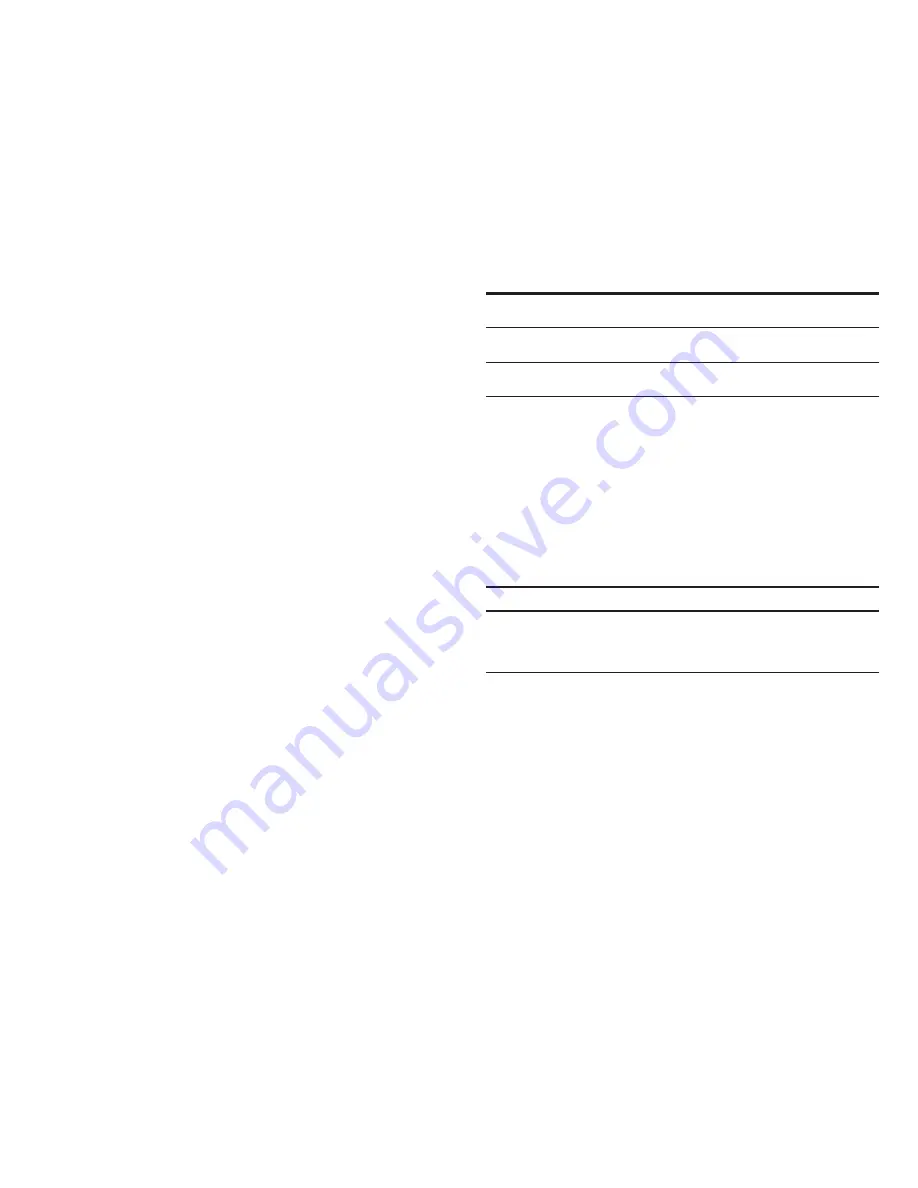
13
Instruction Book
IB182023EN March 2016 www.eaton.com
AMH-4.76-VR
Replacement Circuit Breaker
4.4.2 CLOSING OPERATION
Figure 4.6 shows the positions of the closing cam and tripping
linkage for four different operational states. In Figure 4.6.a the
breaker is open and the closing springs are discharged. In this state,
the trip latch is disengaged from the trip “D” shaft (unlatched). After
the closing springs become charged, the trip latch snaps into the
fully reset or latched position (Figure 4.6.b)
When the spring release clapper (Figure 4.5, Item 13) moves into
the face of the spring release coil (electrically or manually), the upper
portion of the clapper pushes the spring release latch (1) upward.
When the spring release latch moves, the cam shaft assembly is
free to rotate. The force of the closing cam (Figure 4.6.b, Item 5),
moving the main link (2), rotating the pole shaft (4) (which charges
the opening spring). This moves the three operating rods (3), closes
the main contacts and charges the contact loading springs (not
shown). The operational state immediately after the main contacts
close but before the spring charging motor recharges the closing
springs is illustrated in Figure 4.6.c. Interference of the trip “D” shaft
with the trip latch prevents the linkage from collapsing, and holds
the breaker closed.
Figure 4.6.d shows the breaker in the closed state after the closing
springs have been recharged. The recharging of the spring rotates
the closing cam one half turn. In this position the main link roller
rides on the cylindrical portion of the cam, and the main link does
not move out of position.
4.4.3 TRIPPING OPERATION
When the trip bar “D” shaft (Figure 4.6.b, Item 9) is turned by
movement of the shunt trip clapper (11), the trip latch will slip past
the straight cut portion of the trip bar shaft and will allow the banana
link and main link roller to rise. The energy of the opening spring and
contact loading springs is released to open the main contacts. The
mechanism is in the state illustrated (Figure 4.6.b) after the breaker
is tripped open.
4.4.4 TRIP-FREE OPERATION
When the manual trip button is held depressed, any attempt to close
the breaker results in the closing springs discharging without any
movement of the pole shaft or vacuum interrupter stem.
4.5 CONTROL SCHEMES
There are two basic control schemes for each series of Type VCP-WR
breakers, one for DC control and one for AC control voltages (Figure
4.3). Specific wiring schematics and diagrams are included with each
breaker.
There may be different control voltages or more than one tripping
element, but the principal mode of operation is as follows:
As soon as the control power is applied, the spring charging motor
automatically starts charging the closing spring. When the springs
are charged, the motor cut off LS1/bb switch turns the motor off. The
breaker may be closed by making the control switch close (CS/C)
contact. Automatically upon closing of the breaker, the motor starts
charging the closing springs. The breaker may be tripped any time by
making the control switch (CS/T) contacts.
Note the position switch (PS1) contact in the spring release circuit
in the scheme. This contact remains made while the breaker is
being racked between the TEST and CONNECTED positions for
appropriately retrofitted breakers. Consequently, it prevents the
breaker from closing automatically, even though the control close
contact may have been made while the breaker is racked to the
CONNECTED position.
When the CS/C contact is made, the SR closes the breaker. If
the CS/C contact is maintained after the breaker closes, the Y relay
is picked up. The Y/a contact seals in Y until CS/C is opened. The
Y/b contact opens the SR circuit, so that even though the breaker
would subsequently open, it could not be reclosed before CS/C was
released and remade. This is the anti-pump function.
4.5.1 TIMING
The opening and closing times for the circuit breakers vary
depending upon the control voltage, power rating, environment and
test equipment. Differences in timing are expected between initial
factory measurements and field inspections. Circuit breaker timing
can be measured by service personnel using available equipment
before installation and in conjunction with regular maintenance
periods to assist in tracking the general health of the breaker. Typical
ranges as observed using nominal control voltages are listed in
Table 4.
Tablt 4. Timt Ptr Evtnt
Event
Milliseconds / Maximum
Closing Time
(From Initiation of Close Signal to Contact Make)
75
Opening Time
(Initiation of Trip Signal to Contact Break)
45
Reclosing Time
(Initiation of Trip Signal to Contact Make)
190
4.6 SECONDARY CONNECTION BLOCK
The breaker control circuit is connected to the switchgear control
through secondary connection block, located at the lower left
rear of the breaker. The contacts engage automatically when the
breaker is racked into the “test” and “connect” positions. The
socket half of the connection is located in the cubicle and a jumper
of multiconductor cable can complete the control connections (for
testing) when the breaker is withdrawn from the cell.
4.7 INTERLOCKS
WARNING
INTERLOCKS ARE PROTECTIVE DEVICES FOR PERSONNEL AND
EQUIPMENT. DO NOT BYPASS, MODIFY, OR MAKE INOPERATIVE ANY
INTERLOCKS. DOING SO COULD CAUSE DEATH, SERIOUS PERSONAL
INJURY, AND/OR PROPERTY DAMAGE.
There are several interlocks built into the VR-Series vacuum
replacement breakers. Each of these interlocks, though different in
form, duplicate or exceed in function that of the original breaker.
These interlocks exist to safeguard personnel and equipment. The
basic premise behind the interlocking arrangement on the vacuum
replacement breaker is that the breaker must not be inserted into
or removed from a live circuit while the main contacts are closed.
Also considered in the interlocking is that the breaker should pose
no greater risk than necessary to the operator in or out of the cell.
In addition to the original interlocks, VR-Series breakers provide an
anti-close interlock.
4.7.1 ANTI-CLOSE INTERLOCK
The anti-close interlock prevents discharging of the closing springs if
the breaker is already closed (Figure 4.5, Item 11). When the breaker
is closed, the interlock component moves away from the spring
release clapper so that it cannot lift the spring release latch (9).
4.7.2 RACKING SYSTEM TRIP AND SPRING RELEASE
INTERLOCKS
The racking interlock prevents engaging or disconnecting a shut
breaker with live cell buss work or removing a mechanically
hazardous breaker from the cell. The basic premise of this interlock
is that no breaker should be connected to or removed from cell
primary circuitry when shut and no breaker should be removed
from the cell with charged open or closing springs. The racking