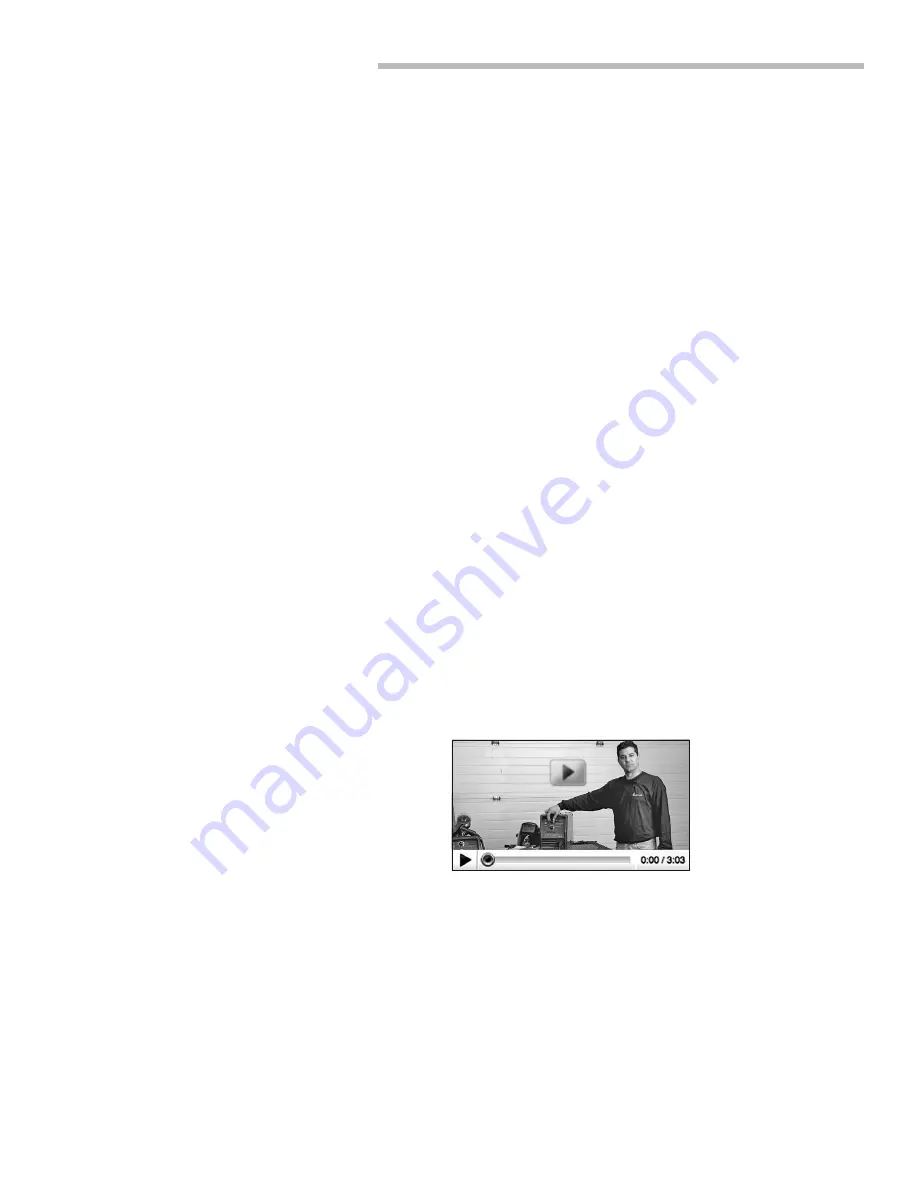
To order parts and supplies, call 1-800-345-1178 or visit www.eastwood.com
9
WELDING PROCESS
1.
Please refer to “Suggested Settings” chart in the unit and select proper settings based on the material
and thickness.
2.
Adjust output polarity according to the welding wire and to ensure whether or not the protective gases
are needed. This welder comes set to weld with gas. If welding gasless with fl ux core, polarity must be
changed.
3.
Connect the ground clamp to the work pieces that are to be welded. This connection should be good
and secure.
4.
Your welding torch should have clear access to the work piece
5.
Wearing your welding helmet, gloves and long sleeve shirt and pants, press the trigger of the welding
gun and begin to weld. Keep the nozzle of the welding torch approximately 1/4” away from the work
piece.
6.
Use a “Push” technique which means you will be holding the gun in your right hand with the nozzle
and gun tilted back about 10-20 degrees and pushing the gun or moving from right to left.
7.
Once you depress the trigger the wire will arc and you will notice a molten puddle from. You want to
“move” this puddle to the left following the seam or areas to be welded.
8.
If you “burn through” the material you are moving too slowly or your heat setting is too high.
9.
The sound of bacon frying is what you are after. Start with the initial setting on the chart and increase
or decrease wire speed to obtain the best weld
10.
Release the trigger of the welding torch to stop welding
11.
After welding, close the valve on the bottle (if gas is used) and then press trigger of the welding torch
to release any gasses left in the hose. Finally, power off the welding machine
13.
If you’re welding patch panels or quarter panels on use the “stitch” type method. Depress the trigger
momentarily to form a small puddle or single bead. Then depress again to form another bead aside of
the fi rst. Continue until you have 4 or 5 small beads connected about 1⁄2-3/4” in length.
13.
Move to the other end of the panel and repeat the process. Now go to the middle and repeat. Con-
tinue this process moving to different areas of the panel to eliminate heat warping the material.
Visit Eastwood.com
to see our welding videos!