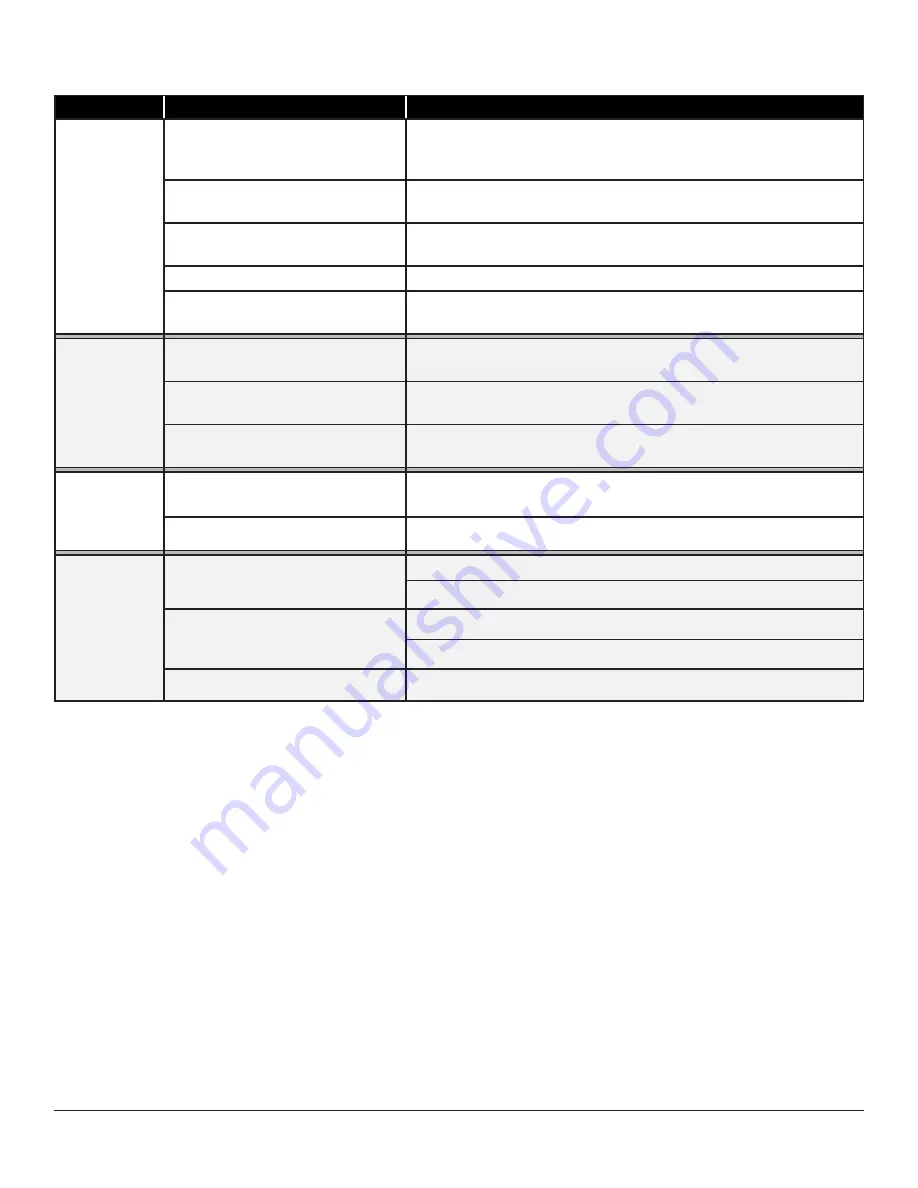
To order parts and supplies: 800.343.9353 >> eastwood.com
19
PROBLEM
CAUSE
CORRECTION
Weak Blast
Stream
Compressor Inadequate Causing
Insufficient Volume of Air (CFM)
to Operate Tool
Verify sufficient air supply to tool. Minimum requirement = 12 CFM @ 90 PSI.
Air Supply Line from Compressor
Too Small
Use air supply line of 3/8” or greater.
Air Supply Line from Compressor
Too Long
Limit air supply line to 25’ or less.
Pinched or Damaged Media Suction Line
Replace suction hose. Automotive fuel or heater hose works well.
Moisture or Other Contamination in
Air Supply
Check for and eliminate source of moisture in air line and blast gun.
Media Surging
Moisture in Media and or/Air Supply
Install a moisture separator capable of removing all moisture and impurities
from the air supply.
Debris or Blasting Residue in Gun Nozzle
Clean out gun nozzle then drain and sift blast media to remove debris
before re-use.
Excessive Media in Hopper
For best results, operate blaster with the Pick-up Tube inlet buried several
inches in media. 50 lbs. of media is generally sufficient.
Media Stream
Suddenly
Stops
Dirt or Debris in Media Suction Line
to Gun
To dislodge blockage, with lid closed, place a blast gloved finger over the
nozzle outlet and momentarily depress Foot Pedal.
Contaminated Media
Drain and sift blast media to remove debris before re-use.
View in
Cabinet
Becomes
Obstructed
Dust is Clogging Filter
Operate Filter Plunger to shake dust form Filter.
Clean Filter per procedure in Maintenance Section.
Filter Housing is Full of Dust
Empty Filter Housing per procedure in Maintenance Section.
Clean Filter per procedure in Maintenance Section.
Plastic Peel-Off Shield is Worn
Clean inside of window and replace Peel-off shield.
TROUBLESHOOTING