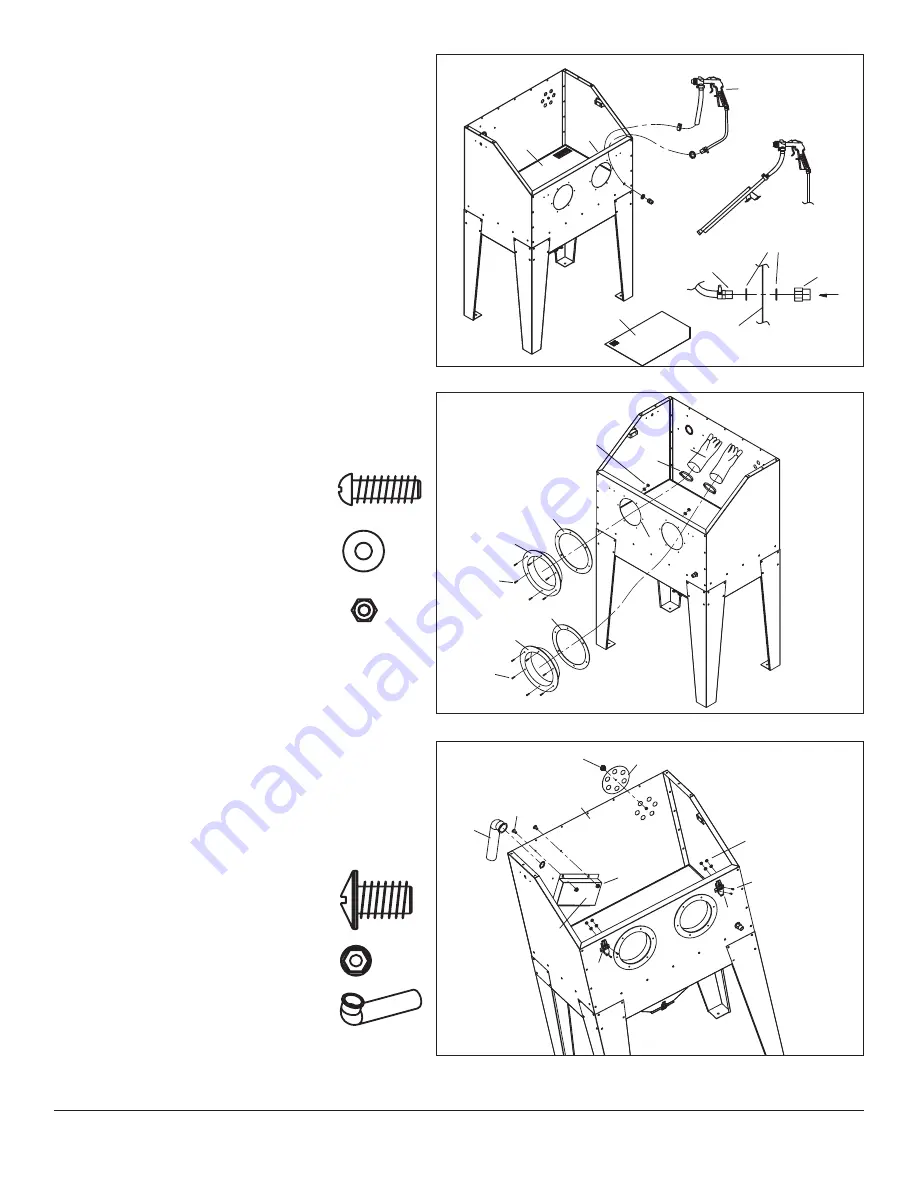
To order parts and supplies: 800.343.9353 >> eastwood.com
9
INSTALLING
REMAINING COMPONENTS
1.
Stand assembled unit up on it’s legs
(FIG. 15)
.
2.
Tighten leg screws to ensure unit sits level.
3.
Install the Media Blasting Gun (W) Suction Hose to the Media
Suction Tube (O), secure with a Hose Clamp and tighten
(FIG. 15)
.
4.
Place the Media Blasting Gun (W) Air Supply Hose Fitting through
the through hole in the lower right corner of the Cabinet Front
Panel (H) using a large flat washer on either side. Wrap thread
sealing tape around fitting threads and secure with the
Air Supply Fitting Nut
(FIG. 15)
.
5.
Let the Media Blasting Gun (W) hang out of the right front corner
of the Cabinet
(FIG. 15)
.
6.
Set the Shelf (B) (with angled cut off corner toward right front of
cabinet) and allow it to rest on the hopper flanges and Shelf
Floor Support (Q)
(FIG. 15)
.
7.
From the outside, install 2 sets of Seal Rings (U) and Glove Seats
(V) into the large holes in the Cabinet Front Panel (H) and secure
with twelve M4 x 16mm screws (BB), flat washers, (GG) and nuts
(FF)
(FIG. 16)
.
8.
Fit 2 Hose Clamps (S) over the Glove Sleeves then slide the Gloves
(R) fully over the Glove Seats (V) then tighten Hose Clamps (S)
securely
(FIG. 16)
.
NOTE:
Be sure to install left and right hand
gloves on the correct side and position them with thumbs upward.
9.
From the outside, install the Air Input Regulating Disk (LL) over the
six hole array on the upper rear corner of the Cabinet Back Panel
(C) and secure with Knob Screw (MM)
(FIG. 17)
.
10.
From the inside, install the Vacuum Elbow (SS) with grommet.
Next, install the Vacuum Baffle (X) over the vacuum hole on the
upper left corner of the Cabinet Back Panel (C) and secure with
four M6 x 12mm screws (AA) and nuts (EE)
(FIG. 17)
.
FIG. 15
FIG. 16
FIG. 17
H
B
W
Air Supply
Hose Fitting
Washer
Air Supply
Fitting Nut
Air Flow
H
H
S
R
U
V
BB
V
U
BB
FF, GG
AA
C
MM
LL
FF, GG
CC
EE
X
M
M
H
12 Pcs. BB M4 x 16mm Screw
12 Pcs. GG M4 Washers
12 Pcs. FF M4 x 12mm Screw
B
4 Pcs. AA M6 x 12mm Screw
4 Pcs. EE M6 Nut
1 Pc. SS Vacuum Elbow
SS