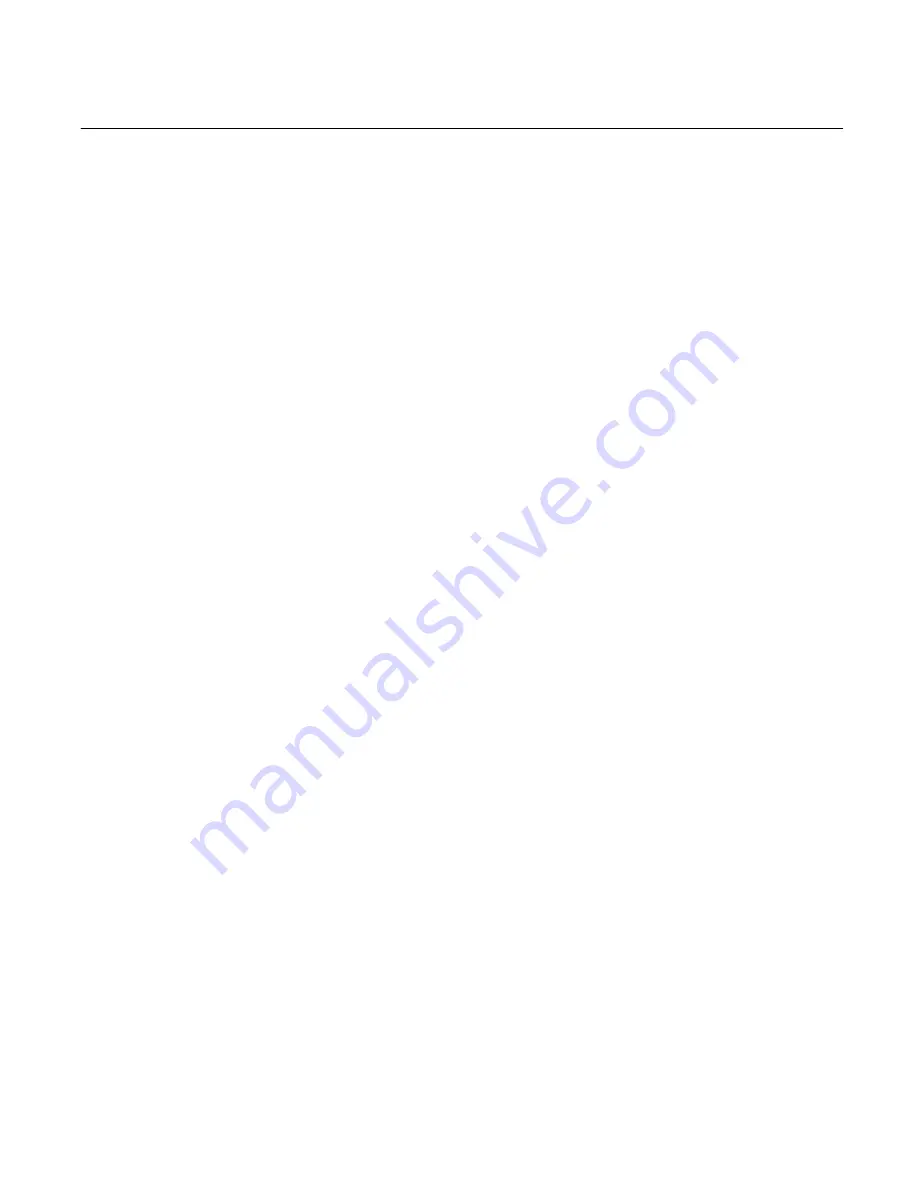
9
4. Turn knob (1) counterclockwise and remove knob
from valve cover (14).
NOTE
An adjusting screw replaces the knob on C*5
models.)
5. Remove parts (3) through (8). Inspect poppet (8) for
damage to sealing surface. If poppet (8) is damaged, replace
with a new cover subassembly.
6. Inspect seat (12) for nicks, scratches, and washout.
If the seat shows evidence of damage, replace with a new
cover subassembly. DO NOT attempt to remove seat (12)
from cover (14).
7. If seat (12) is in good condition, remove plug (9), seal
(10), and spacer (11).
NOTE
Space (11) exists on C*-10-**-** models only.)
8. Remove four screws (13) from cover (14), then disas-
semble the cover from body (21).
9. Remove parts (15) through (18) from body (21).
Inspect piston (18) sealing surface for heavy scratches and
other damage. Discard seal (15).
10. If piston (18) is damaged, turn valve body (21) in vise
so tank port faces up. Insert a rod (reference Figure 3) into
the tank port against seat (19.) Tap on rod end with hammer
and remove the seat (19) from body (21). For C*-H**-30/50
models, insert rod against sleeve (20) and remove sleeve
and seat at the same time.
NOTE
The following step refers to CG models only.
11. If piston (18) is damaged, secure body (21) in vise so
mounting surface is face up. Insert a screw through seat
(19). See Section VI, B and Figure 4 for removal of seat (19).
12. Remove plug (22) from body (21). Remove seal (23)
from plug (22).
13. Discard seals (6), (10), (15) and (23).
D. Disassembly (C*5 Models)
Except for removal of the solenoid operated directional valve,
the disassembly sequence of a C*5 valve is essentially the
same as a standard relief valve.
1. Remove the four nameplate screws (a) and loosen
nameplate (b) from directional valve cover (c).
2. Loosen four screws (d) and remove directional valve
(e) from valve cover (f).
3. Discard seals (g).
4. Disassemble the relief valve per Section VI, C and
follow Figure 5.
NOTE
This manual does not cover the repair and/or over-
haul of solenoid operated directional valves. If the
directional valve causes the relief valve to become
inoperative, obtain the necessary parts and service
information for directional valves.
E. Inspection, Repair & Replacement
NOTE
All parts must be thoroughly cleaned and kept clean
during inspection and assembly. The close toler-
ance of the parts makes this requirement very
important.
NOTE
Reliable operation throughout the specified operat-
ing range is assured only if genuine Vickers parts
are used. Sophisticated design processes and
materials are used in the manufacture of our parts.
Substitutions may result in early failure.
NOTE
Replace all parts that do not meet the following
specifications.
1. Inspect all screws (13) for evidence of damaged
threads. If threads are damaged, replace the screws.
2. Inspect springs (7), (16), and (17) for distortion or
damaged coils. Replace springs if coils are damaged.
3. Inspect the piston (18) to cover (14) clearance. Insert
the piston into the cover and check for looseness. A close
tolerance fit is mandatory for proper valve operation. If a
loose fit is noted, the cover is worn and must be replaced.
4. Inspect the piston (18) to body (21) clearance. The
piston should have a close tolerance fit as noted in step 3. If
the piston is loose inside the body bore, replace the body
and seat (19).
5. Inspect piston (18) for nicks or scratches across the
sealing surface. Make sure the balance hole in the piston is
free from foreign material. Remove minor scratches on piston
with 500 grit polishing paper. If the piston has heavy
scratches, replace the piston (18), seat (19), and body (21).
6. Inspect poppet (8) and seat (12) for heavy wear or
evidence of washout. Replace both the poppet and seat if
heavy wear or washout is noted.