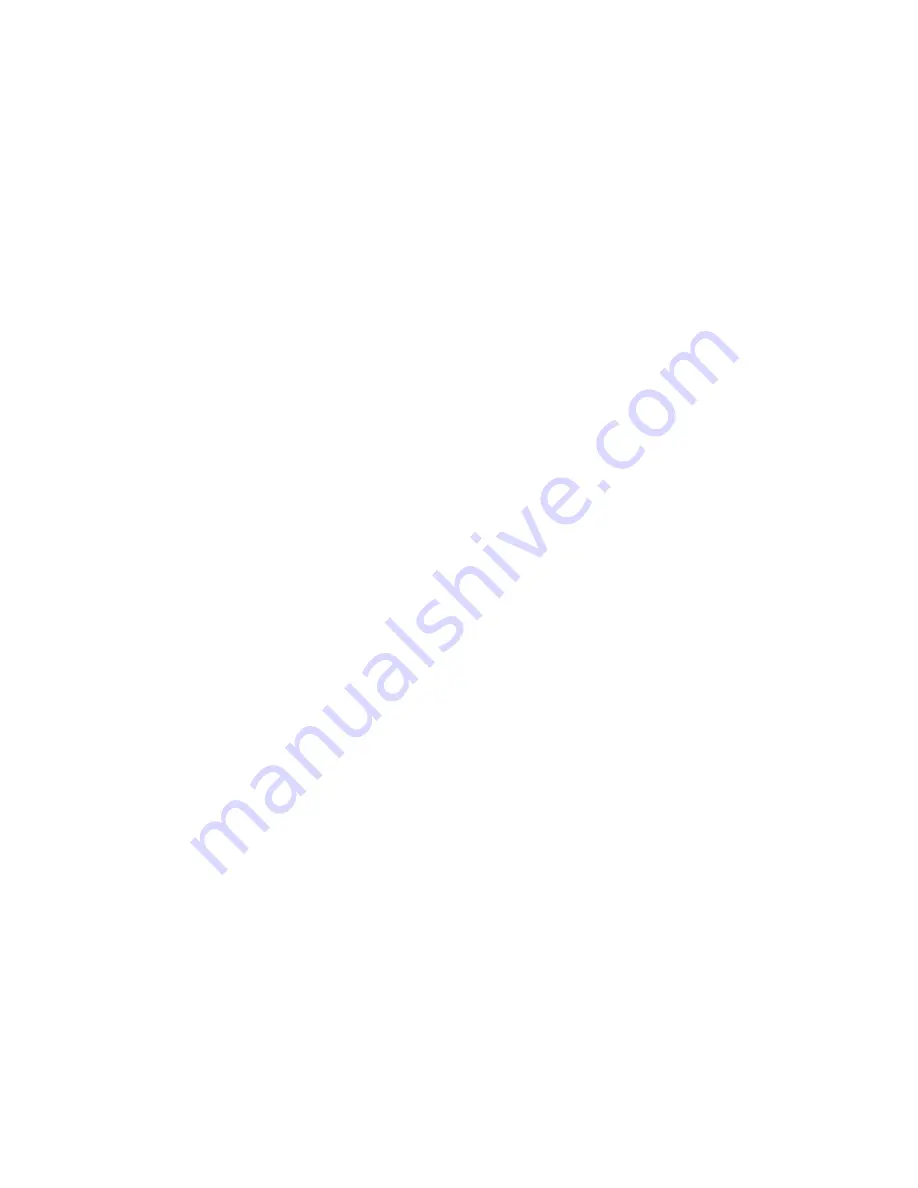
- Page 25 -
I.B. 8926-1
recessed in the handle may be extended and padlocked
with from one to three padlocks. See Figure 34.
With the door open and the disconnect device OFF, the
operating handle is mechanically interlocked to prevent
inadvertently being pushed ON. To defeat this interlock,
the bar on the top of the mechanism should be pushed
in slightly, allowing the handle to move upward to the
ON position. WARNING: IF FULLY INSERTED, THE
POWER AND CONTROL CIRCUITS WILL BE ENER-
GIZED. Padlocking to prevent this handle movement
may be accomplished by the same method as described
above.
Separate control sources of power must also be dis-
connected. If control power is used during main-
tenance, take steps to prevent feedback of a hazard-
ous voltage through a control transformer. Be alert
to power factor correction capacitors that may be
charged. Discharge them before working on any part
of the associated power circuit.
Cleaning. Soot, smoke, or stained areas (other than
inside arc chutes), or other unusual deposits, should be
investigated and the source determined before cleaning
is undertaken. Vacuum or wipe clean all exposed sur-
faces of the control component and the inside of its en-
closure. Equipment may be blown clean with com-
pressed air that is dry and free from oil. (Be alert to built-
in oilers in factory compressed air lines!) If air blowing
techniques are used, remove arc covers from contac-
tors and seal openings to control circuit contacts that
are present. It is essential that the foreign debris be
removed from the control center, not merely rearranged.
Control equipment should be clean and dry. Remove
dust and dirt inside and outside the cabinet without us-
ing liquid cleaner. Remove foreign material from the out-
side top and inside bottom of the enclosure, including
hardware and debris, so that future examination will re-
veal any parts that have fallen off or dropped onto the
equipment. If there are liquids spread inside, determine
the source and correct by sealing conduit, adding space
heaters, or other action as applicable.
Mechanical checks. Tighten all electrical connections.
Look for signs of overheated joints, charred insulation,
discolored terminals, etc. Mechanically clean to a bright
finish (don’t use emery paper) or replace those termina-
tions that have become discolored. Determine the cause
of the loose joint and correct. Be particularly careful with
aluminum wire connections. Aluminum wire is best ter-
minated with a crimp type lug that is attached to the con-
trol component. When screw type lugs (marked CU/AL)
are used with aluminum wire, joint should be checked
for tightness every 200 operations of the device.
Wires and cables should be examined to eliminate any
chafing against metal edges caused by vibration, that
could progress to an insulation failure. Any temporary
wiring should be removed, or permanently secured and
diagrams marked accordingly.
The intended movement of mechanical parts, such as
the armature and contacts of electromechanical contac-
tors, and mechanical interlocks should be checked for
freedom of motion and functional operation.
Wrap-up. Check all indicating lamps, mechanical flags,
doors, latches, and similar auxiliaries and repair, if re-
quired.
Log changes and observations into record book before
returning equipment into service. Do not remove any
labels or nameplates. Restore any that are damaged.
SLIDER OPERATOR MECHANISM- (6-inch Units)
(See Figure 35)
The following features are found on 6-inch units with cir-
cuit breaker operators.
A. Door Interlock
The operator mechanism is factory adjusted and nor-
mally does not need field adjustment. The door in-
terlock mechanism engages a hook that is mounted
to the welded bracket. This allows the unit door to
open when the operator handle is in the “off” (right)
position. With the handle in the “on” (left) position,
the door is interlocked and should not open. If the
door hook and the mechanism do not engage prop-
erly, the positioning of the door hook on the bracket
may need adjustment. The door hook can be ad-
justed left or right by loosening the screw (see pho-
tograph). After adjustment, tighten screw to 201b./
in. [2.2 N-m]. See Figure 38 insert.
B. Defeater Screw
Turning the defeater screw clockwise allows you to
open the unit door (access to the panel mounted
components) with the operator handle (padlocked
or not) in the “on” (left) position.
C. Padlocking (See Figures 36, 37 & 38)
The operator handle can be padlocked in the “off”
position with up to three 3/8" [1 9.5 mm](Max.) shank
padlocks.
To provide for padlocking the circuit breaker opera-
tor in the “on” position, drill the appropriate size hole
through the drill point located on the operator mecha-
nism.
D. Unit Interlock
The unit interlock is provided to assure that the unit
circuit breaker is:
-Open before the stab clips can contact the vertical
bus.
-Open before the stab clips can be disengaged from
the vertical bus.
The unit interlock and bracket does not need field
adjustment. The interlock bracket will be adjusted
to almost touch the side of the unit interlock rod when
the operator is in the “on” position.
Summary of Contents for Freedom 2100
Page 26: ...Page 26 I B 8926 1...
Page 32: ...Page 32 I B 8926 1 Part 11 PLAN VIEWS...
Page 33: ...Page 33 I B 8926 1...