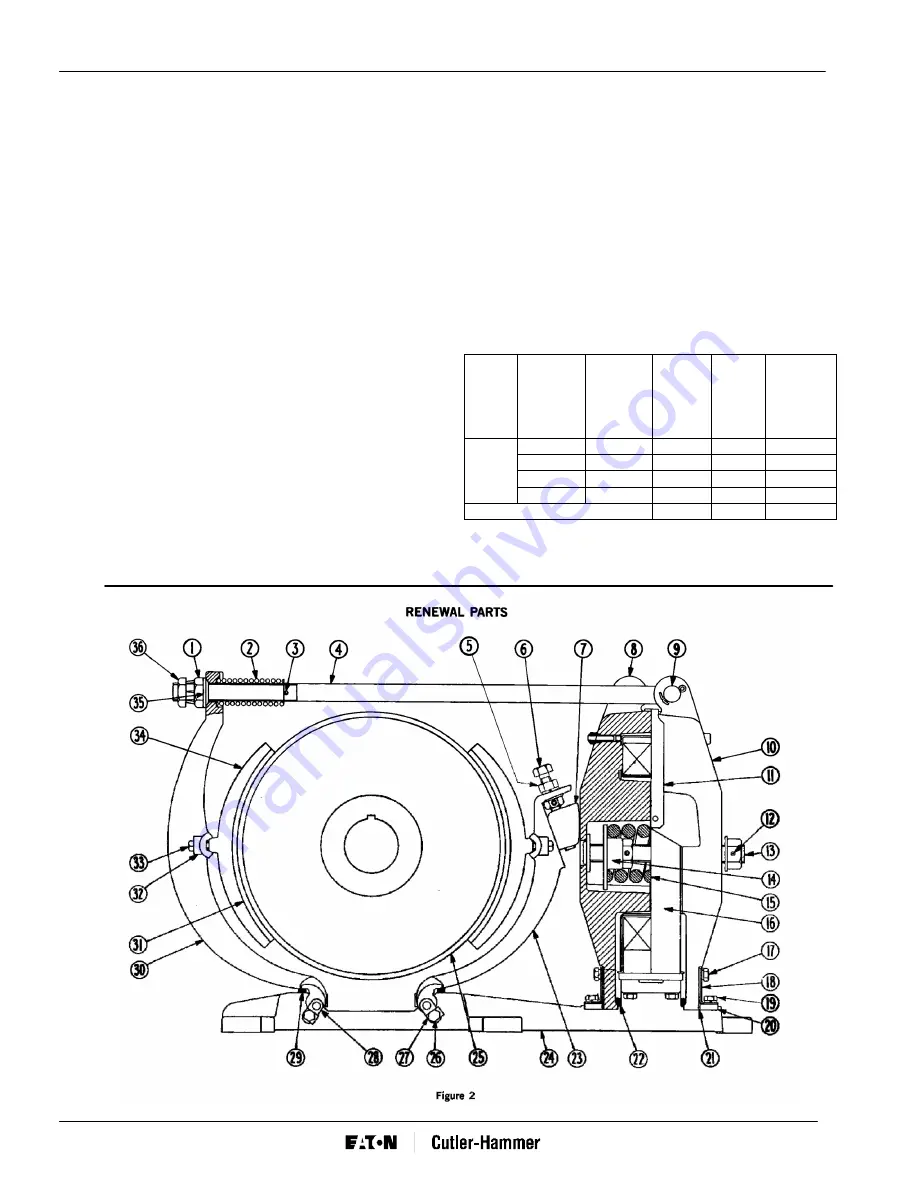
MADE IN U.S.A PAGE 2
PUBLICATION NO.
17228
9.
Be sure there is some spring pressure tending to
separate the two armatures “D” and “F”. This can
be tested by turning nut “G” clockwise. If nut “G”
cannot be turned, the gland inside is tight against
the stop on the screw and a maximum spring
pressure is applied.
10.
Turn the screw “C” on the top of the inner shoe
lever counter-clockwise to move the wedge
downward until the inner armature “D” sounding
pin “E” is flush when pressed. Tighten locknut “T”.
Readjust after wheel has reached normal
operating temperature to allow for thermal
expansion of the brake wheel. Re-inspect and
adjust if necessary after several operations.
11.
Tighten the pull rod nut “P” until the outer armature
“F” sounding pin “E” is flush when pressed. Tighten
locknut “U”. Readjust after wheel has reached
normal operating temperature to allow for thermal
expansion of the brake wheel. Re-inspect and
adjust if necessary after several operations.
12.
Full torque is obtained by turning the torque
adjuster “G” until the gland inside is snug against
the stop. Less than full torque is obtained by
turning the torque adjuster “G” counter-clockwise.
Check the nameplate on the brake and the table in
paragraph 14 for maximum torque setting for the
duty rating of the brake.
13.
With the brake set, tighten screws “K” on the shoes.
14.
Note that when the brake is correctly adjusted for proper
stroke, the torque adjuster washer face stands clear of the
armature “F” surface. As the lining wears this clearance
decreases. If the adjustment is neglected, the brake
operation can become sluggish and when the torque
adjuster washer touches the armature, the torque drops
rapidly reaching zero when the flexure of the lever is used
up. The clearance dimension is not a measurable value
but is determined by proper adjustment of individual
brakes.
TORQUE ADJUSTMENT
Size
Of
Brake
Coil
Winding
Duty
Rated
Torque
Turn
“G”
Clock
wise
To
Solid
Back Off
Turns If
“G” From
Solid
Shunt
Int.
4000
X
0
Shunt
Int.
3000
X
1-5/6
Series
½ Hour
4000
X
0
23”
Series
1 Hour
2600
X
2-3/6
Minimum Torque
1000
X
3-4/6
PROCEDURE FOR INSTALLATION AND OPERATION – (Continued)