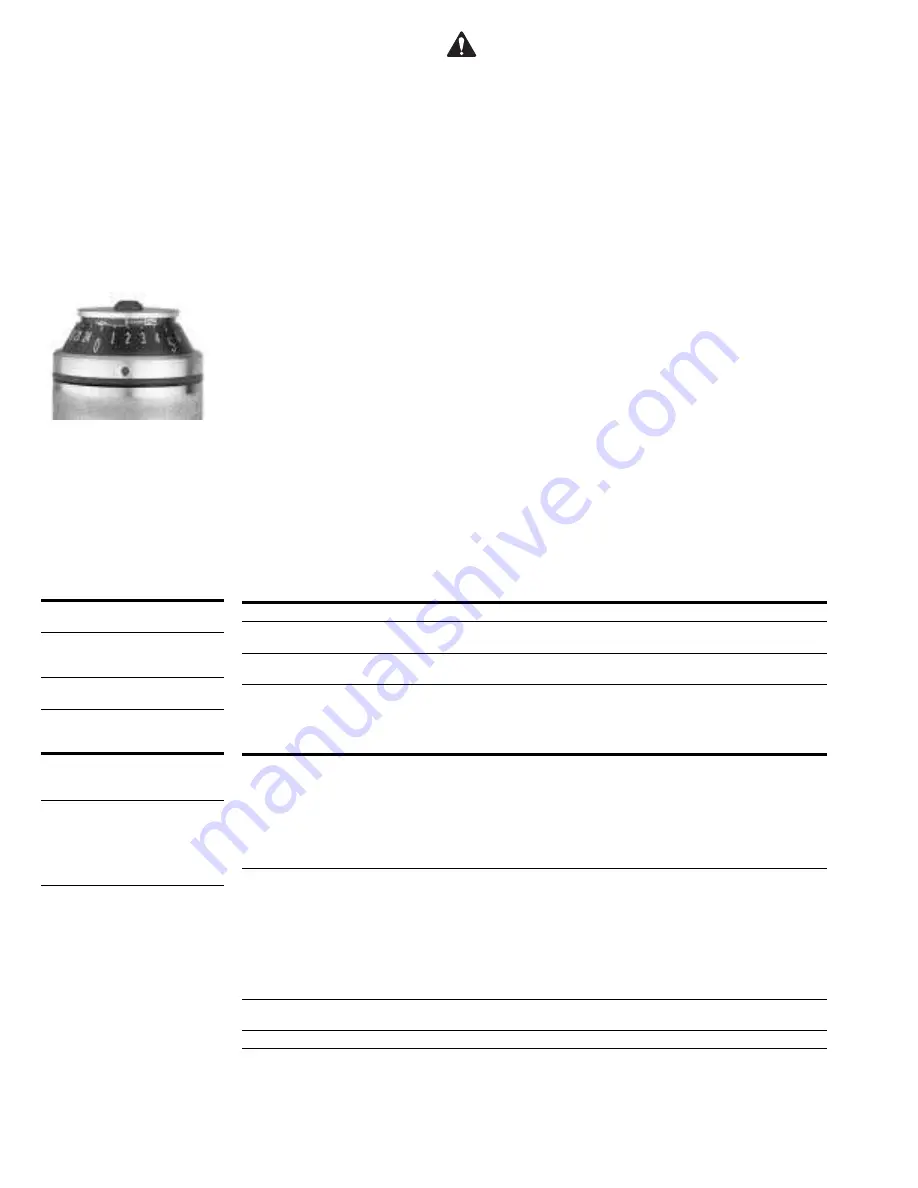
6
EATON
ET1280 Crimp Machine Set Up and Operating Manual E-EQCR-TM003-E September 2005
Calibration
The ET1280 Crimp Machine
is factory calibrated. A TTC-
8 or WeatherGRIP –8 fitting
crimped with an FT1380-
200-M240 die cage and a
machine setting of 100
should result in a socket
diameter of 1.000 +/- 0.003
inches.
If excessive wear occurs in
the crimp ring, or any of the
functional components are
replaced, a minor recalibra-
tion may be necessary. This
can be accomplished by first
loosening the two #8-32 set
screws in the adjustment
knob (see Figure 5) and then
performing the crimp
described above.
If the actual measured crimp
diameter is, for example,
1.010 inches instead of 1.000
inches, the black dial piece
can be rotated inside the
adjustment knob (leaving
the adjustment knob exactly
where it is positioned) until
the number “10” on the dial
lines up with the center ver-
tical line on the barrel.
Then rotate the adjustment
knob and dial together until
the “0” mark on the dial is
once again lined up with the
center vertical line on the
barrel. Repeat the crimp
procedure until the 1.000
inch crimp diameter is
achieved.
WARNING:
Maintain clear distance from all moving parts.
Maintenance
Intervals
DIE CAGE LUBRICATION
Every 50 crimps
Relube sliding
surfaces of dies
Every 500 crimps Remove old
grease and
relube
Every 1000 crimps Die cage
maintenance
CRIMP RING MAINTENANCE
Every 500 crimps Remove old
grease and
relube
Every 2000 crimps Remove old
grease;.
Inspect for
wear or
damage and
relube if okay.
NOTE:
Use NEVER-SEEZ lubricant
(Eaton part number FT1092).
Procedures
MACHINE MAINTENANCE PROCURES
1. Sliding surfaces must be kept free of dirt and other abrasive materials
2. All exposed black metal surfaces should be coated occasionally with a light film of oil
to prevent corrosion.
3. Periodically check the oil level in the fluid reservoir of the hydraulic power unit.
Maintain the oil level of pump manufacturer’s hydraulic oil as needed.
NOTE:
Completely retract the crimp ring when checking the oil level.
DIE CAGE MAINTENANCE PROCEDURES
1. Lubricate the die cage.
For maximum service. FT1380 die cages require lubrication at 50-crimp intervals with NEVER-SEEZ (Eaton
part number FT1092). FT1092 is an 8-ounce container that will provide sufficient lubricant
for approximately 5,000 crimps.
Periodically remove NEVER-SEEZ residue that has built-up on the sides of the dies and the crimp ring
during the crimping process. NEVER-SEEZ residue becomes contaminated with metal and plating chips
and airborne contaminants, which can cause premature wear of the dies and crimp ring. It should care-
fully be removed without mixing it with newly applied NEVER-SEEZ.
2. Die cage maintenance should be performed at 1000-crimp intervals or every six months, which ever occurs
first. Die cages should be clean of grease and debris and inspected for worn or damaged components.
a. The sliding surface of the dies should appear smooth with no apparent galling. Galled dies
must be replaced. Individual dies in a cage can be replaced without replacing all eight dies.
b. Replace springs that show any sign of damage or collapse (are shorter than other springs).
c. The spring plate should appear smooth with no apparent galling.
Galled spring plates must be replaced.
d. Inspect remaining components and replace those that are badly worn.
3. Reassemble components and liberally apply NEVER-SEEZ to the die surface
which slides along the spring plate. Torque the die cage bolts to 50in.-lbs.
4. Ensure that all dies slide in and out freely.
Figure 5