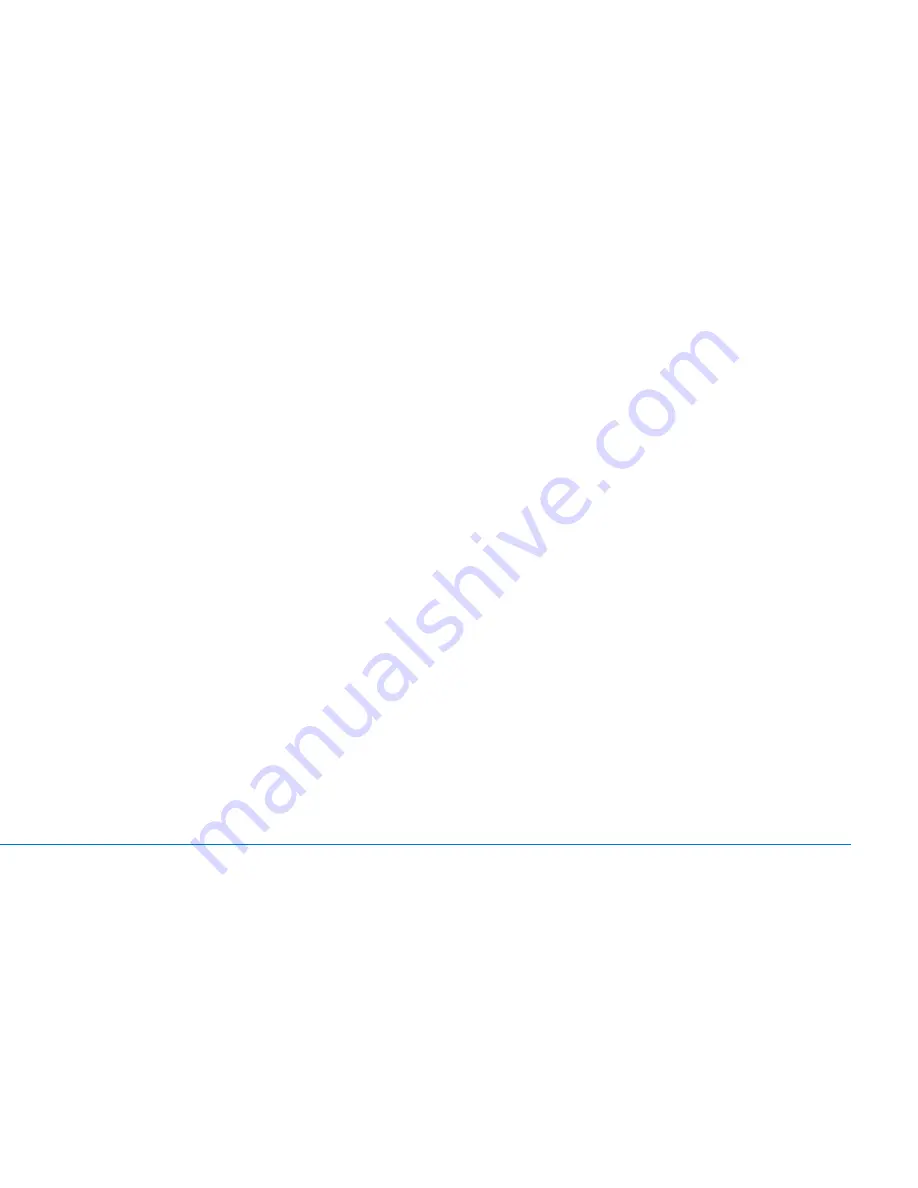
3
EATON
Duraforce HMR Conversion Procedures Manual E-MOPI-TM005-E July 2012
This manual will provide you with information and procedures
for general conversions of Eaton® DuraForce™ HMR
Regulated Variable Displacement Open and Closed Loop
Hydraulic Motors. Procedures outlined in this manual will
allow you to be more flexible with your inventory and better
service your customers. To ensure accuracy of conversion
and prevent part loss or damage, certain components
or subassemblies are disassembled, inspected, and
reassembled when removed from the motor.
Training
You have been provided information on the conversion of
DuraForce products. Proper application of the information
requires specific training and may require use of specialized
tooling and equipment. All requests for training must be
coordinated through your Eaton Account Manager. He can
also provide you price and availability of any specialized
tooling. If you choose to proceed with the conversion of the
DuraForce products absent the necessary training and/or
these specialized tools, you do so at your risk.
Eaton will accept no claim for warranty resulting from
deficiencies in the conversion. Please refer to the
Eaton literature web site for warranty information at
www.eaton.com/hydraulics/warranty.
Labeling Converted Units
All units that have been converted must retain the original
Eaton label and have a second Eaton label placed on the unit.
This second label at a minimum must state
Converted Eaton Model Code # (Final Eaton model code of
the converted unit)
Conversion done by (Name of your company)
Conversion Parts
All requests for specific conversion part information should
be addressed to your Eaton account representative.
Additional information can be found through your Eaton
customer connect portal. All requests or inquiries must be
accompanied by the complete model and serial number of
the base unit you want to convert.
Cleanliness
Cleanliness is extremely important when repairing a
hydrostatic pump or motor. Before disconnecting the lines,
clean foreign material from exterior of unit. Work in a clean
area. Clean all metal parts in clean solvent. Blow parts dry
with air. Don’t wipe parts with cloth or paper towel, because
lint or other matter could cause damage. Check all mating
surfaces. Replace any parts that have scratches or burrs that
could cause leakage. Don’t use coarse grit paper, files or
grinders on parts.
Environmental Concerns
Protection of the natural fundamentals of life is one of our
predominant tasks. We are continuously improving the
protection of the environment as far as applications are
concerned. We encourage you to contribute your share to
comply with this demand. In connection with work to be
performed, the environmental regulations of the machine
manufacturer must be respected.
In general:
• Greases and oils which cannot be used any more have to
be collected. They are normally a threat to water reserves
and must be kept away from the environment.
• Adhere to national and local regulations for waste disposal.
Seals
A good conversion policy is to replace all old seals with new
seals whenever units are disassembled. This avoids potential
damage during seal removal. Lubricate seals with petroleum
jelly. Use only clean and recommended oil when assembling
unit. Information on recommended filters and fluids can be
found in the Operational Parameters section.
Torque
All torque specifications are for lubricated threads. Bolts for
gasketed surfaces should be checked for proper torque.
Introduction
Exchanging Controls
• 6mm Allen wrench
• Torque wrench capable of
setting 32 N-m (24 ft-lb)
Exchanging Response
Orifices
• 3 mm Allen Wrench.
• 6 mm Allen wrench.
• Torque wrench capable of
32 N-m (24 ft-lb).
• Petroleum Jelly or clean
grease.
Maximum & Minimum
Displacement Adjustments
• 6mm Allen wrench
• 19mm closed-end wrench
Adjusting Crossover
Relief
• 5mm Allen wrench
• 17mm closed-end wrench
• 0-7000 psi pressure gauge or
transducer
Tools Required (continued)