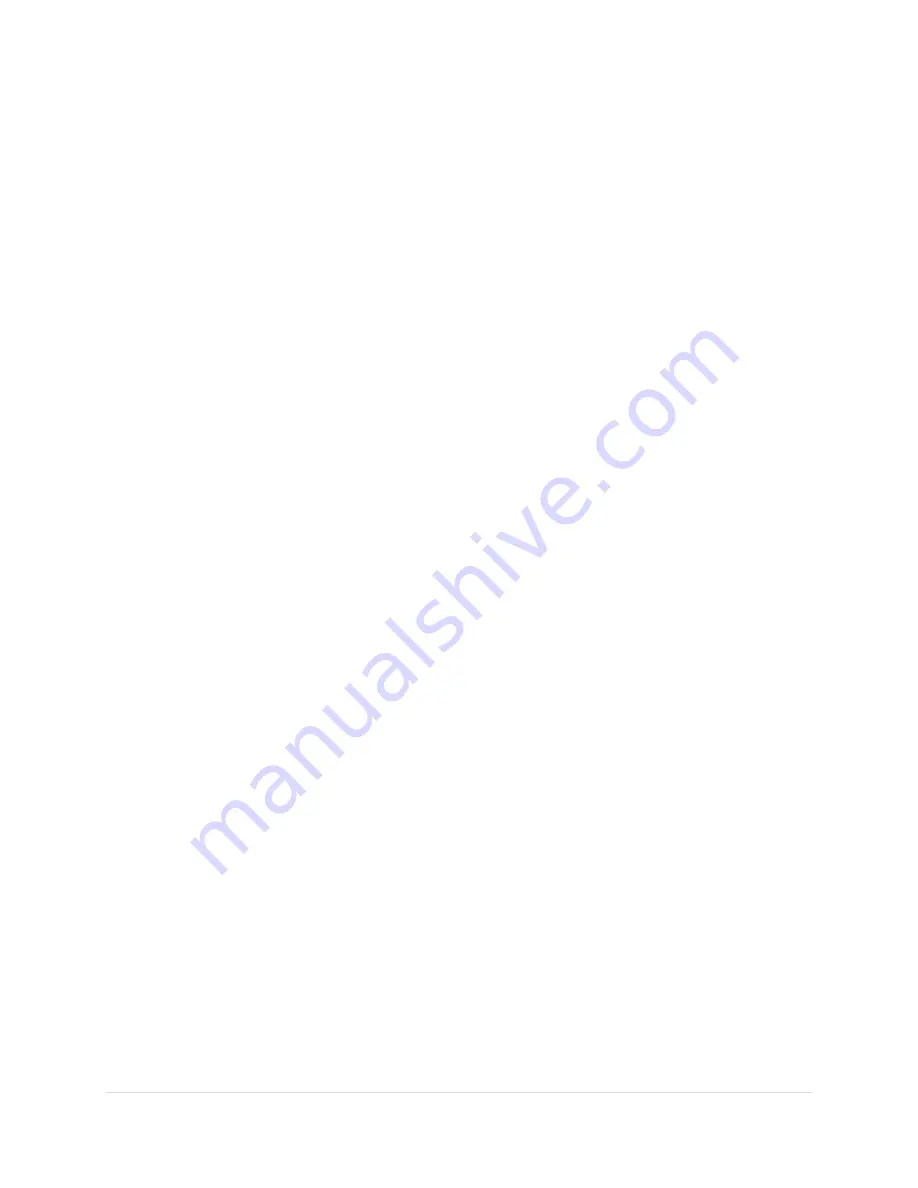
Polar Compressor Rotary Screw Compressors
Revision July.2015
www.eatoncompressor .com
877.283.7614
22 |
P a g e
Mechanical Components (Continued)
the oil particle size and can lower
content to less than 3 PPM. During
normal operation, the air/oil separator
filter can be used for about 2000 hours
or annually, whichever comes first.
Refer to the computer controls of the
compressor to monitor operating time
and remember to reset maintenance
timer when filter is replaced. There is an
automatic alarm that can be set to
remind operator of service times
12.
Safety Valve
The ASME certified safety valve on the
air/oil separator tank is set to open when
the pressure exceeds 175 PSI (12.1 bar).
NEVER attempt to operate machine
without ASME safety valve.
13.
Blow Down Valve
The blow down valve is a two-way valve
normally open. When the machine is
shut down or the compressor is
unloaded, the vent valve opens and
relieves pressure in the air/oil separator
tank to ensure the compressor will not be
started under load.
14.
Check Valve
A minimum pressure check valve is
installed after the air oil separator filter.
The starting pressure is set at over 43.5
PSI (3 bar). The functions of the
minimum pressure valve are as follows:
a)
Actuates oil lubrication of the air
end.
b)
Regulates air flow through the air
separator filter to prevent damage to
the separator filter element. Air flow
begins when pressure in the air / oil
separator tank reaches 43.5 PSI (3
bar).
c)
Prevents back flow from the air
receiver tank into the air / oil
separator tank. This component
serves as a built-in check valve. No
additional check valve is needed for
installation.
15.
After Cooler
The air flows through the check valve
then enters the after cooler. The fan on
the air cooled after cooler radiator draws
in ambient air and blows it through the
radiator cores to reduce heat in the
compressed air and lubricating oil
exhausted from the rotary screw pump.
The heat absorbed in the radiator cores is
discharged from the screw cabinet
because of the cooling fan and generally
reduces air temperature by 60˚F (15˚C).
If ambient air temperature exceeds
112˚F (45˚C), the System may overheat.
It is important to operate the compressor
in a well ventilated area for the cooling
process to be effective.
16.
Air Storage Tank
(optional, not shown)
The air storage tank can serve as cushion
to keep output pressure relatively stable.
It can also reduce operating temperature,
remove moisture content, provide
cleaner air and reduce the load of the
dryer. A larger tank also reduces the
cycling of the suction valve. As
a guideline, for every CFM the
compressor produces, a minimum of 1.2
gal. of air storage is needed.
17.
Refrigerated Dryer/Coalescing Filter
(optional, not shown)
The refrigerated dryer removes moisture
content. The coalescing filter removes
oil droplets and impurities in the
compressed air. The refrigerated
dyer/coalescing filter operates best with
an automatic drain that removes water
condensation collected during the air
drying process.
Operation
Safety Rules
1.
Make sure all operators receive
product training, read and understand
all instructions.