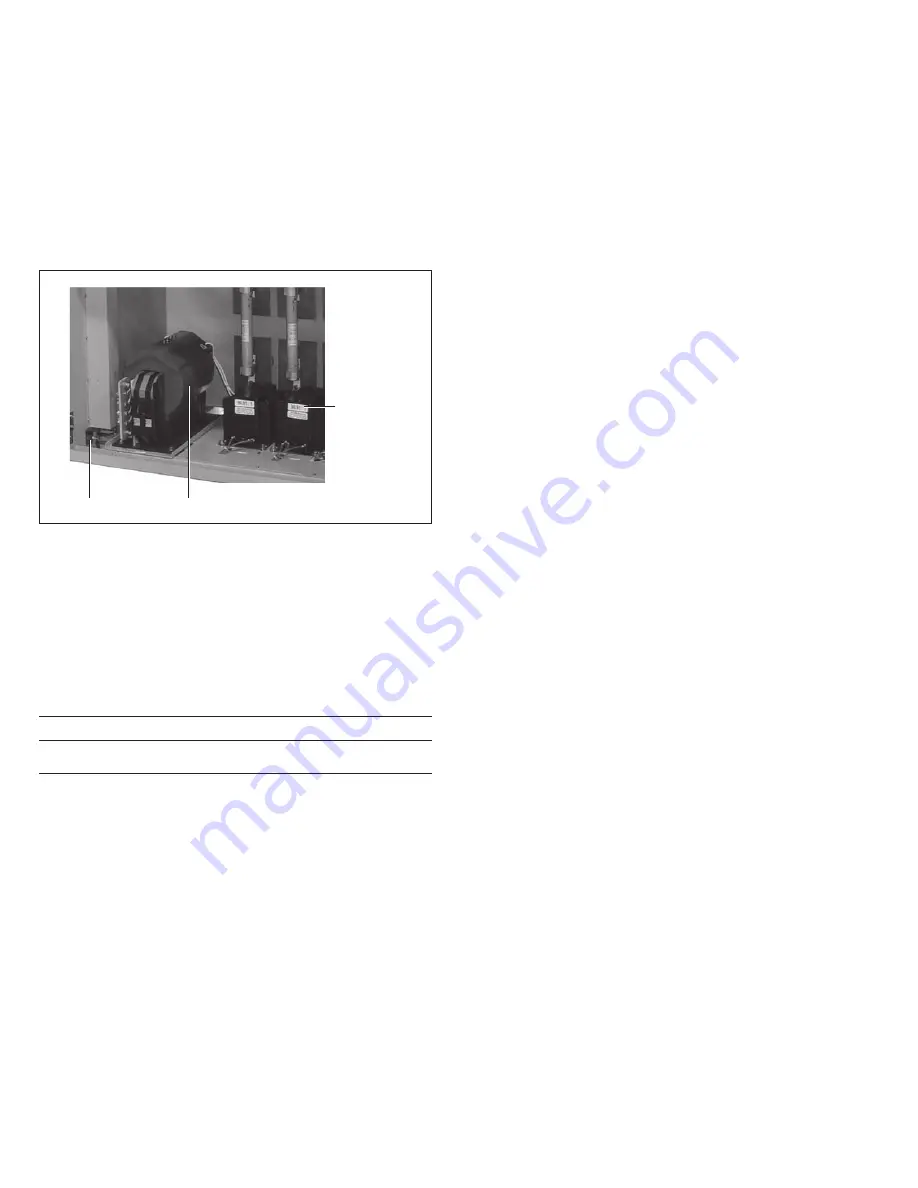
10
Instruction Booklet
IB48050
Effective September 2012
Instructions for installation,
operation, and maintenance of the
AMPGARD 15 kV, 300A vacuum starter
eaton Corporation
www.eaton.com
Some wiring may need to be connected to devices on the low
voltage door or in the low voltage compartment . Wiring to these
devices should come through one of the wire cutouts in the
bottom left of the low voltage compartment . Confirm that there
is sufficient slack in the wiring to allow the medium voltage door
to open properly .
A horizontal low voltage wireway is located at the bottom front
of each lineup . The equipment ground bus is also located in the
wireway . This area may be used to route control wires that must
pass from one structure to another .
Control Power Transformer
Ground Bus
Optional
Potential
Transformers
Figure 20. Ground Bus and CPT
Setting of adjustable protective devices
AMPGARD controllers may contain protective devices such as
solid-state motor protection relays, overcurrent relays, incomplete
sequence timers, and other devices critical to the proper operation
of the starter . Due to the wide variation in job site parameters, these
devices are not set at the factory . It is the purchaser’s responsibility
to ensure that all adjustable devices are properly set before
energizing the equipment . All warranty is void if adjustable devices
are not properly set prior to initially starting the equipment .
m
Danger
failure to properly set aDjustable Devices may result in
equipment Damage, personal injury, or Death.
pre-startup checks
Before attempting to put a newly installed controller into
service, study the wiring diagrams, control schematics, other
order specific drawings, and all instruction literature . Ensure that
all adjustable devices, including protective relays and timers, have
been properly set .
Verify that the controller and motor are connected per the Eaton
drawings . This is particularly essential in this class of equipment as
the fuse ratings, current transformers, and overload protection are
based on the characteristics of the particular motor (or other load)
to be controlled .
Ensure that all safety precautions have been taken and that the
installation conforms to applicable regulations and safety practices .
The equipment should be cleaned of dirt, scraps of wire, tools,
and other foreign material . The dielectric strength of the vacuum
interrupters should be checked before the contactor is energized
for the first time and regularly thereafter to detect at the earliest
possible date any deterioration in the dielectric strength of the
interrupter, because this may result in an interruption failure . The test
is best performed with the contactor removed from the controller
cubicle . Removal instructions can be found later in this IB in the
maintenance/contactor section . If testing is performed with the
contactor installed, care must be taken to ensure that no damage
is inflicted on the controller control power transformer, potential
transformers, or to the controller load . Removal of the primary
fuses is sufficient to protect the CPT or PTs . Cables to the load
should be disconnected . Although an AC test is recommended,
a DC test may be performed if only a DC test unit is available .
A good vacuum interrupter will withstand a 27 kV, 60 Hz test or
a 38 kV, DC test across the normally open contact gap . When
performing DC tests, the voltage should be raised in discrete
steps until the final test voltage is reached . When tested with an
AC high potential tester, expect a capacitance leakage current of
approximately 1 mA per interrupter . Refer to IB48051 for more
information on dielectric testing of the vacuum interrupters .
The insulation level of the starter should be checked and recorded
before the unit is energized .
Enclosure doors should close easily . Do not force doors closed, but
rather look for improperly positioned contactors, isolating switches,
or other devices .