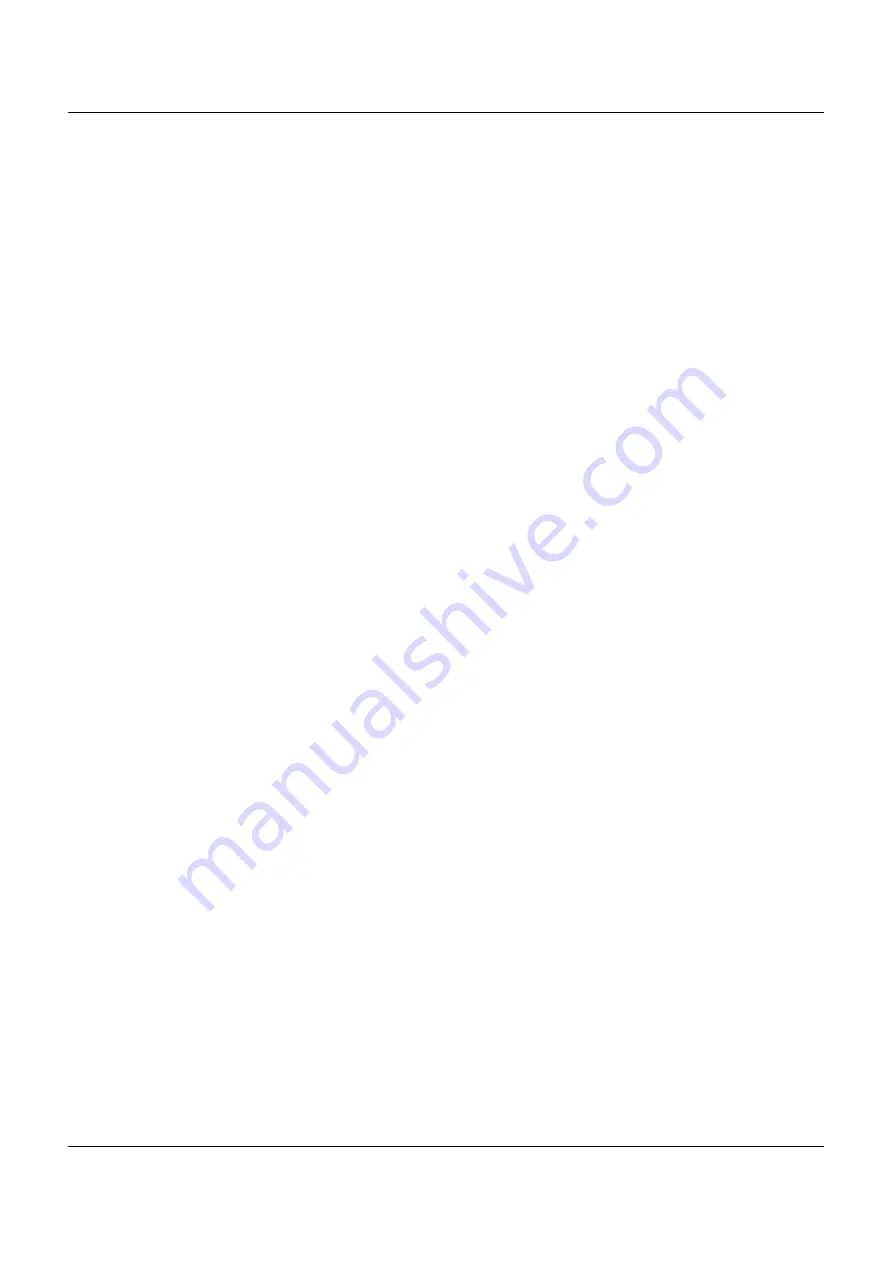
O & M Manual IM05805020K
EATON LMR Plus
Effective September 2013
Electric Fire Pump Controllers
The controller should be located or so protected that it
will not be damaged by water escaping from pumps or
pump connections. Current carrying parts of controllers
shall be a minimum of 12 inches (305mm) above the
floor.
Prior to starting, verify all data on the nameplate such as:
catalog number, AC line voltage, horsepower, and
frequency.
Inspect all electrical connections, components, and
wiring for any visible damage. Correct as necessary.
Ensure that all electrical connections are tightened
before energizing.
Refer to the wiring schematic affixed to the enclosure
door for all wiring information pertaining to the incoming
AC power supply and motor wiring.
Install necessary conduit using proper methods and
tools.
Incoming AC line voltage is clearly marked L1, L2, L3,
and ground, located at the top of the enclosure.
2.3.1 Wire Sizes
For control wiring, use #14 AWG wire for all electrical
connections.
For power wiring sizes refer to Appendix K.
2.3.2 Electrical Checkout Instructions
To ensure the pump does not start upon energizing the
controller, the interlock circuit is enabled with the
installation of a jumper between terminals 39 and 49.
Energize the controller to determine the status of the
controller. If it is determined that the controller will not
start the motor, this jumper can be removed.
The LMR Plus controller is designed to be phase
sensitive. L1, L2 & L3 should be connected to A, B & C
respectively. Energize the controller by closing the
isolation switch (MIS) and circuit breaker (CB). If the
phases are connected incorrectly, the 'Phase Reversal'
LED on the alarm display will be lit. To correct this
condition, refer to Appendix F to correct the phase
reversal setting. Re-energize the controller.
With the controller energized, operate the 'Start'
pushbutton immediately followed by the 'Stop' button to
check the rotation of the motor. If the rotation is incorrect
disconnect power and reverse connection of the load
terminals of the motor contactor T1, T2 & T3.
Note:
On models Primary Resistor (FD40), Wye Delta
(Star-Delta) Open (FD70) and Wye Delta (Star-Delta)
Closed (FD80) models, the connection must be changed
on both contactors.
Adjust the pressure set points detailed in Appendix D.
With the controller isolated and the 'Start Pressure' and
'Stop Pressure' values programmed, energize the
controller. If the system water pressure is lower than the
start pressure, the pump will start. If the controller is set
up for fully automatic operation, the pump will stop when
the pressure is above the stop point and the running
period timer (RPT) has completed its timed interval. If the
controller is setup for semi-automatic operation
(programmed for manual stop mode), the stop
pushbutton must be operated to stop the pump. Note
that the system pressure must be equal to or greater
than the programmed stop pressure value, otherwise the
pump will stop only when the pushbutton is pushed.
The circuit breaker setting is factory set and should not
be adjusted.
The running period timer (RPT) must be set for a
minimum of ten (10) minutes. Refer to Appendix E for
programming of the RPT.
If the sequential start timer (SST) is required refer to
Appendix E. If not required set the SST to disabled. If
required, the lead pump SST should be set to disabled
and the lag SST to five (5) to ten (10) seconds. If there
are more than two pumps in the system, allow a ten (10)
second delay between pumps.
The acceleration timer (AT) is used for reduced voltage
controllers only. The AT is factory set based on the
starting method of the controller. If it is found that more
time is required to allow the pump to come up to speed,
the timer may be adjusted to suit. Refer to Appendix E
for programming of the AT.
If the Undervoltage/Overvoltage alarms are present,
check the programmed values by referring to Appendix
F. If the values are programmed to their maximum and
the alarms continue to occur, check the main voltage
supply to ensure that the power available is dependable
as per NFPA, Pamphlet 20 standards.
3. HARDWARE DESCRIPTION
3.1 General
The purpose of this section is to familiarize the reader
with the LMR Plus Controller hardware, its
nomenclature, and to list the unit's specifications.
3.2 Front Operator Panel
The front operator panel, depending on the installation,
is normally accessible from the outside of the door. The
front panel provides a means to:
Alert the user to specific conditions
Program the controller
Set and monitor the operating parameters
The LMR Plus Controller front panel serves two primary
functions: output and input. The output function consists
of:
A four-line, 40 character LCD display module
Twenty LED outputs: Power On, Pump Running,
Local Start, Remote Start, Deluge Valve, Emergency
Start, Interlock On, Low Pressure, Phase Reversal,