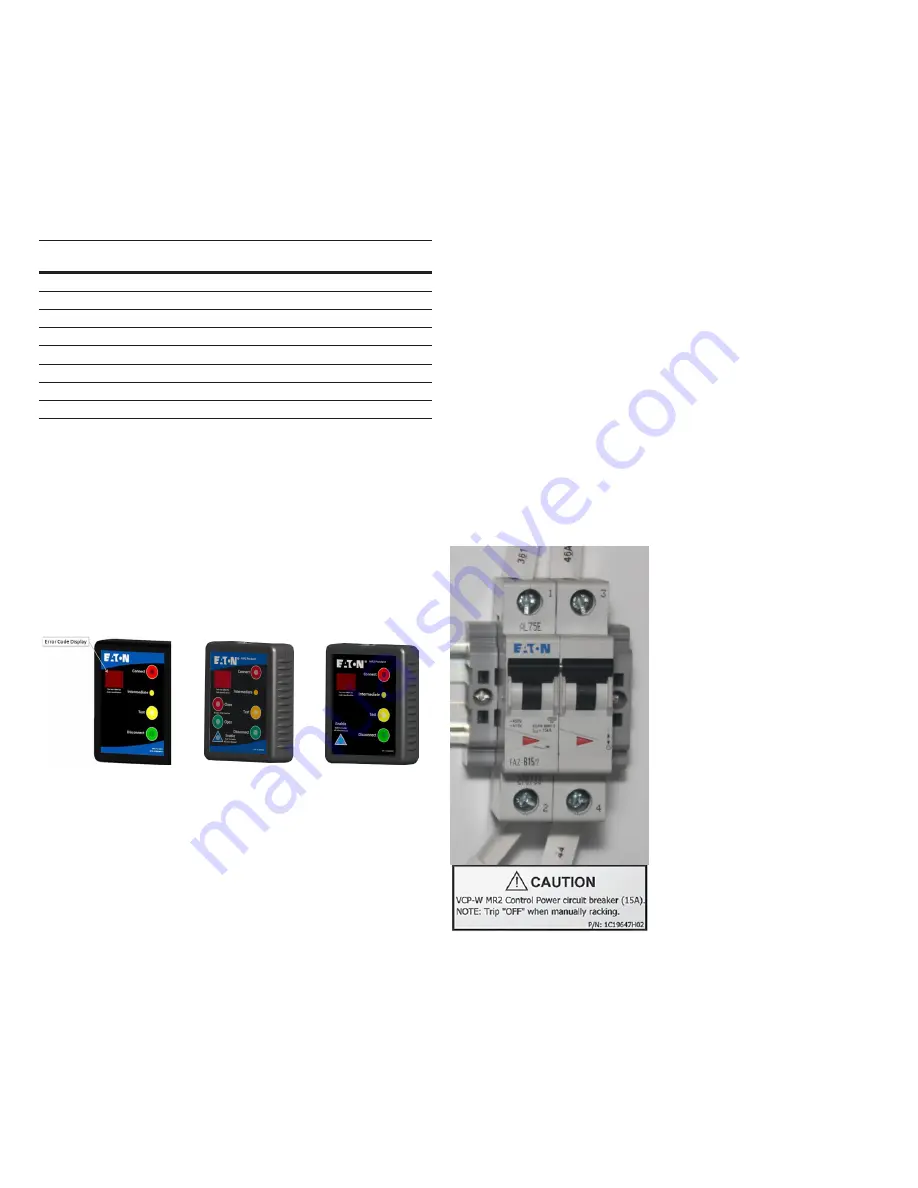
10
Instructional Booklet
IB022010EN
Effective July 2019
Revision #4
Instructions for installation, operation,
and maintenance of medium voltage
VC-W MR2 (integral racking)
EATON
www.eaton.com
Method 2
, applies to pendant without enable button .
On power up if both connect and disconnect positional limit
switches are closed then the controller will look to see what series
of I/O controls are closed . The gear type is then set depending on
what pushbuttons are closed . The gear type can then be verified
with the diagnostic display . Below are the sequences of closed
contacts to set each gear type .
Closed contacts upon power-up
Gear type
Positional limit switches
(ref
I/O Controls jumper
01
“Disc” & “Conn”
Pin 8 to pin 1
02
“Disc” & “Conn”
Pin 8 to pin 2
03
“Disc” & “Conn”
Pin 8 to pin 3
04
“Disc” & “Conn”
Pin 8 to pin 1 and 2
05
“Disc” & “Conn”
Pin 8 to pin 2 and 3
06
“Disc” & “Conn”
Pin 8 to pin 1, 2 and 3”
07
“Disc” & “Conn”
None
15
“Disc” & “Conn”
Pin 8 to pin 1 and 3
Procedure:
Step 1.
- Using an Ethernet cable and a RJ485 to 8 pin terminal
block adapter . Connect one end of the Ethernet cable to the
discrete I/O control connection shown on
. Connect the
other end of the Ethernet cable to the RJ485 connection shown on
Setting the Modbus address
If the enable button is present (
) the enable button
must be held to operate the pendant . The Modbus address of a
controller board is set using the pendant . The available MODBUS
addresses are 01 to 99 for one RS485 network .
To set the MODBUS address, follow the steps below:
1 . Connect pendant to the cell to be programmed .
2 . Hold down the “Intermediate” button and within 3 seconds
press and hold the “Connect” button until the 2-digit LED display
begins to flash “##”, at the same time the “Connect” LED will
begin to flash .
3 . Now the “Test” and “Disconnect” buttons can be used to scroll
up and down (01 to 99) until the desired address number is
reached . While scrolling, the “Connect” LED will continue to
flash to let the user know that the address is not set .
4 . Once the desired address number is reached, press the
“Connect” button to connect to the Modbus address displayed .
5 . Press “Disconnect” to return to operation mode .
6 . At this time the address can be verified using the controller
diagnostic display described above .
The MODBUS address can be modified after being set using the
same sequence .
ote:
N
See Instruction Booklet IB022022EN for information on the MODBUS
interface to VCPW-MR2 and VCPW-HD controllers .
Manual racking
Follow the steps listed below to manually rack the MV device in the
case of a motor/controller failure or loss of control power .
1.
Turn “Off” the 15 A two-pole LV circuit breaker mounted in the
LV compartment (see
) .
a.
This action does two things:
1.
It ensures that the motor will not turn on during
manual racking .
2.
It prevents the motor from back feeding voltage
and causing the user to apply excessive torque to
the lead screw .
2.
Once the LV circuit breaker is turned “Off,” the operator can
insert the standard racking tool (for 5/15 kV 1/4 high auxiliary
drawers, use a standard 1/2” socket) and rack the MV device to
the connected or disconnected position .
a.
This will require slightly more torque than normal because it
will be driving through the motor gearbox .
In the case that the motor is jammed and the lead screw does not
turn freely or with less than 35 ft-lbs (47 .45 N∙m) of torque, the
operator can apply approximately 70 ft-lbs (94 .91 N∙m) of torque
and the lead screw will break away from the motor . Once the lead
screw has broken free from the motor, the MV device can be racked
manually . The unit should then be inspected and a new lead screw
installed .
Figure 11. 15 A circuit breaker.
Terminals 1 and 2 are the 120 VAC power supply .
Terminals 3 and 4 are the 140 VDC motor circuit .