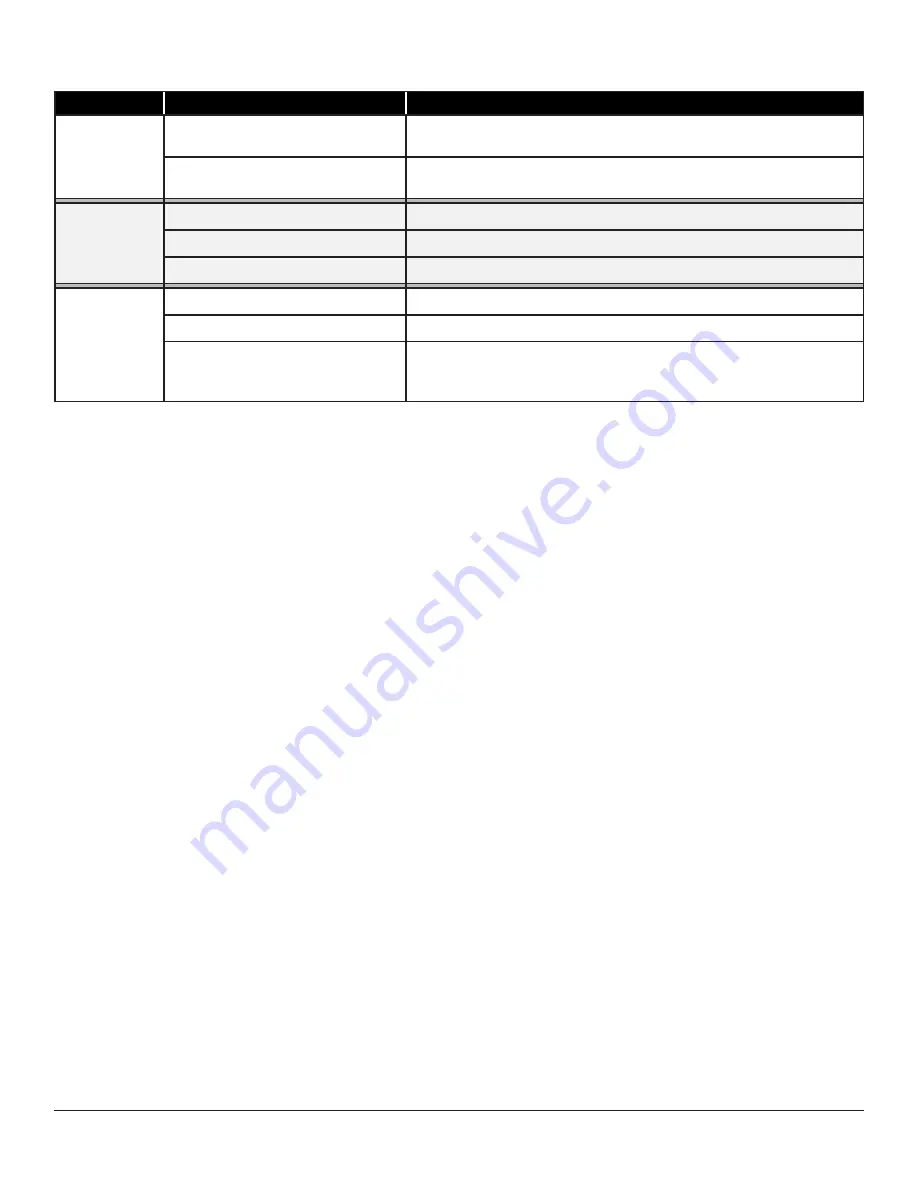
To order parts and supplies: 800.343.9353 >> eastwood.com
29
TIG WELDING TROUBLESHOOTING
PROBLEM
CAUSE
CORRECTION
Crater in the
End of the Weld
Bead
Insufficient Shielding
Keep the Torch on the base metal while the post flow shielding gas flows to
protect and cool the metal and Tungsten.
Not Enough Filler Material
Reduce current and add more filler at end of weld. It may also be beneficial to
back step to ensure no crater will form.
Weld Bead is
Cracking
Too Much Heat in Material
Reduce heat and allow more time between passes.
Base Metal is Absorbing Too Much Heat
Preheat base metal (consult welding codes for requirements)
Incorrect Filler Wire
Use appropriate filler wire type and diameter for the joint being welded.
Material is
Warping
Insufficient Clamping
Clamp work piece tightly and weld while clamps are in place.
Insufficient Tack Welds
Add more tack welds until rigidity and stiffness is developed.
Too Much Heat in Material
To reduce heat it is best to spread the welding out around the area. This can be
done by using stitch welding techniques, alternating sides, and/or taking your
time and allowing the pieces to cool between passes.