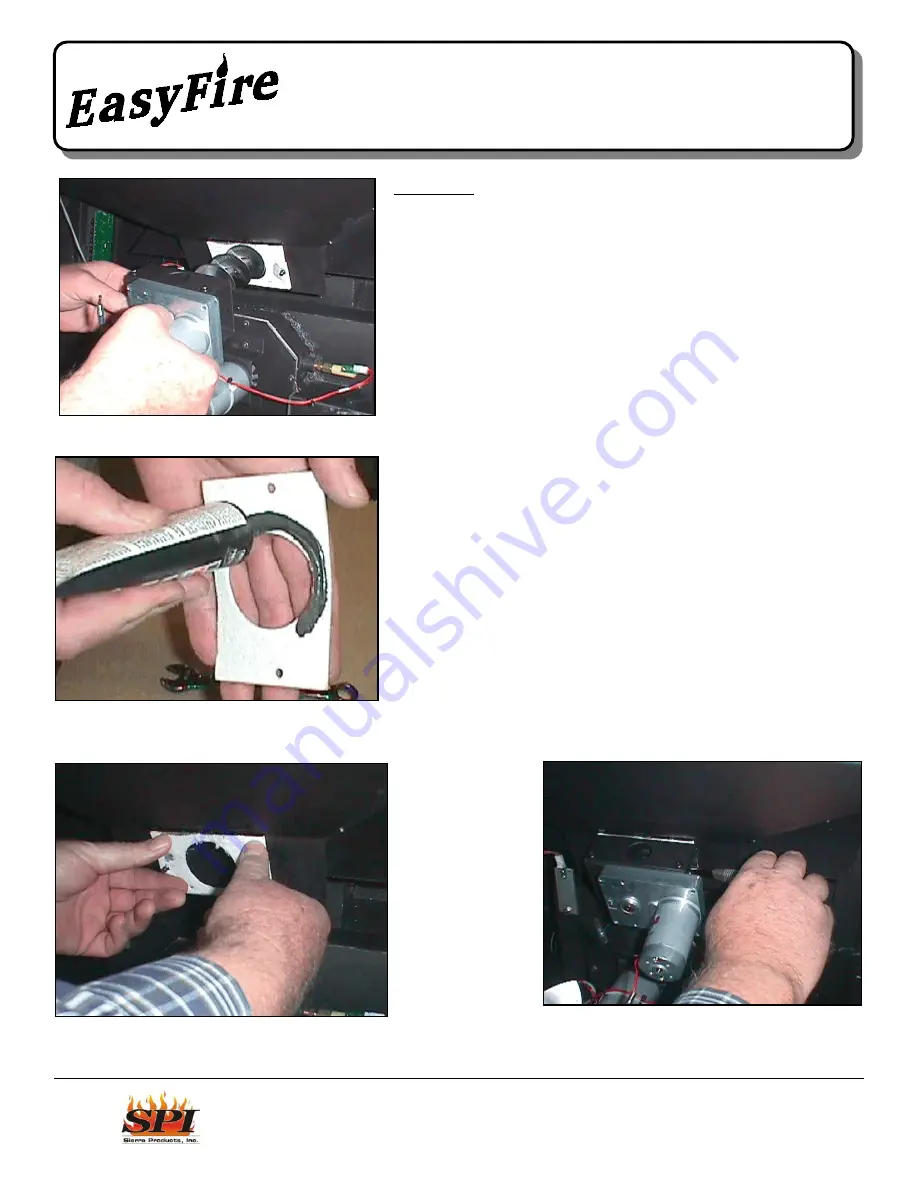
B Model General
Service Instruction
Figure 1
Figure 3
Figure 2
Figure 4
OVERVIEW
With one season of field service experience three service items have
been noteworthy and should be completed during the next unit service.
Feed System Gasket and Attachment Nuts
: Feed system
attachment in past EF units had been accomplished with wing nuts.
We have noted that the nuts tightened by hand may not be sufficient to
properly secure the feed drive. If the drive become loose the feed
gasket may fail and allow saw dust to fall into the cabinet. To correct
this we have available 10-24 washer locking nuts to replace the wing
nuts. Replacement of the feed gasket should include gluing the gasket
to the bottom of the feed hopper using silicone sealant.
1) Remove the units rear panels to gain access to the feed drive.
Empty the hopper of fuel. Loosen and remove the wing nuts.
Lower the feed drive from the hopper
(Figure 1)
. Remove old
gasket.
2) Apply automotive type silicone gasket material around feed drive
hole
(Figure 2).
3) Press silcone applied gasket side to bottom of hopper
(Figure 3)
.
4) Carefully install feed drive so as to not damage gasket. Install new
lock nuts and tighten with 3/8 wrench (
Figure 4).
Note: silicone gasket material should squeeze out from edges both
inside hopper and out. Remove excess silicone.
*** Prior to re-installing back panels complete the following services ***
Sensor and Switch Harness Connections:
These digital
components connect to the main circuit board through the main wiring
harness. The
connections
utilize industry
standard pin and
sockets.
Operating at low
DC voltage these
connections are
subject to
vibration, dust,
and moisture. To
minimize the loss
of contact these
three connections
should be coated
with a small
amount of
63 Laxalt Dr. Carson City, NV 89706
775-241-2586 Fax 775-241-2704
www.sierraproductsinc.net
P/N B Model General Service 09 01/09
19