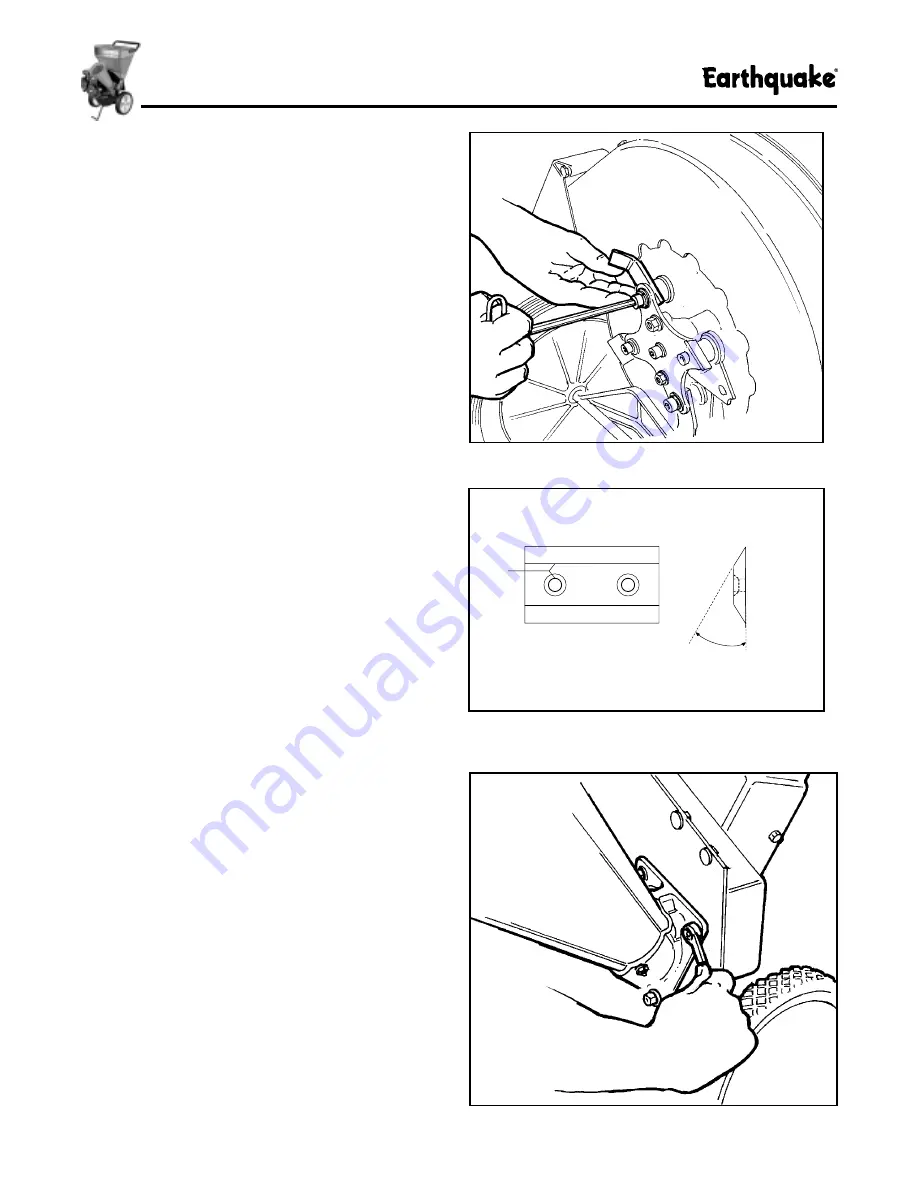
23
TROUBLESHOOTING AND REPAIR
assembly before attempting to start unit. Do not
attempt to start unit if extra hardware is left over
after reassembly is complete. Check all hammer
assemblies before proceeding.
Chipping Knives
Chipping knives should be resharpened or replaced
when tree limbs and branches require extra force to feed
completely into the chipper block.
Chipping knives may be resharpened until the distance
between the mounting holes and the top corner of the
blade bevel is 1/16” apart. (See Figure 16.)
To inspect and service the cutting knives, follow these
steps:
1. Turn engine off, allow rotor to stop completely,
and disconnect spark plug wire.
2. See Figure 10. Detach the shredder hopper from the
rotor housing leaving the liner and handle in place on
the hopper.
3. See Figure 17. Using an 1/2” box wrench or socket
remove the chipper cone to expose the oval chipping
block and one chipping knife.
4. Using a 1/4” hex wrench, loosen and remove the two
socket head cap screws holding the chipper knife in
place (access the screw heads from the rear of the
unit), and remove the chipper knife. See Figure 18 for
location and temporary removal of an access plug
that permits removal of the capscrews.
5. See Figure 19. Remove both knives through the
opening in the front of the chipper/shredder, and
sharpen equally or replace both blades to ensure
proper balancing and correct chipping action.
NOTE: Slow-speed water-cooled grinding is
suggested to help maintain blade temper and a long-
lasting sharp edge. Rapid grinding and heating of
blades will soften the edges, making repeated
sharpening necessary.
Chipper knives require a 30° bevel on the cutting
edge (see Figure 16) for efficient chipping action.
Contact your local dealer or blade sharpening
service if you prefer not to sharpen the blades
yourself.
6. Clean the chipper knife mounting areas before
reinstalling the blades to ensure a flat mounting
surface.
Figure 15. Reassembling Shredder Hammer
30
°
Top View
Side View
Figure 16. Chipper Knives Minimum Cutting Edge
Figure 17. Removing Chipper Cone to Expose
Chipping Knives