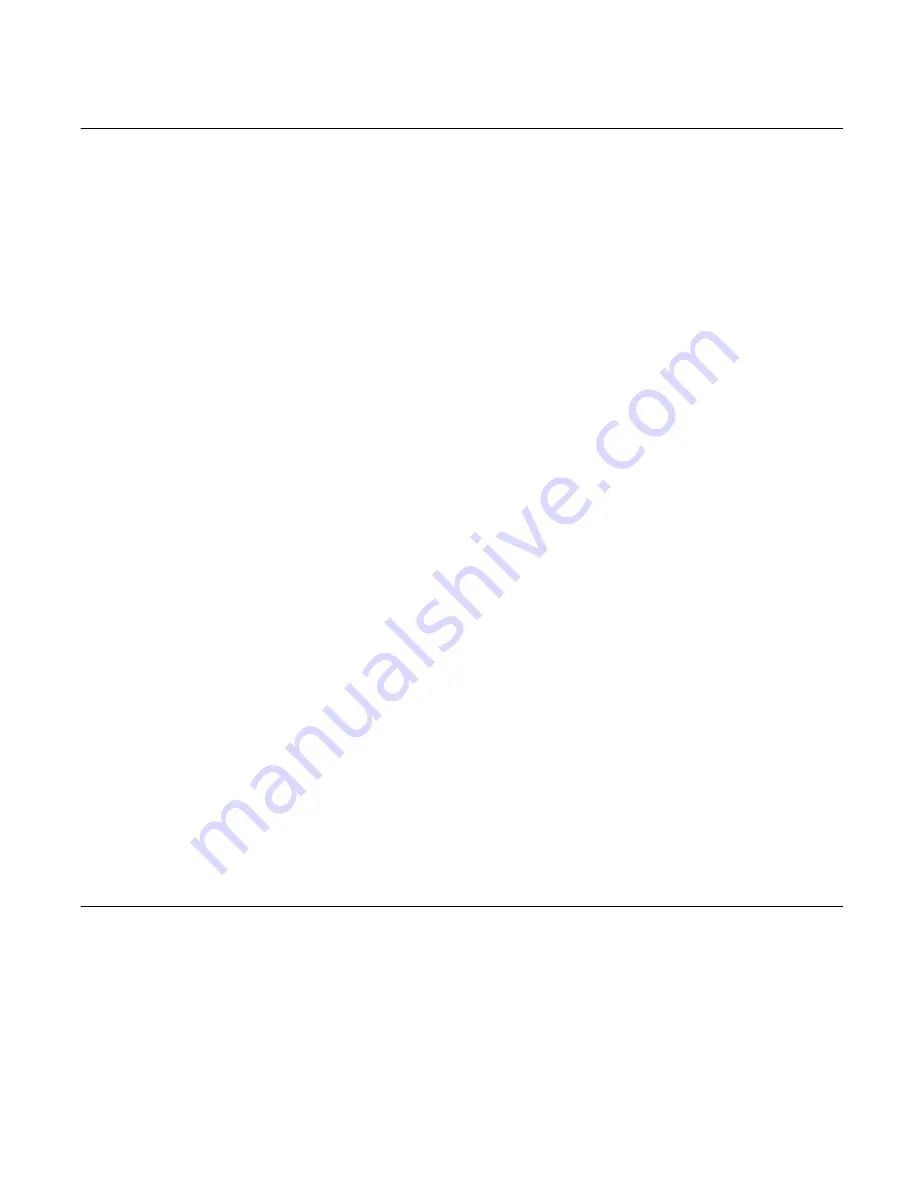
11
7. If seat (19) was removed during disassembly, make
sure inside of body (21) is clean and free from damage.
8. Inspect mounting surfaces on cover and body for
burrs, nicks, or scratches. Remove burrs and/or scratches
with India stone or polishing paper. Also check body and
cover for damaged or worn threads. If threads are worn or
damaged, replace the part.
F. Assembly
Assembly of parts will be in reverse numerical sequence as
shown in Figure 5. Obtain new seals. Seal kits are noted on
the parts and service drawings that are tabulated in Section
I, B. Make sure all parts are clean prior to assembly.
Lubricate all parts with a light film of clean hydraulic fluid.
1. Secure body (21) in a vise.
2. If sleeve (20) was removed during disassembly, insert
the sleeve into bottom of body bore.
NOTE
This step applies to C*-H**-30/50 models only.
3. If seat (19) was removed, install new seat into body
(21) as follows:
a. Lubricate seat with petroleum jelly or grease that is
compatible with system fluid.
b. Position the seat square over the body bore. Place
a rod against the seat. Hold the rod centered. Tap on end of
rod with hammer until seat is started into body, then drive the
seat into the body bore until it bottoms out. Inspect the body
and seat to be sure no chips or metal shavings were
developed.
4. Install parts (18) through (15).
NOTE
Spring (16) is used on high vent models only (‘V’ in
the model code).
5. Slide piston (18) back and forth within the body bore.
Also rotate the piston 360
°to make sure piston movement is
free and without bind
.
6. Assemble cover (14) to body (21). Cross tighten four
screws (13) evenly. Torque the screws to 14.9-20.3 Nm.
(133-178 lb. in.).
7. Secure valve body in vise to a horizontal position.
Place screwdriver or similar tool in tank port against bottom
of piston (18). Push the piston up and down within the body.
If the piston hangs up or binds, loosen screws (13) on cover
(14) to snug condition. Lightly tap around cover perimeter
with a soft tip hammer until the piston moves freely within the
body bore. Retighten the cover screws.
8. Install parts (11) through (9).
NOTE
Restriction plug (11) exists in C*-10-** models only.
Torque plug (9) to 22.6-27.1 Nm. (200-240 lb. in.).
9. Install parts (8) through (3). Be sure to install the
same quantity of spacers (4) that were removed. The
spacers determine the pressure adjustment range of the
valve. Make sure seal (6) is assembled on plunger (5).
10. Install parts (2) and (1). Thread knob (1) in retainer (3)
approximately five complete turns.
NOTE
The following step applies to C*5 solenoid operated
relief valves only.
11. Assemble directional valve on cover in reverse alpha-
betical sequence as shown in Figure 6. Torque screws (d) to 5.6
Nm. maximum (50 lb. in.).
Section VII – Start-up and Test
A. Start-up
Start the system and sequence the unit through all positions
while watching for appropriate movement of actuators.
Improper or erratic movement of the actuators may indicate
incorrect assembly of the unit or presence of trapped air.
B. Test
A test stand having regulated flow, temperature control and
special fixtures is required to fully test the performance of the
rebuilt unit. Because of this, only the functional test shown in
the start-up paragraph is given. If such a test stand is avail-
able, test the unit to the requirements set forth in the installa-
tion drawings.