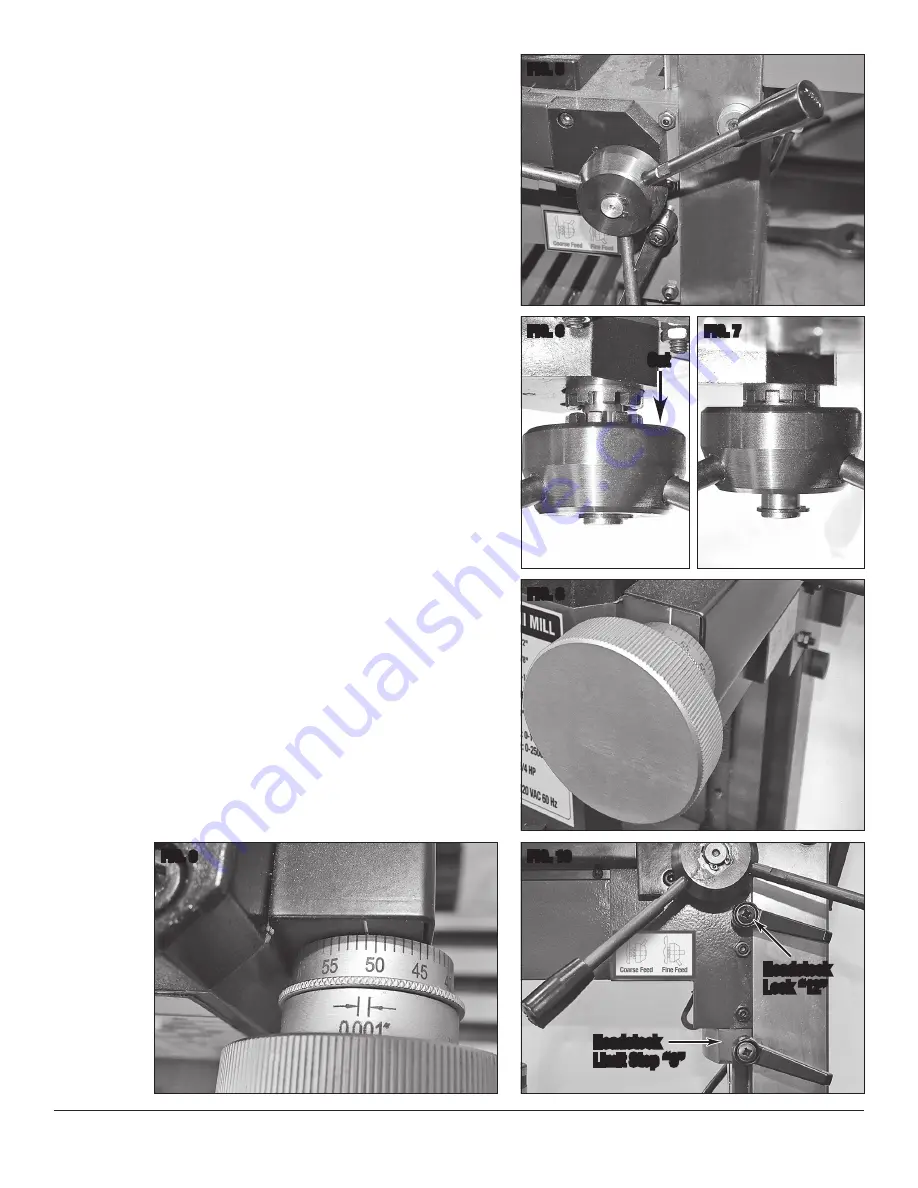
To order parts and supplies: 800.343.9353 >> eastwood.com
9
• The Headstock vertical travel is controlled by the Downfeed Handwheel
“10”
(FIG 5)
which drives a pinion gear along a Column mounted toothed rack.
It has both “Coarse” and “Fine” adjustments as described below:
- The “Coarse” adjustment provides a faster downward motion when
using as a drill press or as a rough positioning adjustment for precision
cutting operations. For “Coarse” adjustment, pull the Downfeed
Handwheel out to disengage the Castellated Drive Collar, allowing it to
turn
(FIG 6)
.
NOTE:
The Gauge and Pointer for the “Coarse” adjustment are
located at the left side of the Column.
- To lock in the “Fine” adjustment, push the Downfeed Handwheel in to
engage the Castellated Drive Collar
(FIG 7)
.
• The vertical Headstock travel is then finely adjusted by the Fine Downfeed Hand-
wheel
“11”
which provides a “fine tuning” precise positioning of the Headstock
along the Column
(FIG 8)
.
• Rotate the Fine Downfeed Handwheel Clockwise to lower the Headstock and
Counterclockwise to raise it. The Fine Headstock Handwheel moves the Head-
stock vertically 0.060” per revolution in fine increments of 0.001” as indicated
on the Pointer and Radial Gauge
(FIG 9)
built into the base of the Fine Downfeed
Handwheel
“11”
. Note that the Radial Gauge can be rotated to allow for indexing.
NOTE:
Refer to “Backlash Compensation” section of this Manual.
• The Headstock Limit Stop
“9”
limits the downward travel of the Headstock which
serves to limit depth of travel cut
(FIG 10)
.
• The Headstock Lock
“12”
locks the vertical position of the Headstock on the
Column
(FIG 10)
.
FIG. 8
FIG. 9
FIG. 10
Headstock
Lock “12”
Headstock
Limit Stop “9”
✓
✓
FIG. 5
✓
Out
FIG. 7
FIG. 6