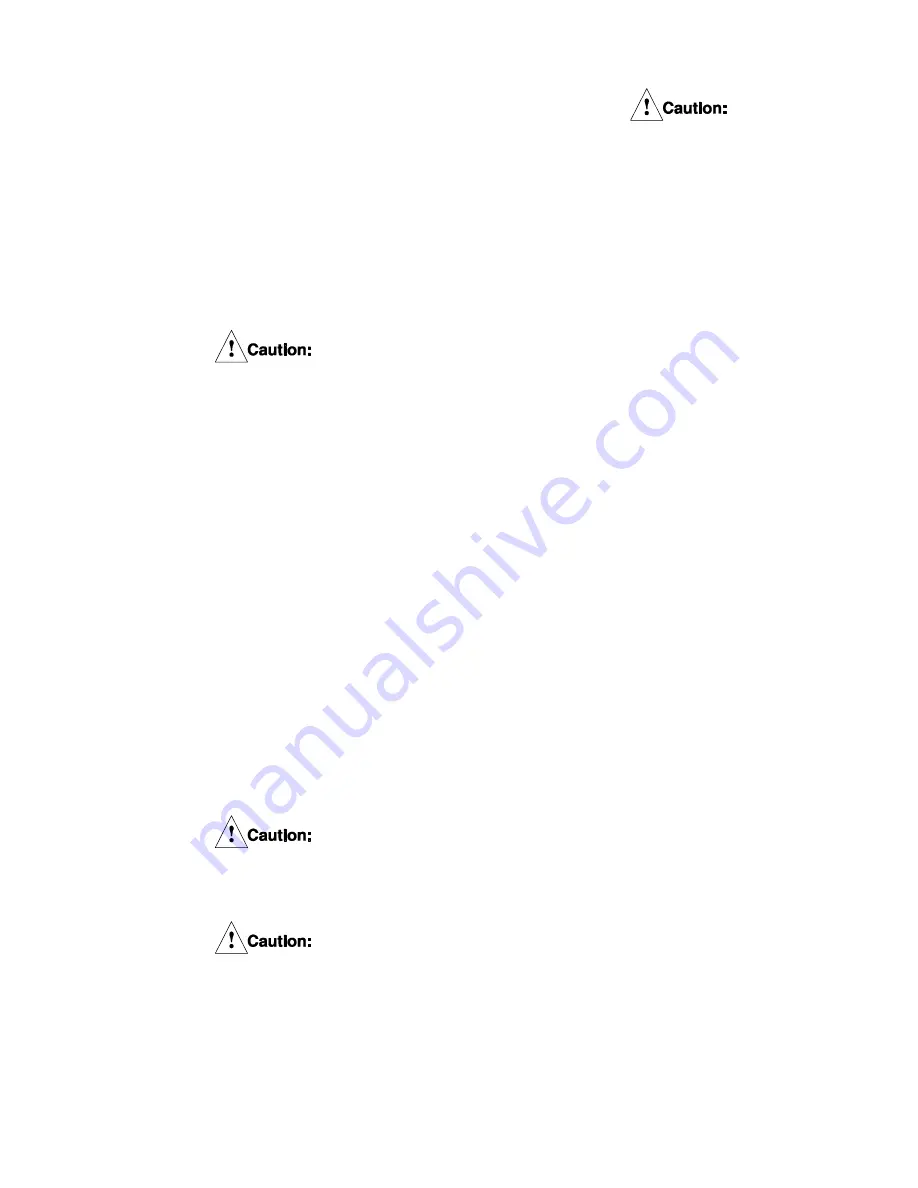
2.3.4
All pipes should be free of metal chips, cutting
compound and any other foreign matter. Pipe
ends should be reamed after cutting to elimi-
nate possible restrictions. For optimum air
system response, a minimum number of
bends and elbows should be used.
2.3.5
The WCB2 tensioner does not require lubri-
cated air; however associated control valves
may. Consult the valve manufacturer for
appropriate recommendations.
2.4
Coolant System
Make sure that the water inlets
and outlets are positioned as close
as possible to the 6 o’clock and 12
o’clock positions, respectively.
This will help to minimize the
formation of air pockets in the
water cavity during o p e r a tion,
which could contribute to
overheating of the tensioner.
2.4.1
Maximum allowable coolant pressure within
the water cavity is 40psi for size 36 and 48
WCB2 units and 45psi for all other sizes. See
Table 7 for coolant pressure limitations as
measured at the inlets and outlets of water
jackets. Note that inlet pressures exceeding
the maximum allowable static pressures are
only permissible under dynamic flow condi-
tions, provided that the average pressure
between the inlet and outlet does not exceed
the maximum allowable pressure stated
above. The use of an accumulator or
pressure relief valve may be desirable to
reduce the effect of pressure spikes in the
coolant system during operation.
High outlet pressures or surges
exceeding maximum allowable may
result in damage to the tensioner.
Maximum allowable water pressure
is dependent upon tensioner size
and specific application
requirements.
Inlet pressures exceeding the maxi-
mum allowable average pressure are
only permissible when the outlet
pressures are at or below the limits
listed in Table 7.
2.4.2
The coolant supply and discharge hose, pipe
and fitting sizes, along with minimum flow
rates for the tensioner rated horsepower,
are listed in Table 6.
2.4.3
Coolant supply connections to the tensioner
should provide a parallel flow through each
section of the tensioner. Series flow is not
recommended, as it can lead to overheat-
ing of the tensioner.
2.4.4
Inlet and outlet coolant manifolds must be
provided. Manifolds should be constructed to
allow for even flow through all ports. On
sizes 18" and larger, two hoses can be
routed to the reaction plates (30) to assist
with balancing the flow to each wear plate.
Note: Reaction plates (30) in WCB2 sizes 18"
and larger typically have two inlet and two
outlet ports to assist with obtaining balanced
flow to each cooling chamber. In the event that
a multiple disc tensioner includes an older style
reaction plate with only one inlet and one outlet
port, water flow should be restricted at the in-
lets to the pressure plate (13) and mounting
flange (1) to allow for equally proportional heat
dissipation at each cooling cavity.
See Figure 5.
2.4.5
Use flexible connecting hose to each
tensioner coolant section to allow axial
travel of the pressure plate, reaction plate,
and end plate during tensioner operation
without restricting the movement of compo-
nents. When determining hose lengths,
consideration should be given to movement
and location of the pressure plate and
reaction plate as friction material wears.
Hose lengths running between the
manifolds and the inlet or outlet ports
should be equal in length, if possible.
Reductions in the recommended line
diameter should be avoided to prevent
excessive line pressures.
WCB 11070 VP 4.2 Format
9
© Copyright Eaton Corp., 2003. All rights reserved
April 2002 (Revised June 2003)