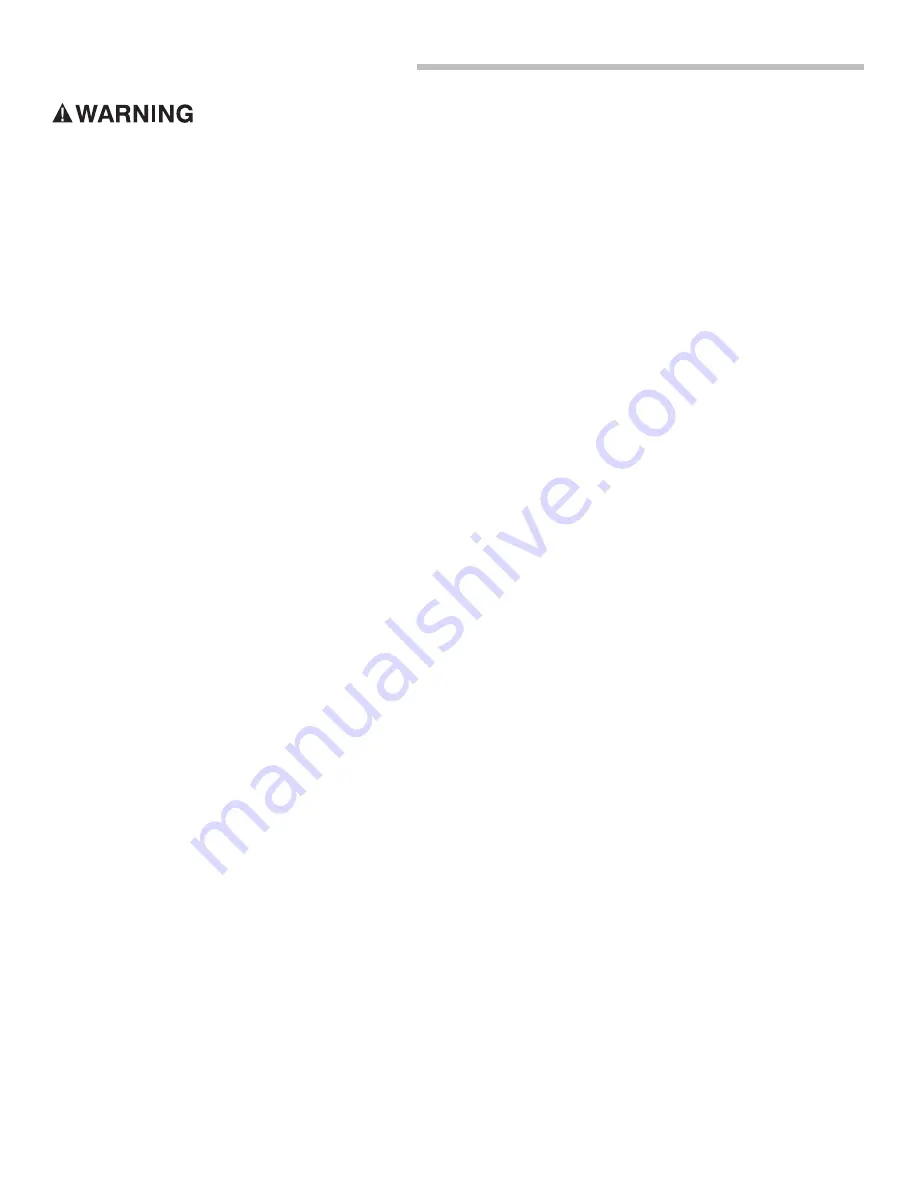
To order parts and supplies, call 1-800-345-1178 or visit www.eastwood.com
3
SAFETY INFORMATION
Pressure blasters and blast cabinets emit abrasive particles under high pressure.
Adequate respiratory, eye, and body protection must be utilized at all times during product operation.
Inhalation of silica based blast media particles have been known to cause cancer and other deadly
diseases and must be avoided. Always wear NIOSH approved respiratory protection when operating
this equipment.
•
Do not use any sand or silica based abrasives with this blaster. Silica based abrasives have been
linked to severe respiratory disease.
•
Read the manual carefully before beginning. Learn the blaster’s applications and limitations as
well as potential hazards.
•
The Soda Blasting side of the equipment is color coded GREEN and the Abrasive Blasting side
is color coded RED. DO NOT attempt to put Soda Media in the RED side or Abrasive Media in
the GREEN side. Damage to the equipment and operator injury can occur. Note: If this should
occur, stop work immediately, disconnect from air supply, release all pressure and drain tank by
removing cap and inverting unit. Replace cap, repressurize unit and purge all remaining media
from valves and hose.
•
Keep work area clean and well lit. Cluttered or dark work areas invite accidents.
•
All children should and pets should be kept away from the work area. Never let a child operate
the abrasive blaster.
•
Do not operate this tool if under the infl uence of alcohol or drugs. Read warning labels on pre-
scriptions to determine if your judgment or refl exes are impaired while taking drugs. If there is
any doubt, do not attempt to operate.
•
Use safety equipment. Eye protection should be worn at all times when operating this tool. Use
ANSI approved safety glasses. Everyday eyeglasses are NOT safety glasses. NIOSH approved
respiratory protection, non-skid safety shoes, blast hood, hard hat, and hearing protection
should be used in appropriate conditions.
•
Wear proper clothing. Loose clothing, neckties, rings, bracelets, or other jewelry may present a
potential hazard when operating this equipment. Please keep all clothing clear of the tool.
•
Don’t overreach. Keep proper footing and balance at all times when operating this product.
•
Always disconnect the air supply and release pressure from the tank before refi lling media, stor-
ing, servicing, or changing accessories. Such preventative safety measures reduce the risk of
releasing pressure accidentally.
•
Use clamps or other practical means to secure and support the work piece to a stable platform.
Holding the work by hand or against your body may lead to a loss of control and result in severe
injury.
•
Check for damage regularly. If any part of the tool is damaged it should be carefully inspected
to make sure that it can perform its’ intended function correctly. If in doubt, the part should be
repaired. Refer all servicing to a qualifi ed technician. Consult Eastwood for advice.
•
Always check to make sure that the dead man valve is not open before connecting blaster to air
supply. Blaster may cause damage to property or person if connected to air while the dead man
valve is open.
Continued...