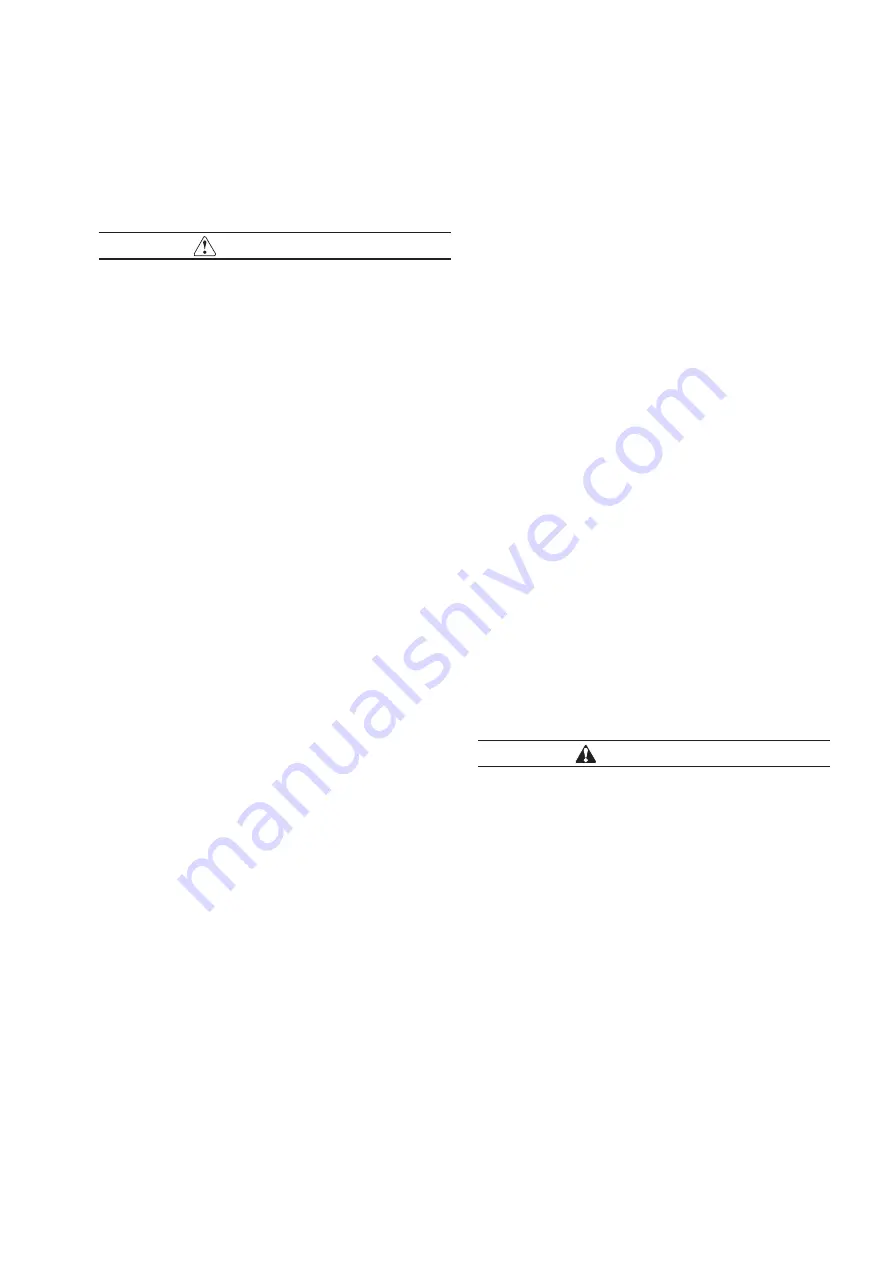
General Safety Instructions
3
HYDROKRAFT OPERATION MANUAL PVW 250+360
E-PUIO_II001-E April 2021 www.eaton.com
2. General Safety Instructions
Preface
We would like to thank you for choosing a product from
Eaton Germany GmbH.
IMPORTANT!
Please read the information carefully before you put the
pump into operation.
In accordance with the state of the technology, the
information in this document can be modified at anytime
without prior notification.
Only if you respect the present instructions, accidents and
material damages can be avoided and operating without
any complications can be guaranteed.
The present instructions apply solely to the pump
and do not replace the operating instructions of the
complete machine.
Eaton Germany GmbH does not assume any guarantee or
liability for errors in these instructions or any subsequent
damages in relation with the delivery
2.1 Application range
These general operating instructions only apply to Eaton
Hydrokraft axial piston units PVW manufactured by Eaton
Germany GmbH.
2.2 Limits of the partly completed machinery
The Eaton Hydrokraft PVW pump from Eaton Germany
GmbH is a partly completed machinery according to
the machinery directive 2006/42/EC article 2g and is
intended for the assembly in or with another machine
or equipment.
The limit of the partly completed machinery is in the main
connections on the machine side of the aggregate.
This partly completed machinery must only be taken into
operation once it has been ensured that the machine, in
which the partly completed machinery is to be assembled,
meets the expectations of the machinery directive.
2.3 Operating and environmental conditions
If the technical specification does not mention any other
data, the following conditions apply.
•
Eaton Hydrokraft PVW pump are usable for mineral-
oil based hydraulic medium in accordance with ISO
6743-4 (for other hydraulic medium have a look in chap.
Hydraulic Fluids).
•
The type and model of pump is indicated on nameplate.
•
For permissible operation temperatures, viscosity etc.
have a look to chap. Technical Data and Hydraulic Fluids.
•
Cleanliness level of hydraulic medium
The recommended purity level according to ISO 4406:
18/15/13 or better
•
Operating pressure:
Please consider the maximum operating pressure in
the technical documentation
•
Operating in an explosion risk environment:
Eaton Hydrokraft piston pumps cannot be operated
in an explosion risk environment, beside this has
been explicitly stated in the assembly notice
.
•
Water-imperilling substances:
Hydraulic medium based on mineral oil are part of
the products susceptible to pollute the water. Their
taking into operation represents high danger for
human-beings and the environment.
•
Both the respective legal or otherwise binding regu-
lations of the European and national legislation must
be observed, as well as all rules for the prevention of
accidents and for environmental protection applicable
in the country of operation.
2.4 Intended use
Eaton Hydrokraft axial piston pumps are developed and
manufactured in accordance with the state of technology
and the safety-related directives of MD 2006/42/EC. The
pump is intended to be operated only according to the
technical specifications.
During operation, endangering of users or third parties
or damaging of hydraulic aggregates and other elements
might be possible, especially when the assembly instruc-
tions are disregarded. Any use other than specified
applies to be unintended.
The present assembly notice lapses if modifications,
which have not been agreed by the manufacturer, are
performed on the axial piston pumps.
WARNING!
In case of non-intended use and the damages occurred
through it, no liability or material claim applies (explicit
in contractual documents).
2.5 General safety advice
•
The Eaton Hydrokraft axial piston pump is manufactured
and verified according to the state of technology. Even
if all risks are identified and all measures to reduce the
probability of damage-occurrence have been taken in
the risk evaluation, remaining risks (non-apparent) can
never be completely excluded.
•
According to amendment II B of the machinery direc-
tive 2006/42/EC, the partly completed machinery can
only be taken into operation, if the machine, in which it
is assembled, meets the directives.
•
When assembling, you must also consider
dangers stipulated in the instruction manual of the
complete machine.
•
Any modification of the partly completed machinery can
present important changes in the sense of machinery
directive 2006/42/EC. Supplementary safety require-
ments must be considered. For this reason, modifica-
tions should always be approved by the manufacturer.